SmCo Mıknatıslar Nasıl Üretilir?
İçindekiler
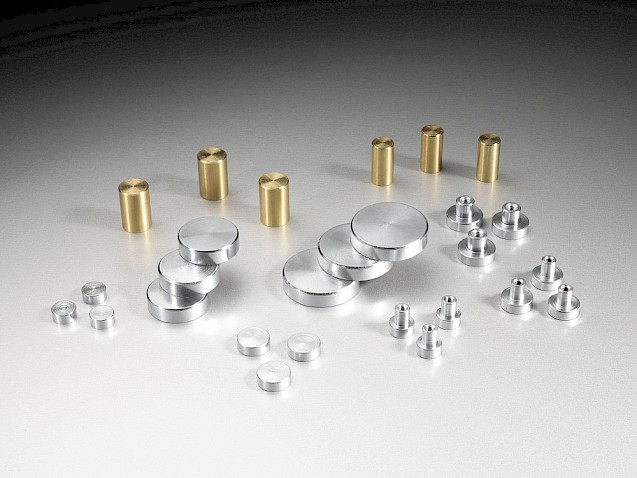
Samaryum ve kobalt karışımından yapılmıştır, SmCo mıknatıslar birçok yüksek teknoloji sektörünün temel dayanağıdır. Özellikle yüksek sıcaklıklarda, bu mıknatıslar kararlılıkları ve dayanıklılıklarıyla ünlüdür. Peki SmCo mıknatıslar nasıl üretilir? Son derece güçlü mıknatısların üretiminin ardındaki karmaşık yöntem bu sayfada size rehberlik edecektir. Malzeme hazırlamadan son rötuşlara kadar, mıknatısların gerektiği gibi çalışmasını garantilemek için her aşama hayati önem taşır. Bu kılavuz, bir proje için SmCo mıknatıslarına ilginiz olsun veya üretim sürecine hayran olun, ihtiyacınız olan tüm bilgileri sağlayacaktır.
SmCo Mıknatıslar Nelerdir?
Esas olarak samaryum ve kobalttan yapılmış olan SmCo mıknatıslar (samaryum-kobalt mıknatıslar olarak da bilinir) nadir toprak mıknatıslarıdır. Bu mıknatısların mükemmel manyetik nitelikleri (yüksek manyetik enerji ve korozyon direnci dahil) iyi bilinmektedir. Havacılık, askeri ve yüksek performanslı motorlar gibi özel kullanımlarda, 350°C'ye kadar yüksek sıcaklıklara dayanma kapasiteleri onları özellikle önemli hale getirir. SmCo mıknatıslar, diğer mıknatısların aksine çok zorlu koşullar altında manyetizmalarını korudukları için birçok farklı alanda faydalıdır.
Yaygın SmCo Mıknatıs Türleri
SmCo 1:5 ve SmCo 2:17, iki temelde iki çeşit SmCo mıknatısıdır. Bileşimleri ve manyetik nitelikleri, ikisini temelde farklı şekilde tanımlar. Bir kısım samaryum ve beş kısım kobalttan oluşan SmCo 1:5 mıknatıs, iyi bir kararlılık ve yüksek enerji sağlar. Buna karşılık, SmCo 2:17 mıknatıslar daha da büyük bir manyetik enerji ürününe ve daha büyük bir samaryum konsantrasyonuna sahiptir. çeşitli kullanımlar, her iki türün de çeşitli biçimlerini ve boyutlarını gerektirir.
SmCo 1:5 Mıknatıslar
Bir kısım samaryum beş kısım kobaltla birleştirildiğinde SmCo 1:5 mıknatıslar elde edilir. Bu mıknatıslar maliyet etkinliği, sıcaklık kararlılığı ve manyetik güç arasında güzel bir karışıma sahiptir. Özellikle yüksek sıcaklıklara karşı direncin gerekli olduğu ve mütevazı manyetik gücün yeterli olduğu kullanımlarda faydalıdırlar. Hem endüstriyel hem de otomotiv sektörleri SmCo 1:5 mıknatısları kullanan motorları, sensörleri ve aktüatörleri oldukça yaygın bulmaktadır. Genellikle SmCo 2:17 muadillerinden daha ucuzdurlar ve daha az performans gereksinimi olan kullanımlar için mükemmeldirler.
