Como os ímãs SmCo são feitos?
Índice
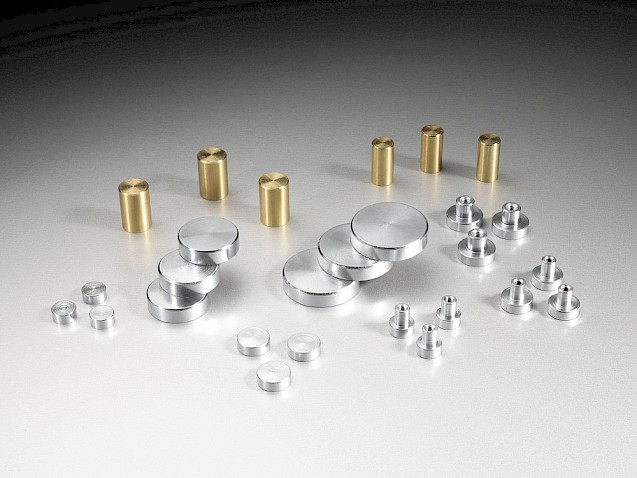
Feito de uma mistura de samário e cobalto, Ímãs SmCo são um pilar de muitos setores de alta tecnologia. Particularmente em altas temperaturas, esses ímãs são famosos por sua estabilidade e resistência. Como então os ímãs de SmCo são produzidos? O método complexo por trás da produção de ímãs extremamente fortes o guiará nesta página. Da preparação do material aos retoques finais, cada estágio é vital para garantir que os ímãs funcionem como deveriam. Este guia fornecerá todo o conhecimento de que você precisa, seja seu interesse em ímãs de SmCo para um projeto ou você esteja fascinado pelo processo de produção.
O que são ímãs SmCo?
Feitos essencialmente de samário e cobalto, os ímãs de SmCo — também conhecidos como ímãs de samário-cobalto — são ímãs de terras raras. As excelentes qualidades magnéticas desses ímãs — incluindo alta energia magnética e resistência à corrosão — são bem conhecidas. Em usos especializados, incluindo motores aeroespaciais, militares e de alto desempenho, sua capacidade de sobreviver a altas temperaturas — até 350 °C — os torna especialmente importantes. Os ímãs de SmCo são úteis em muitos campos diferentes, pois retêm seu magnetismo sob condições muito exigentes, ao contrário de outros ímãs.
Tipos comuns de ímãs SmCo
SmCo 1:5 e SmCo 2:17 são duas variedades primárias de ímãs de SmCo. Sua composição e qualidades magnéticas definem os dois principalmente de forma diferente. Composto por uma parte de samário e cinco partes de cobalto, o ímã de SmCo 1:5 fornece boa estabilidade e alta energia. Por outro lado, os ímãs de SmCo 2:17 têm um produto de energia magnética ainda maior e uma concentração maior de samário. Usos diversos exigem formas e tamanhos diversos de ambos os tipos.
Ímãs SmCo 1:5
Uma parte de samário combinada com cinco partes de cobalto produz ímãs SmCo 1:5. Esses ímãs têm uma boa mistura entre custo-benefício, estabilidade de temperatura e força magnética. Eles são especialmente úteis em usos onde resistência a altas temperaturas é necessária e onde força magnética modesta é suficiente. Tanto o setor industrial quanto o automotivo acham motores, sensores e atuadores usando ímãs SmCo 1:5 bastante comuns. Geralmente mais baratos do que seus equivalentes SmCo 2:17, eles são perfeitos para usos com menos requisitos de desempenho.
Ímãs SmCo 2:17
Cerca de duas partes de samário para cada dezessete partes de cobalto, os ímãs SmCo 2:17 têm uma concentração maior de samário. Seu produto de energia magnética é, portanto, maior do que o dos ímãs SmCo 1:5. Força magnética superior, resistência à temperatura e longevidade abundam nos ímãs SmCo 2:17. Motores de alto desempenho, sensores magnéticos e aplicações aeroespaciais onde tanto alta energia magnética quanto estabilidade em temperaturas aumentadas são necessárias encontram uso frequente para eles. Embora sejam preferidos em aplicações exigentes, os ímãs SmCo 2:17 são geralmente mais caros do que os ímãs SmCo 1:5 devido ao seu melhor desempenho.
