Índice
Os ímãs permanentes NdFeB (Neodímio Ferro Boro) e SmCo (samário cobalto) têm inúmeras aplicações nas indústrias eletrônica (alto-falantes, fones de ouvido), renováveis (turbinas eólicas), médica e automobilística (motores, freios, embreagens). Esses ímãs são valiosos para diferentes aplicações devido às propriedades excepcionais, mas alguns fatores ambientais afetam seu desempenho. Para proteger esses ímãs do efeito de elementos ambientais como corrosão, temperatura e umidade, as superfícies desses ímãs precisam ser revestidas com camadas protetoras. Quando os ímãs são expostos ao ambiente de alta umidade e temperatura, a superfície deles é danificada e o desempenho e a eficácia são afetados. O custo do projeto ou produto é aumentado devido ao reparo e substituição dos ímãs. Os ímãs podem ter um desempenho melhor e por mais tempo e o produto é econômico se for feito um revestimento de superfície de alta qualidade.
As diferentes técnicas e métodos de proteção de superfície para ímãs permanentes com vantagens e desvantagens são explorados e descritos neste artigo. Os critérios para seleção dos materiais de proteção adequados para os ímãs permanentes também são descritos para orientação e informação das indústrias de fabricação e dos clientes.
A Necessidade de Proteção de Superfície de Ímãs Permanentes
As características materiais dos ímãs permanentes os tornam muito vulneráveis à corrosão e outros efeitos ambientais. Os ímãs permanentes mais vulneráveis são os ímãs de Neodímio ferro Boro (NdFeB) com natureza oxidante e são muito propensos à corrosão ou problemas de superfície expostos à umidade e ao ambiente de corrosão. A natureza corrosiva desses ímãs é arriscada e não é adequada para aplicações duráveis e de alto desempenho.
As diferentes técnicas e métodos de proteção de superfície para ímãs permanentes com vantagens e desvantagens são explorados e descritos neste artigo. Os critérios para seleção dos materiais de proteção adequados para os ímãs permanentes também são descritos para orientação e informação das indústrias de fabricação e dos clientes.
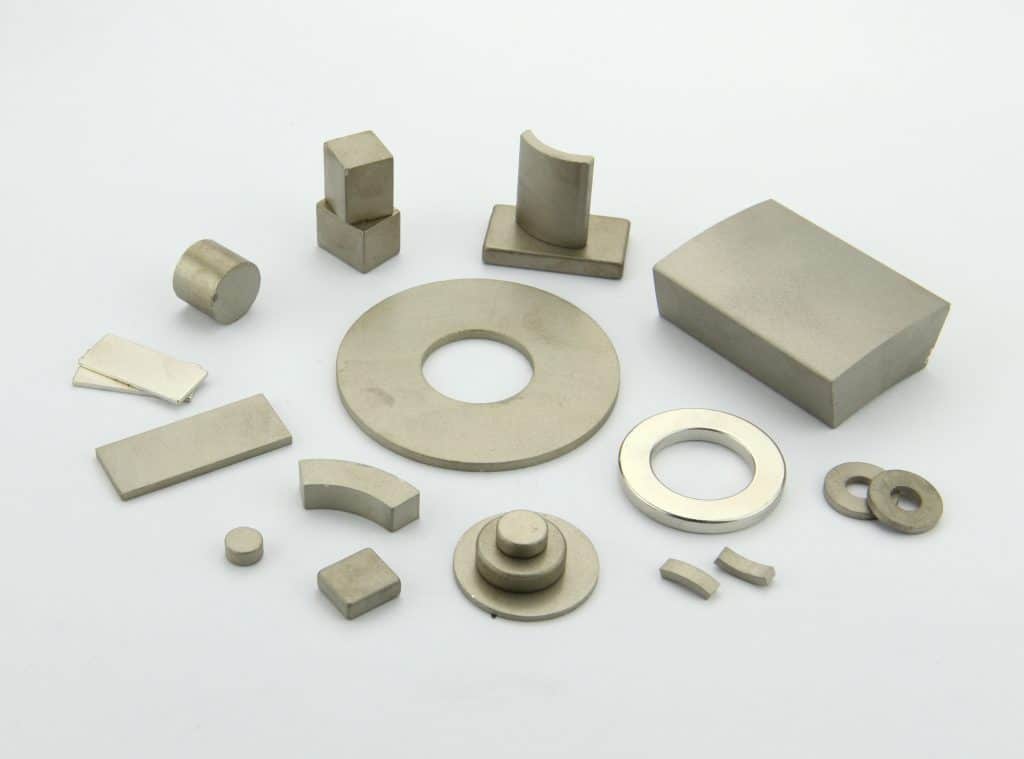
Sensibilidade e suscetibilidade dos ímãs ao ambiente corrosivo:
As propriedades magnéticas dos ímãs permanentes, como desempenho e força, diminuem gradualmente com a corrosão. O processo de degradação da superfície e corrosão dos ímãs é acelerado com exposição contínua a produtos químicos e variação de temperatura e umidade. O desempenho e a eficácia dos circuitos magnéticos são afetados e comprometidos e também todo o sistema pode falhar mesmo com a pequena quantidade de efeito de corrosão.