SmCo 2:17 Mıknatıslar
Yaklaşık her on yedi parça kobalt için iki parça samaryum, SmCo 2:17 mıknatıslar daha yüksek bir samaryum konsantrasyonuna sahiptir. Bu nedenle manyetik enerji ürünleri SmCo 1:5 mıknatıslarından daha fazladır. Üstün manyetik güç, sıcaklık direnci ve uzun ömür SmCo 2:17 mıknatıslardan bol miktarda bulunur. Hem yüksek manyetik enerjinin hem de artan sıcaklıklarda kararlılığın gerekli olduğu yüksek performanslı motorlar, manyetik sensörler ve havacılık uygulamaları bunlara sıklıkla başvurur. Zorlu uygulamalarda tercih edilmelerine rağmen, SmCo 2:17 mıknatıslar daha iyi performansları nedeniyle genellikle SmCo 1:5 mıknatıslardan daha maliyetlidir.
SmCo Mıknatısının Proses Akışı
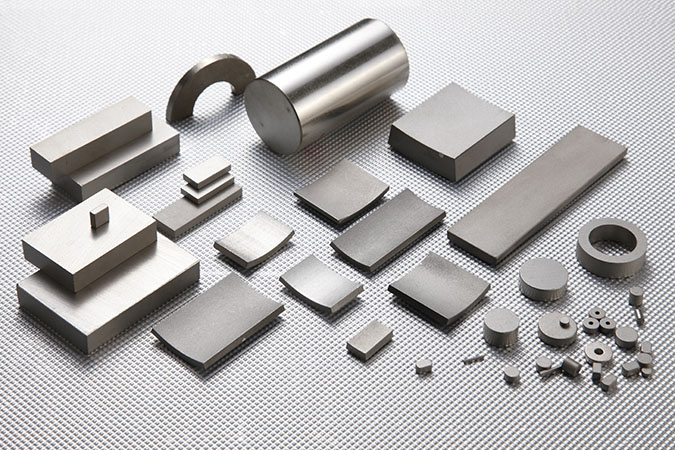
SmCo mıknatısları yapmak, her biri mıknatısın nihai niteliklerini tanımlamaya yardımcı olan birkaç işlemle çok kesin bir prosedürdür. En ufak işlem değişikliği bile SmCo mıknatıslarının performansını etkileyebileceğinden, üretim yolu doğruluk ve bilgi gerektirir. Bu bölümde her aşamayı daha ayrıntılı olarak inceleyeceğiz ve özellikle bu mıknatısların endüstri standartlarını ve belirli uygulama kriterlerini karşılamak için nasıl özenle yaratıldığına dikkat edeceğiz.
Adım 1: Malzeme Hazırlığı
SmCo mıknatısları yapımında ham maddelerin dikkatli seçimi ve işlenmesi ilk sırada gelir. Samaryum (Sm) ve kobalt (Co), çoğunlukla SmCo mıknatıslarını oluşturur. Bu iki malzemenin mükemmel manyetik nitelikleri, onların seçilmesine yol açtı. Nadir toprak elementi samaryum, yüksek manyetik alandan sorumludur; kobalt, mıknatısın kararlılığını ve korozyon direncini artırır.
Genellikle, ham bileşenler ayrıca demir (Fe), bakır (Cu) ve zirkonyum (Zr) ve hafniyum (Hf) dahil olmak üzere diğer eser metallerin dakika konsantrasyonlarını içerir. Bu ekstra bileşenler mıknatısların daha iyi genel manyetik performansa, sıcaklık kararlılığına ve uzun ömre sahip olmasına yardımcı olur. Doğru manyetik niteliklere ulaşmak bu bileşenlerin tam olarak birleştirilmesine bağlıdır. Doğru oranları garantilemek için ham bileşenler tartılır; herhangi bir bileşim dengesizliğini önlemek için titiz hesaplamalar yapılır.
Ölçümleri tam olarak doğru olduğunda, öğeler homojen bir karışım oluşturmak için harmanlanır. Bu kombinasyon, ortaya çıkan ürünün mıknatısın tüm parçaları üzerinde sabit manyetik özelliklere sahip olmasını garantilemek için çok önemlidir. SmCo mıknatısının çeşitli kullanımlarda etkili bir şekilde çalıştığından emin olmak için ilk aşamalardan biri, bu malzeme karışımının homojenliğidir.