Fluxo de processo do ímã SmCo
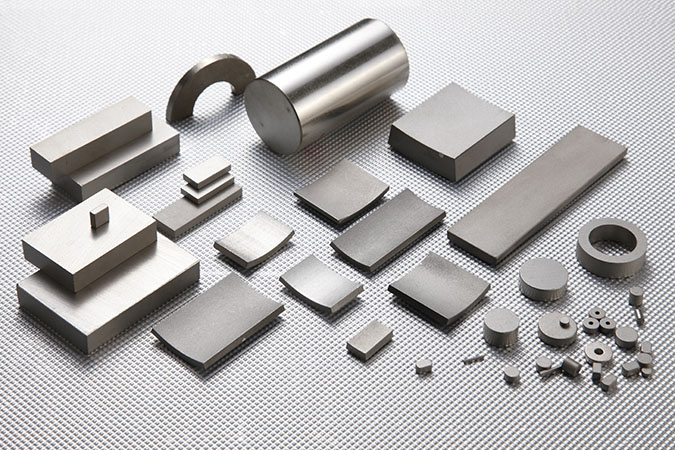
A fabricação de ímãs de SmCo é um procedimento muito exato com vários processos que ajudam a definir as qualidades finais do ímã. Como até mesmo a menor variação do processo pode influenciar o desempenho dos ímãs de SmCo, o caminho da fabricação exige precisão e conhecimento. Exploraremos cada estágio em mais detalhes nesta parte, com atenção especial a como esses ímãs são meticulosamente criados para satisfazer os padrões da indústria e critérios de aplicação específicos.
Etapa 1: Preparação do material
A escolha cuidadosa e o processamento de matérias-primas vêm primeiro na fabricação de ímãs de SmCo. Samário (Sm) e cobalto (Co) compõem principalmente os ímãs de SmCo. Excelentes qualidades magnéticas desses dois materiais levaram à sua escolha. O elemento de terra rara samário é responsável pelo alto campo magnético; o cobalto melhora a estabilidade e a resistência à corrosão do ímã.
Normalmente, os componentes brutos também compreendem concentrações mínimas de ferro (Fe), cobre (Cu) e outros metais traço, incluindo zircônio (Zr) e háfnio (Hf). Esses componentes extras ajudam os ímãs a ter melhor desempenho magnético geral, estabilidade de temperatura e longevidade. Alcançar as qualidades magnéticas corretas depende da combinação exata desses componentes. Para garantir as proporções corretas, os ingredientes brutos são pesados; cálculos meticulosos são feitos para evitar qualquer desequilíbrio de composição.
Os itens são misturados para criar uma mistura homogênea quando suas medições são precisamente precisas. Essa combinação é crucial para garantir que o produto resultante tenha características magnéticas constantes sobre todas as partes do ímã. Um dos primeiros estágios para garantir que o ímã SmCo funcione efetivamente em uma variedade de usos é a homogeneidade dessa mistura de materiais.
Etapa 2: Fusão e Ligação
O procedimento de fusão e liga vem após a fase de preparação do material. Um forno de indução opera o samário e o cobalto medidos, bem como quaisquer outros materiais. Para interromper a oxidação durante o processo de aquecimento, este forno opera argônio ou outro gás inerte. Manter a atmosfera do forno livre de oxigênio é, portanto, muito importante, pois a oxidação reduziria a pureza dos componentes, influenciando a qualidade do ímã final.
Os componentes são aquecidos a temperaturas tão altas, onde o cobalto e o samário derretem e se combinam para criar uma liga homogênea. Após o vazamento cuidadoso em moldes, essa liga fundida forma lingotes sólidos. Antes de mais tratamento, esses lingotes são a forma bruta do ímã. O vazamento perfeito do material fundido garante o tamanho e a composição apropriados dos lingotes.
Manter a estabilidade da liga depende de regular rigorosamente a temperatura do forno, bem como o ritmo de vazamento. Quaisquer variações de temperatura ou resfriamento inadequado podem produzir variações nas qualidades magnéticas do ímã. Este estágio é, então, um delicado ato de equilíbrio entre calor, tempo e gerenciamento cuidadoso do material.
Etapa 3: Fresagem da liga
Os lingotes resfriados e endurecidos quebram em pedaços menores que são posteriormente moídos em pós finos. Como ela deixa o material pronto para as próximas fases da fabricação do ímã, a moagem é um estágio crucial no processo de fabricação do ímã. Máquinas de moagem alimentam os lingotes de liga, que se quebram em um pó fino de tamanho de partícula consistente.
