Table of Contents
NdFeB (Neodymium Iron Boron) and SmCo (samarium cobalt) permanent magnets have numerous applications in the electronics ( speakers, headphones) , Renewable (wind turbines), medical and automobile industries ( motors, Brakes, clutches ). These magnets are valuable for different applications because of exceptional properties but some environmental factors affect their performance. To protect these magnets from the effect of environmental elements like corrosion, temperature and humidity, the surfaces of these magnets need to be coated with protective layers. When magnets are exposed to the high humidity and temperature condition environment then surface of these is damaged and performance and effectiveness is affected. The cost of the project or product is increased due to repair and replacement of magnets. The magnets can perform better and for a longer time and the product is economical if high-quality surface coating is done.
The different techniques and methods of surface protection for permanent magnets with advantages and disadvantages are explored and described in this article. The criteria for selection of the suitable protection materials for the permanent magnets are also described for the guidance and information of the manufacturing industries and the clients.
The Necessity of Surface Protection of Permanent Magnets
The material characteristics of the permanent magnets make them very vulnerable for the corrosion and other environment effects. the most vulnerable permanent magnets are Neodymium iron Boron (NdFeB) magnets having oxidizing nature and these are very likely to corrosion or surface issue exposing to the humidity and corrosion environment. The corrosive nature of these magnets is risky and not suitable for the high performance and durable applications.
The different techniques and methods of surface protection for permanent magnets with advantages and disadvantages are explored and described in this article. The criteria for selection of the suitable protection materials for the permanent magnets are also described for the guidance and information of the manufacturing industries and the clients.
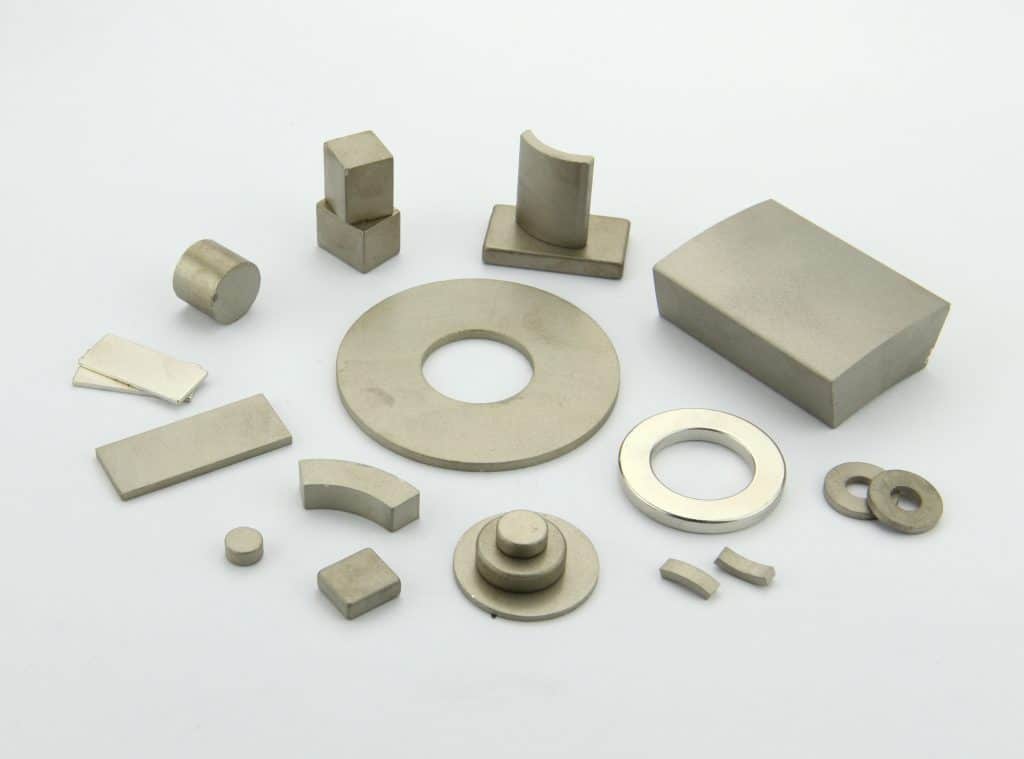
Sensitivity and susceptibility of the magnets to corrosive environment:
The magnetic properties of the permanent magnets like performance and strength are decreased gradually with the corrosion. The process of surface degradation and corrosion of the magnets is speed up with continuous exposure to chemicals and variation of temperature and humidity. The performance and effectiveness of the magnetic circuits are affected and compromised and also the whole system can be failed even with the small amount of corrosion effect.