Adım 2: Eritme ve Alaşımlama
Eritme ve alaşımlama prosedürü, malzeme hazırlama aşamasının ardından gelir. Bir indüksiyon fırını, ölçülen samaryum ve kobaltı ve diğer malzemeleri çalıştırır. Isıtma işlemi sırasında oksidasyonu durdurmak için, bu fırın argon veya başka bir inert gaz çalıştırır. Bu nedenle fırın atmosferini oksijensiz tutmak çok önemlidir çünkü oksidasyon, bileşenlerin saflığını azaltarak nihai mıknatısın kalitesini etkiler.
Bileşenler, kobalt ve samaryumun eriyip homojen bir alaşım oluşturmak üzere birleştiği yüksek sıcaklıklara kadar ısıtılır. Kalıplara dikkatlice döküldükten sonra, bu erimiş alaşım katı külçeler oluşturur. Daha fazla işlemden önce, bu külçeler mıknatısın ham halidir. Erimiş malzemenin mükemmel bir şekilde dökülmesi, külçelerin uygun boyutunu ve bileşimini garanti eder.
Alaşımın kararlılığını korumak, fırın sıcaklığının yanı sıra döküm hızının da yakından düzenlenmesine bağlıdır. Herhangi bir sıcaklık değişimi veya yetersiz soğutma, mıknatısın manyetik niteliklerinde değişikliklere neden olabilir. Bu aşama, ısı, zaman ve dikkatli malzeme yönetimi arasında hassas bir denge eylemidir.
Adım 3: Alaşımı Frezeleme
Soğutulmuş ve sertleştirilmiş külçeler daha sonra ince tozlara öğütülen daha küçük parçalara ayrılır. Malzemeyi mıknatıs üretiminin bir sonraki aşamaları için hazır hale getirdiğinden, öğütme mıknatıs yapım sürecinde önemli bir aşamadır. Öğütme makineleri alaşım külçelerini besler ve bu külçeler tutarlı parçacık boyutunda ince tozlara ayrılır.
Mıknatıs üretimindeki sonraki aşama, parçacıkların şekillendirilmesine ve hizalanmasına izin verdiği için bu toza bağlıdır, böylece elde edilen ürünün manyetik alanı en üst düzeye çıkarılır. Manyetik parçacıkların daha sonra ezilebilecek veya katı bir yapıya sinterlenebilecek kadar küçük olmasını garantilemek için, toz kıvamı oldukça kesin kriterleri karşılamalıdır.
Bu öğütme adımında malzeme, homojen parçacık boyutunu garantilemek için sürekli gözlem altındadır. Parçacık boyutundaki değişiklikler, nihai manyetik güçte ve genel SmCo mıknatıs performansında değişikliklere neden olabilir.
Adım 4: Presleme veya Sinterleme
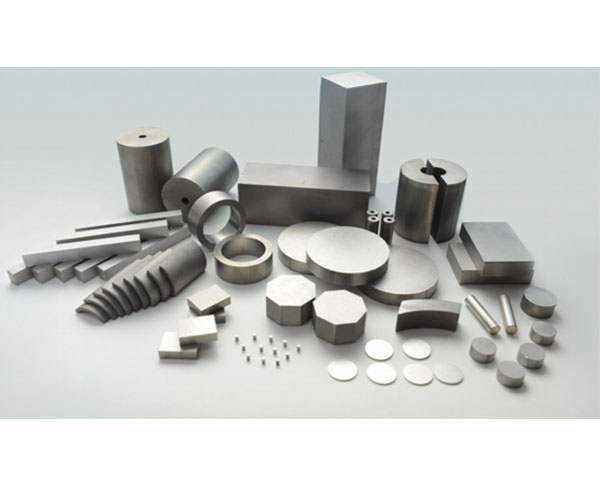
Toz haline getirilmiş alaşım daha sonra ya preslenmeli ya da sinterlenmelidir. Presleme, toz haline getirilmiş malzemenin bir kalıpta büyük basınç altında sıkıştırılmasıyla katı bir nesnenin oluşturulmasıdır. Ancak SmCo mıknatıslar için sinterleme (daha sık kullanılan teknik) daha fazla ısıl işlem içerir.