O estágio seguinte na produção de ímãs depende desse pó, pois ele permite que as partículas sejam moldadas e alinhadas para que o campo magnético do produto resultante seja maximizado. Para garantir que as partículas magnéticas sejam pequenas o suficiente para serem esmagadas ou sinterizadas em uma estrutura sólida posteriormente, a consistência do pó deve satisfazer critérios bastante exatos.
O material está sob observação contínua nesta etapa de moagem para garantir tamanho de partícula uniforme. Variações no tamanho de partícula podem causar variações na força magnética final e no desempenho geral do ímã SmCo.
Etapa 4: Prensagem ou Sinterização
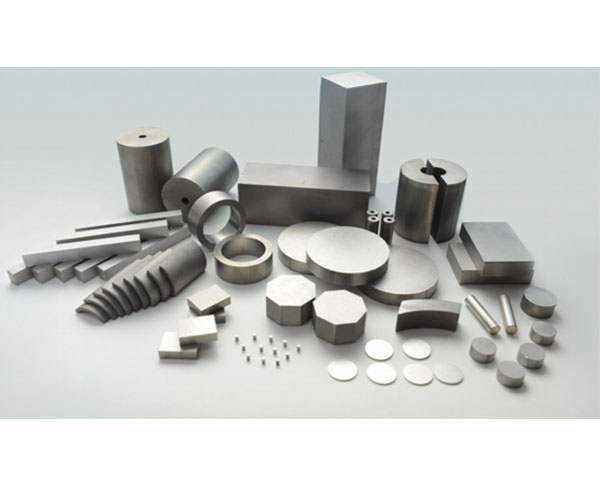
A liga em pó deve ser então prensada ou sinterizada na forma necessária. Prensagem é a formação de um objeto sólido pela compactação do material em pó sob grande pressão em um molde. Para ímãs de SmCo, no entanto, a sinterização — a técnica mais usada — envolve um tratamento térmico adicional.
O pó é inserido em uma matriz e aquecido muito alto — até 1250 °C — logo abaixo do ponto de fusão durante a sinterização. A fusão das partículas provocada por esse calor produz uma massa sólida. O material é então resfriado sob um campo magnético para garantir que as partículas se alinhem de uma maneira que maximize a força magnética do ímã. Garantir que o ímã final tenha o máximo produto de energia e coercividade total — resistência à desmagnetização — dependente desse estágio é absolutamente vital.
Um processo movido a calor, a sinterização exige um controle de temperatura muito exato. Uma temperatura muito baixa causará uma fusão de partículas ruim; uma temperatura muito alta pode fazer com que a liga derreta e perca suas qualidades magnéticas. Além disso, o resfriamento correto sob um campo magnético garante que o ímã mantenha sua força e alinhamento pretendidos.
Etapa 5: Usinagem e Acabamento
A sinterização deixa ímãs resultantes um tanto delicados que exigem mais processamento. As etapas de usinagem e polimento permitem que o ímã seja moldado em seu formato perfeito. Normalmente polidos para corresponder a limites dimensionais rigorosos, os ímãs sinterizados foram retificados. Este estágio é absolutamente importante, pois o tamanho e a forma finais do ímã afetam diretamente sua aplicação.
Este processo também compreende polimento e alisamento da superfície para remover quaisquer defeitos que possam impactar o desempenho ou o ajuste do ímã em seu uso pretendido. A precisão é crucial durante esta etapa, pois qualquer pequeno erro pode levar a problemas significativos de desempenho no futuro.
Etapa 6: Revestimento e magnetização
Os últimos processos de revestimento e magnetização seguem depois que os ímãs foram usinados na forma e tamanho necessários. Para aumentar sua vida útil e impedir a corrosão, os ímãs têm uma cobertura protetora aplicada sobre eles. Dependendo da aplicação planejada do ímã, os revestimentos comuns são níquel (Ni), zinco (Zn) ou outros compostos protetores.
Os ímãs passam por um último processo de magnetização após o revestimento. Um campo magnético externo é usado durante a magnetização para alinhar os domínios magnéticos dentro do material, ativando, portanto, suas qualidades magnéticas. Este estágio garante que o ímã possa funcionar em seu uso esperado e atinja seu potencial magnético total.
Uma etapa importante é a magnetização, pois finaliza as qualidades de desempenho do ímã e ativa seu campo magnético. Toda a força, estabilidade e resistência à desmagnetização do ímã dependem do tipo e da força do campo magnético aplicado durante toda essa operação.
Como escolher o tratamento de superfície do ímã de SmCo?