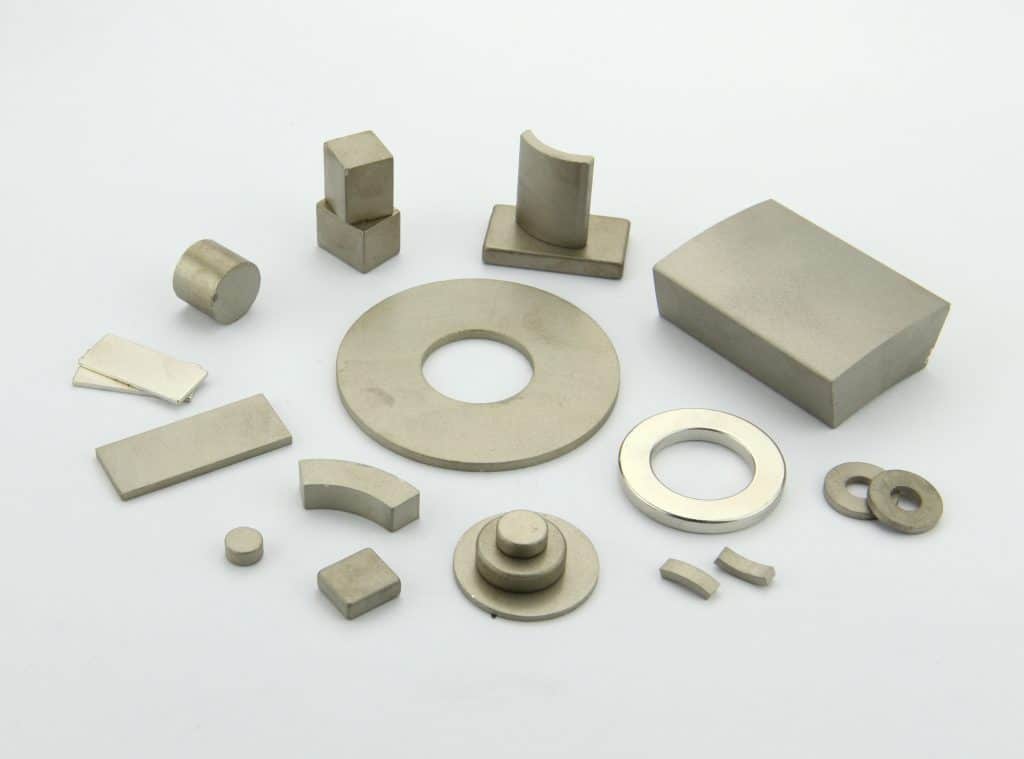
Melhorando a durabilidade e a vida útil dos ímãs:
A durabilidade e a vida útil dos ímãs podem ser melhoradas ao elaborar e implementar estratégias ou técnicas eficazes de proteção de superfície. A camada protetora é produzida na superfície dos ímãs com técnicas de revestimento e protege contra umidade, corrosão e efeitos de oxidação, e a vida útil dos ímãs também é aumentada. O desempenho operacional geral dos ímãs pode ser aumentado e menos custos de manutenção são necessários se o investimento for feito em técnicas de proteção de superfície. As chances de falha do equipamento também podem ser mitigadas com o uso de técnicas de proteção de superfície eficazes e de alta qualidade.