Toz bir kalıba yerleştirilir ve sinterleme sırasında erime noktasının hemen altında 1250°C'ye kadar çok yüksek bir sıcaklığa ısıtılır. Bu ısıyla meydana gelen parçacıkların füzyonu katı bir kütle üretir. Daha sonra malzeme, parçacıkların mıknatısın manyetik gücünü en üst düzeye çıkaracak şekilde hizalanmasını garantilemek için manyetik bir alan altında soğutulur. Son mıknatısın maksimum enerji ürününe ve tam koersiviteye (manyetiksizleşmeye karşı direnç) sahip olmasını sağlamak bu aşamaya bağlıdır ve kesinlikle hayati önem taşır.
Isı ile çalışan bir işlem olan sinterleme, çok hassas sıcaklık kontrolü gerektirir. Çok düşük bir sıcaklık zayıf parçacık füzyonuna neden olur; çok yüksek bir sıcaklık ise alaşımın erimesine ve manyetik niteliklerini kaybetmesine neden olabilir. Dahası, manyetik alan altında doğru soğutma, mıknatısın amaçlanan gücünü ve hizalamasını korumasını garanti eder.
Adım 5: İşleme ve Sonlandırma
Sinterleme, daha fazla işlem gerektiren, nispeten hassas sonuç mıknatısları bırakır. İşleme ve cilalama adımları, mıknatısın mükemmel şekline kalıplanmasını sağlar. Genellikle katı boyut sınırlarına uyacak şekilde cilalanan sinterlenmiş mıknatıslar öğütülmüştür. Bu aşama kesinlikle önemlidir çünkü mıknatısın nihai boyutu ve biçimi, uygulamasını doğrudan etkiler.
Bu işlem ayrıca, mıknatısın amaçlanan kullanımına uyumunu veya performansını etkileyebilecek herhangi bir kusuru gidermek için yüzey parlatma ve pürüzsüzleştirmeyi de içerir. Bu adımda hassasiyet çok önemlidir çünkü herhangi bir küçük hata, ileride önemli performans sorunlarına yol açabilir.
Adım 6: Kaplama ve Mıknatıslama
Kaplama ve mıknatıslamanın son işlemleri, mıknatıslar gerekli form ve boyuta işlendikten sonra gerçekleşir. Ömürlerini uzatmak ve korozyonu durdurmak için mıknatıslara koruyucu bir kaplama uygulanır. Mıknatısın planlanan uygulamasına bağlı olarak, yaygın kaplamalar nikel (Ni), çinko (Zn) veya diğer koruyucu bileşiklerdir.
Mıknatıslar kaplamanın ardından son bir mıknatıslanma sürecinden geçer. Mıknatıslanma sırasında, malzeme içindeki manyetik alanları hizalamak için harici bir manyetik alan kullanılır, böylece manyetik nitelikleri etkinleştirilir. Bu aşama, mıknatısın beklenen kullanımında çalışabilmesini ve tam manyetik potansiyeline ulaşmasını garanti eder.
Önemli bir aşama mıknatıslanmadır çünkü mıknatısın performans niteliklerini sonlandırır ve manyetik alanını aktive eder. Mıknatısın tüm gücü, kararlılığı ve manyetikliğini kaybetmeye karşı direnci, bu işlem boyunca uygulanan manyetik alanın türüne ve gücüne bağlıdır.
SmCo Mıknatısın Yüzey İşlemi Nasıl Seçilir?