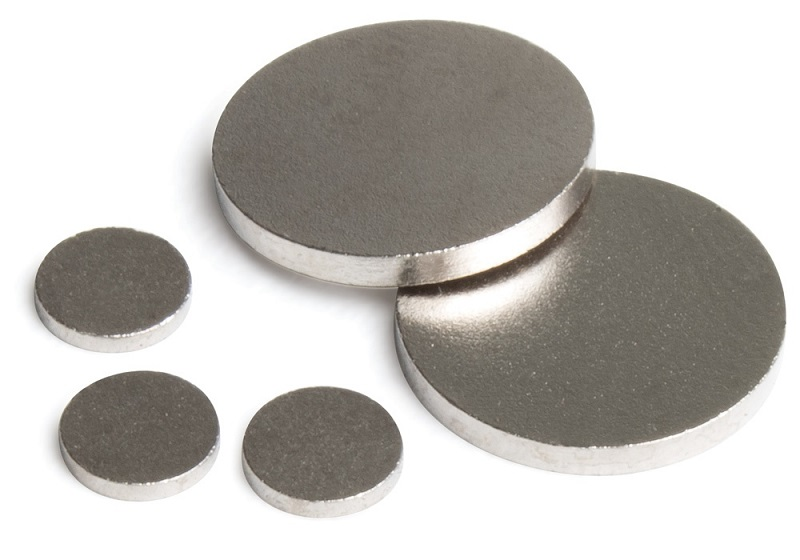
A vida útil dos ímãs de SmCo é substancialmente melhorada pelo tratamento de superfície. Diferentes revestimentos são usados para proteger os ímãs de oxidação, desgaste e corrosão com base na aplicação. Os dois tratamentos de superfície mais usados para ímãs de SmCo são revestimentos de níquel (Ni) e zinco (Zn). Particularmente em ambientes exigentes como condições marítimas ou de alta temperatura, esses revestimentos estendem a vida útil e o desempenho do ímã. O tratamento de superfície deve ser selecionado considerando o ambiente em que o ímã será utilizado e o grau de proteção necessário.
As vantagens e desvantagens dos ímãs SmCo

Aqui estão os benefícios e desvantagens dos ímãs SmCo
Vantagens
As características superiores dos ímãs de SmCo — alta densidade de energia, ótima estabilidade de temperatura e resistência à corrosão — são bem reconhecidas. Para usos em situações de alta temperatura, como nos setores aeroespacial e automotivo, eles são perfeitos, pois podem operar em temperaturas de até 350 °C. Os ímãs de SmCo também têm alta coercividade, o que significa que são resistentes à desmagnetização.
Desvantagens
Embora os ímãs de SmCo tenham vários benefícios, eles são mais frágeis do que outros tipos de ímãs, como NdFeB. Sua fragilidade aumenta sua suscetibilidade a impactos ou quebras relacionadas a tensões. Além disso, o custo de produção das matérias-primas influencia sua tendência a ser mais custosa. Embora eles se destaquem em condições exigentes, alguns usos podem achar seu ponto de preço mais alto proibitivo.
Campos de aplicação dos ímãs SmCo
Uma ampla gama de setores e usos encontram ímãs de SmCo aplicados. Componentes-chave em setores incluindo aeroespacial, militar e eletrônico são suas grandes qualidades magnéticas e estabilidade de alta temperatura. Os ímãs de SmCo encontram uso em sistemas de propulsão e sensores que precisam de longevidade em altas temperaturas em aeronaves. Além disso, vitais em motores elétricos para carros elétricos e equipamentos médicos como máquinas de ressonância magnética, eles são. Além disso, demonstrando sua adaptabilidade em muitos setores estão os sistemas de levitação magnética, turbinas eólicas e sensores automotivos usando ímãs de SmCo.
Conclusão
Fortes qualidades magnéticas, estabilidade de temperatura e resistência à corrosão definem os ímãs de SmCo como bastante valiosos. Esses ímãs foram feitos usando métodos exatos, incluindo preparação de material, sinterização, usinagem e revestimento. Embora tenham certas desvantagens — fragilidade e custo, entre outras coisas — seus benefícios especiais os tornam absolutamente vitais em usos importantes. Não importa se seu setor de emprego é aeroespacial, eletrônico ou outro, saber como os ímãs de SmCo são produzidos permite que você valorize sua parte na tecnologia contemporânea. Os ímãs de SmCo são uma parte necessária em sistemas de alta tecnologia, pois sua adaptabilidade combinada com técnicas de fabricação sofisticadas garante que eles sempre inspirarão a criatividade em muitos setores.