Lista de aplicações com exigência de alta resistência à corrosão:
Algumas das aplicações onde é necessária alta resistência à corrosão dos ímãs permanentes estão listadas abaixo:
Instrumentos médicos:
Instrumentos médicos como ressonância magnética (MRI) e dispositivos de diagnóstico funcionam com o campo magnético dos ímãs permanentes. Os ímãs permanentes fornecem o ambiente de campo magnético contínuo nesses dispositivos para uma operação durável e confiável.
Automóveis:
Os ímãs permanentes são os principais componentes dos sensores e motores de automóveis e estão mais expostos aos efeitos ambientais. Então, a superfície dos ímãs permanentes usados em automóveis precisa ser revestida com uma camada protetora.
Motores (Elétricos):
Os motores elétricos de navios e unidades industriais expostos a ambientes hostis e úmidos são mais vulneráveis à corrosão e outros processos de degradação da superfície.
As indústrias podem garantir a proteção da superfície dos ímãs para melhor desempenho em ambientes úmidos e corrosivos, considerando a importância discutida acima do revestimento da superfície dos ímãs permanentes.
Métodos comuns de proteção de superfície para ímãs permanentes
Existem diferentes métodos de superfície no mercado para a proteção de ímãs permanentes contra corrosão e outros efeitos de degradação de superfície. Alguns dos métodos de proteção de superfície são descritos abaixo:
Revestimento orgânico:
A forte proteção da superfície dos ímãs permanentes contra os efeitos dos produtos químicos e da umidade, o revestimento de poliuretano e resina epóxi na superfície dos ímãs é feito. Este revestimento é chamado de revestimento orgânico. A resistência ao impacto e a propriedade de adesão dos ímãs são aumentadas com a formação de uma camada protetora na superfície dos ímãs. Os ímãs são coloridos e suavemente acabados com este tipo de revestimento, de modo que os ímãs revestidos são muito viáveis ou adequados para aplicações estéticas.
Tratamento de oxidação:
Para ímãs de Neodímio Ferro Boro (NdFeB) e SmCo (Samário Cobalto), o método de tratamento de oxidação é muito adequado. Nessa técnica, uma camada controlada de óxido é formada na superfície dos ímãs. Com essa técnica, a durabilidade e a resistência à corrosão dos ímãs permanentes são aumentadas para as condições de ambiente úmido e severo.
Método de revestimento:
Técnicas de galvanoplastia, como métodos de zinco e níquel-cobre-níquel, são usadas para proteção de superfície de ímãs permanentes.
Zincagem tipo galvanoplastia:
Proteção da superfície dos ímãs permanentes por um curto período de tempo, o método de galvanoplastia é um método muito adequado e econômico. A camada sacrificial do zinco é produzida na superfície dos ímãs que corrói como resultado do ambiente corrosivo e protege o ímã. O método de galvanoplastia não é usado geralmente por causa da proteção de curto prazo do ambiente corrosivo.
Níquel Cobre Revestimento tipo níquel:
Para proteção de superfície de ímãs permanentes, o níquel cobre níquel é o método mais comumente usado. Este método de revestimento de camada tripla oferece alta capacidade de resistência contra corrosão, melhorando a adesão e a tenacidade dos ímãs permanentes. O revestimento externo de níquel fornece proteção extra e torna esta técnica muito viável para diferentes aplicações da indústria.
Revestimento a vácuo:
O revestimento a vácuo é conhecido como método de deposição física de vapor e muito adequado para condições ambientais adversas devido à alta resistência à corrosão e fortes propriedades de ligação.
Revestimento químico:
Revestimento de liga de níquel-fósforo:
Nessa técnica, o revestimento de liga de níquel-fósforo é feito na superfície dos ímãs permanentes para aumentar a resistência à corrosão para condições úmidas e corrosivas. Esse tipo de revestimento é feito em diferentes espessuras para aumentar a resistência ao desgaste de acordo com os requisitos do ambiente.
Método de revestimento de parileno:
Para atingir excelente resistência à corrosão e espessura extra dos ímãs permanentes, o método de revestimento de parileno é amplamente usado devido às suas propriedades altamente especializadas. Os ímãs de formas complexas são revestidos com esta técnica de forma fácil e perfeita, sem afetar o desempenho magnético. Esta técnica tem aplicações em equipamentos eletrônicos e médicos.