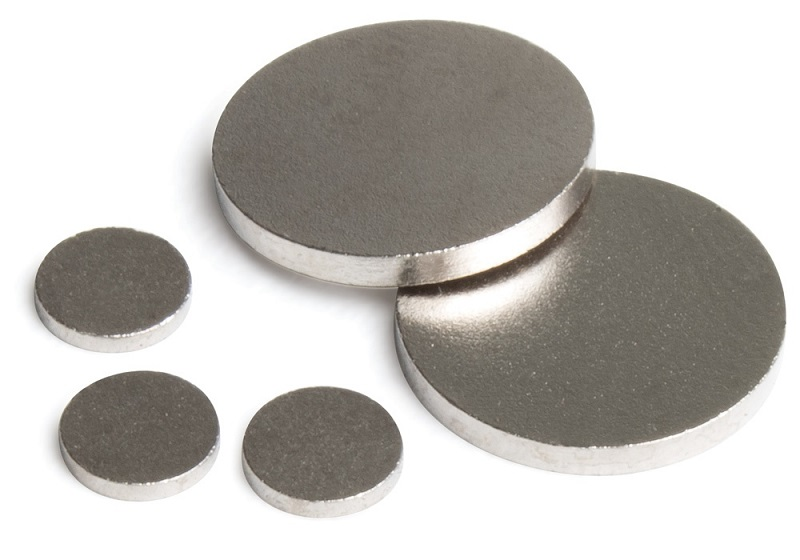
SmCo mıknatısların ömrü yüzey işlemiyle önemli ölçüde artırılır. Uygulamaya bağlı olarak mıknatısları oksidasyondan, aşınmadan ve korozyondan korumak için farklı kaplamalar kullanılır. SmCo mıknatıslar için en sık kullanılan iki yüzey işlemi nikel (Ni) ve çinko (Zn) kaplamalardır. Özellikle deniz veya yüksek sıcaklık koşulları gibi zorlu ortamlarda, bu kaplamalar mıknatısın ömrünü ve performansını uzatır. Yüzey işlemi, mıknatısın kullanılacağı ortam ve gereken koruma derecesi dikkate alınarak seçilmelidir.
SmCo Mıknatısların Avantajları ve Dezavantajları

İşte SmCo mıknatısların avantajları ve dezavantajları
Avantajları
SmCo mıknatıslarının üstün özellikleri -yüksek enerji yoğunluğu, yüksek sıcaklık kararlılığı ve korozyona karşı direnç- iyi bilinmektedir. Havacılık ve otomotiv sektörleri gibi yüksek sıcaklık durumlarında kullanım için mükemmeldirler çünkü 350°C'ye kadar sıcaklıklarda çalışabilirler. SmCo mıknatısları ayrıca yüksek bir koersiviteye sahiptir, yani manyetikliği gidermeye karşı dirençlidirler.
Dezavantajları
SmCo mıknatısların birçok avantajı olmasına rağmen, NdFeB gibi diğer mıknatıs türlerinden daha kırılgandırlar. Kırılganlığı, darbeye veya stresle ilişkili bozulmaya karşı duyarlılığını artırır. Dahası, üretimlerinin hammadde maliyeti, daha maliyetli olma eğilimlerini etkiler. Zorlu koşullarda mükemmel olmalarına rağmen, bazı kullanıcılar daha yüksek fiyat noktalarını engelleyici bulabilir.
SmCo Mıknatısların Uygulama Alanları
SmCo mıknatısları geniş bir sektör ve kullanım yelpazesinde kullanılmaktadır. Uzay, askeri ve elektronik gibi sektörlerdeki temel bileşenler, harika manyetik nitelikleri ve yüksek sıcaklık kararlılığıdır. SmCo mıknatısları, uçaklarda yüksek sıcaklıklarda uzun ömürlü olması gereken tahrik sistemlerinde ve sensörlerde kullanılır. Ayrıca elektrikli otomobiller ve MRI makineleri gibi tıbbi ekipmanlar için elektrik motorlarında hayati öneme sahiptirler. Ayrıca birçok sektörde uyarlanabilirliklerini gösterenler arasında manyetik levitasyon sistemleri, rüzgar türbinleri ve SmCo mıknatısları kullanan otomotiv sensörleri yer almaktadır.
Çözüm
Güçlü manyetik özellikler, sıcaklık kararlılığı ve korozyon direnci SmCo mıknatıslarını oldukça değerli olarak tanımlar. Bu mıknatıslar, malzeme hazırlama, sinterleme, işleme ve kaplama gibi kesin yöntemler kullanılarak yapılmıştır. Kırılganlık ve maliyet gibi bazı dezavantajları olmasına rağmen, özel faydaları onları önemli kullanımlarda kesinlikle hayati hale getirir. İstihdam sektörünüz havacılık, elektronik veya başka bir şey olsun, SmCo mıknatıslarının nasıl üretildiğini bilmek, çağdaş teknolojideki rollerini değerlendirmenizi sağlar. SmCo mıknatısları, uyarlanabilirlikleri ve sofistike üretim tekniklerinin bir araya gelmesiyle birçok sektörde her zaman yaratıcılığa ilham verecekleri garanti edildiğinden, yüksek teknoloji sistemlerinde gerekli bir parçadır.