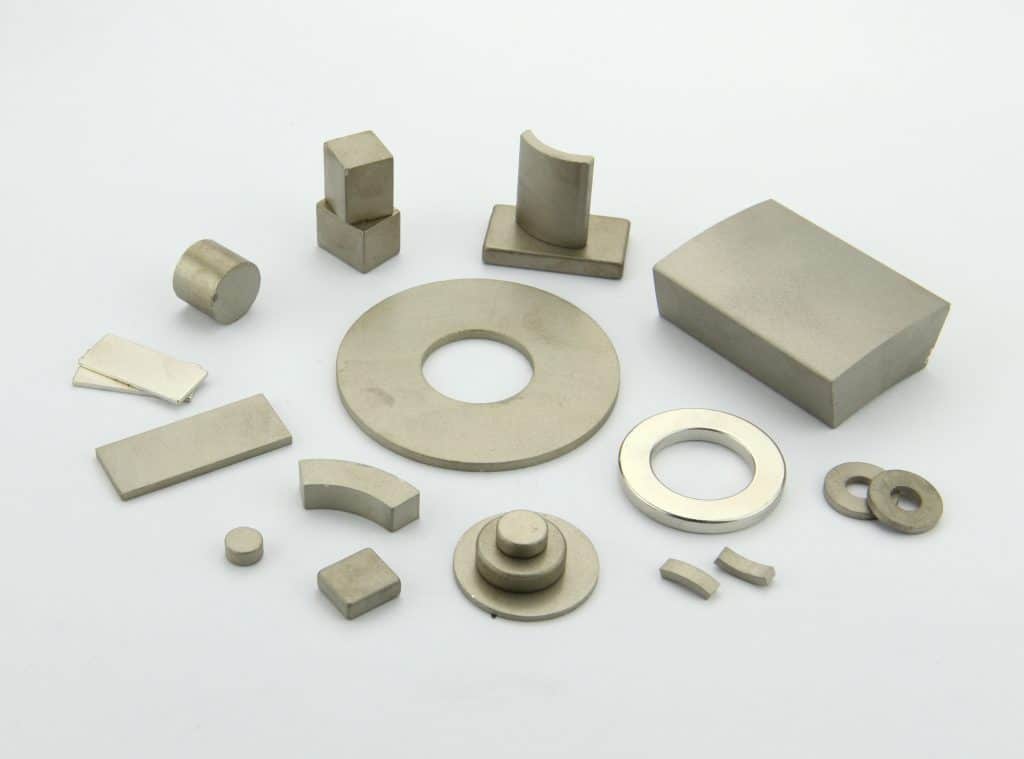
Improving the durability and service life of magnets:
The durability and service life of the magnets can be improved by devising and implementing effective surface protection strategies or techniques. The protective layer is produced on the surface of the magnets with coating techniques and protects from humidity, corrosion, and oxidation effects, and the life of the magnets is also increased. The overall operational performance of the magnets can be increased and less maintenance costs are required if investment is made in surface protection techniques. The chances of failure of the equipment can also be mitigated with the use of high-quality and effective surface protection techniques.
List of applications with requirement of high corrosion resistance:
Some of the applications where high corrosion resistance of the permanent magnets is required listed below:
Medical Instruments:
Medical instruments like Magnetic resonance imaging (MRI) and diagnostic devices work with the magnetic field of the permanent magnets. The permanent magnets provide the continuous magnetic field environment in these devices for durable and reliable operation.
Automobiles:
The permanent magnets are the main components of the sensors and motors of automobiles and are more exposed to environmental effects. So, the surface of the permanent magnets used in automobiles need to be coated with protective layer.
Motors (Electric):
The electric motors of ships and industrial units exposed to harsh and humid environments are more vulnerable for the corrosion and other surface degradation processes.
The industries may ensure the protection of surface of the magnets for better performance in the humid and corrosive environments by considering the above discussed importance of the coating of the surface of the permanent magnets.
Common Surface Protection Methods for Permanent Magnets
There are different surface methods in the market for the protection of the permanent magnets from corrosion and other surface degradation effects. Some of the surface protection methods are described below:
Organic coating:
The strong surface protection of the permanent magnets from the effects of the chemicals and moisture, the coating of the polyurethane and epoxy resin on the surface of the magnets is done. This coating is called organic coating .The impact resistance and adhesion property of the magnets is increased with the formation of a protective layer on the surface of the magnets. The magnets are colored and smoothly finished with this type of coating so the coated magnets are very feasible or suitable for aesthetic applications.
Oxidation Treatment:
For Neodymium Iron Boron (NdFeB) and SmCo ( Samarium Cobalt) magnets, oxidation treatment method is very suitable. In this technique, a controlled layer of oxide is formed on the magnets surface. With this technique, the durability and corrosion resistance of the Permanent magnets is increased for the conditions of humid and harsh environment.
Plating method:
Plating techniques like zinc and Nickel-Copper-Nickel methods are used for the surface protection of permanent magnets.
Zinc type plating:
Protection of the surface of the permanent magnets for short time period, zinc plating method is very suitable and economical method. The sacrificial layer of the zinc is produced on the surface of the magnets which corrodes as a result of corrosive environment and protect the magnet. Zinc plating method is not used generally because of the short term protection from the corrosive environment.
Nickel Copper Nickel type plating:
For surface protection of the permanent magnets, Nickel Copper Nickel is most commonly used method. This is triple layer plating method offers high resistance capacity against corrosion by improving the adhesion and toughness of the permanent magnets. The external nickel coating provides the extra protection and making this technique very feasible for different applications of the industry.
Vacuum coating:
Vacuum coating is known as the physical vapor deposition method and very suitable for harsh environmental conditions due to high corrosion resistance and strong bonding properties.
Chemical plating:
Nickel-phosphorous alloy plating:
In this technique, Nickel phosphorous alloy plating is done on the surface of the permanent magnets for enhancing corrosion resistance for the humid and corrosive conditions. This type of plating is done in different thicknesses to increase the wear resistance according to the requirements of the environment.
Parylene coating method:
For achieving excellent corrosion resistance and extra thinness of the permanent magnets, parylene coating method is widely used because of its highly specialized properties. The complex shapes magnets are coated with this technique easily and perfectly without affecting the magnetic performance. This technique has applications in the electronics and medical equipment.
Water proof encapsulation:
The water proof encapsulation is a complete protection method in which plastic or epoxy material coating is applied on the surface of the permanent magnets to prevent magnets from the high humidity conditions. The long-term durability and performance of the magnets are ensured with this coating technique and provide a feasible solution for the server environmental conditions. It also makes the surface of the magnets contamination and moisture-proof.
Comparison of the advantages and disadvantages of various surface protection methods
The necessary requriements should be considered while selecting the suitable protection method. The factors of these coating methods are discussed in the following table.
| Corrosion Resistance |
| Production Complexity | Performance Characteristics | Applicable Scenario | ||
Zinc Coating | Medium | Low | Low | Medium corrosion resistant, less costly, for non -corrosive condition | Protection for shorter time period | ||
Organic Coating | High | Medium | Medium | feasible for complex shaped, provides protection from corrosion due to chemicals | For chemical and high humidity conditions | ||
Nickel Copper-Nickel plating | High | Medium | Medium | Offers excellent resistance for corrosion, widely used | Suitable for humid condition | ||
Chemical plating (Nickel-phosphorous alloy) | Very high | Medium | high | Suitable for severe conditions due to high corrosion resistance | For marine applications (highly corrosive) | ||
Vacuum spraying /platting | Very high | high | high | Very High cost Resistance for high temperature and surface protection | For precision instruments | ||
Oxidation technique | Low | Low | Low | Stability of surface enhanced, performance of protection is weaker | Suitable for SmCo magnets | ||
Water encapsulation | Very high | Medium to high | Medium to high | Most suitable for underwater and outdoor envrionment | Stable for logn term exposure to mositure | ||
Parylene coating technique | Very high | High | high | Most suitable for sensitive applications and high corrosion resistance | For electronics and medical |
How to choose the right surface protection solution
The selection of the suitable surface protection method for the permanent magnets is very critical because the performance and longevity is ensured. The important elements which need to be considered are enlisted below:
High resistance for humidity: That coating technique should be used which have high resistance for corrosion and humidity.
Stability for high temperature: the coating which remain stable for high temperature conditions.
Suitable for salty or marine applications: The method of surface protection is suitable which can bear the conditions of saltine water.
Durability vs Cost:
The durability should be preferred over the cost of the coating technique because some of the coating methods are costly but have higher durability and life due to use of high-quality materials and application technique.
Guide for selection:
- Identification of the working environment like industrial, indoor, and outdoor.
- Type of corrosive elements like salty, chemicals, water.
- Performance requirement
- Selection of technique according to requirement and budget.
What We Can Do For The Surface Protection of Permanent Magnets?
We are highly expertise in providing the high-quality surface protection for the permanent magnets.
Our team is highly experience in providing the services of surface protection for permanent magnets with deep knowledge and skills for selection of suitable technique with respect to the design conditions.
Coating | Technical Procedure Name | Color | Thickness (μm) | Duration(h) | Temperature (℃) | Environment | ||
SST | Damp Heat Test | PCT | ||||||
White Zn | Electrical Coating | Blue | 4-10 | 24 | 48 | — | <160 | Normal Temperature |
Colored Zn | Electrical Coating | Colored | 4-10 | 48 | 48 | — | <160 | Normal Temperature |
Chemical Ni | Chemistry Coating | Silver | 8-15 | 96 | 300 | 48 | <200 | Corrosive Environment |
Ni-Ni | Electrical Coating | Silver+ White | 10-20 | 72 | 300 | 48 | <200 |
Corrosive Environment |
Ni-Cu-Ni | Electrical Coating | Silver+ White | 12-25 | 72 | 500 | 48 | <200 | |
Ni-Cu-Ni+Sn | Electrical Coating | Silver+ White | 12-25 | 72 | 500 | 96 | <200 | Corrosive Environment |
Sprayed Epoxy | Electrophoresis | Black or Grey | 15-30 | 96 | 120 | — | <180 |
Strong Corrosive Environment |
Ni-Cu+ Epoxy | Electrical Coating +Electrophoresis | Black or Grey | 25-45 | 500 | 1000 | — | <200 | |
Everlube | Electrical Coating | Yellow | 10-20 | 72 | 500 | 72 | -70~180 | |
Phosphate/Passivated | Chemical Deposition | Dark Gray | 1-2 | — | — | — | <500 | Temporary Protection |
Vacuum Aluminium | Vacuum Coating | Silver+ White | 2-10 | 100 | 500 | 72 | <500 | Fluctuating Temperature Environment |
Teflon | Electrical Coating | Black | 8-15 | 24 | 120 | 48 | <260 | High Temperature resistance |
Future trends in permanent magnetic material surface protection
We are looking forward in the development and progress of surface protection techniques with the advancement of technology.
Technologies for anti corrosion:
The life and durability of the permanent magnets will be increased for severe environmental conditions with the invention of new technologies.
Innovative materials:
Anticipating for the new and innovating materials for the coating of the permanent magnets which may offer high performance and durability.
Environmental friendly:
The Research and development works are being done to mitigate the harmful impact of these coatings on the environment.
Conclusion
The Neodymium Iron Boron (NdFeB) magnets are more vulnerable for the corrosion and severe environmental conditions so protective surface coatings are very essential for these permanent magnets for sustaining the performance and increasing the durability. The suitable and effective surface coating technique can make these magnets very useful for the humid and corrosive environment but also enhance the performance and durability.
For sustaining the magnetic properties for longer time, it is very essential for choosing the most suitable surface coating technique for the permanent magnets. The environment risks and dangers can be lessened with the tailored surface protection techniques.
For professional recommendations and solution, we encourage customers to contact us at any time. We are highly experience and have diverse expertise in surface protection method will provide you the quality service.
Please do contact for guidance and solution for the surface protection techniques and how to selection the right technique for your magnets. We can increase the performance and durability of your permanent magnets with your cooperation.