Encapsulamento à prova d'água:
O encapsulamento à prova d'água é um método de proteção completo no qual o revestimento de plástico ou material epóxi é aplicado na superfície dos ímãs permanentes para evitar que os ímãs fiquem expostos a condições de alta umidade. A durabilidade e o desempenho de longo prazo dos ímãs são garantidos com esta técnica de revestimento e fornecem uma solução viável para as condições ambientais do servidor. Também torna a superfície dos ímãs à prova de contaminação e umidade.
Comparação das vantagens e desvantagens de vários métodos de proteção de superfície
Os requisitos necessários devem ser considerados ao selecionar o método de proteção adequado. Os fatores desses métodos de revestimento são discutidos na tabela a seguir.
| Resistência à corrosão |
| Complexidade da Produção | Características de desempenho | Cenário aplicável | ||
Revestimento de zinco | Médio | Baixo | Baixo | Resistência média à corrosão, menos dispendiosa, para condições não corrosivas | Proteção por um período de tempo mais curto | ||
Revestimento orgânico | Alto | Médio | Médio | viável para formas complexas, fornece proteção contra corrosão devido a produtos químicos | Para condições químicas e de alta umidade | ||
Revestimento de níquel cobre-níquel | Alto | Médio | Médio | Oferece excelente resistência à corrosão, amplamente utilizado | Adequado para condições úmidas | ||
Revestimento químico (liga de níquel-fósforo) | Muito alto | Médio | alto | Adequado para condições severas devido à alta resistência à corrosão | Para aplicações marítimas (altamente corrosivas) | ||
Pulverização a vácuo/plating | Muito alto | alto | alto | Custo muito alto Resistência para alta temperatura e proteção de superfície | Para instrumentos de precisão | ||
Técnica de oxidação | Baixo | Baixo | Baixo | Estabilidade da superfície melhorada, desempenho de proteção mais fraco | Adequado para ímãs SmCo | ||
Encapsulamento de água | Muito alto | Médio a alto | Médio a alto | Mais adequado para ambientes subaquáticos e externos | Estável para exposição prolongada à umidade | ||
Técnica de revestimento de parileno | Muito alto | Alto | alto | Mais adequado para aplicações sensíveis e alta resistência à corrosão | Para eletrônicos e médicos |
Como escolher a solução certa para proteção de superfícies
A seleção do método de proteção de superfície adequado para os ímãs permanentes é muito crítica porque o desempenho e a longevidade são garantidos. Os elementos importantes que precisam ser considerados estão listados abaixo:
Alta resistência à humidade: Deve ser utilizada a técnica de revestimento que tenha alta resistência à corrosão e à umidade.
Estabilidade para alta temperatura: o revestimento que permanece estável em condições de alta temperatura.
Adequado para aplicações salgadas ou marinhas: O método de proteção de superfície é adequado para suportar as condições de água salgada.
Durabilidade vs Custo:
A durabilidade deve ser preferida ao custo da técnica de revestimento porque alguns dos métodos de revestimento são caros, mas têm maior durabilidade e vida útil devido ao uso de materiais de alta qualidade e técnica de aplicação.
Guia para seleção:
- Identificação do ambiente de trabalho, como industrial, interno e externo.
- Tipo de elementos corrosivos como sal, produtos químicos, água.
- Requisito de desempenho
- Seleção da técnica de acordo com a necessidade e o orçamento.
O que podemos fazer para proteger a superfície de ímãs permanentes?
Temos grande experiência em fornecer proteção de superfície de alta qualidade para ímãs permanentes.
Nossa equipe tem grande experiência em fornecer serviços de proteção de superfície para ímãs permanentes, com profundo conhecimento e habilidades para seleção de técnicas adequadas em relação às condições de projeto.
Revestimento | Nome do procedimento técnico | Cor | Grossura (μm) | Duração(h) | Temperatura (℃) | Ambiente | ||
TSS | Úmido Teste de calor | PCT | ||||||
Zinco branco | Revestimento Elétrico | Azul | 4-10 | 24 | 48 | — | <160 | Temperatura normal |
Zn colorido | Revestimento Elétrico | Colorido | 4-10 | 48 | 48 | — | <160 | Temperatura normal |
Ni químico | Revestimento químico | Prata | 8-15 | 96 | 300 | 48 | <200 | Ambiente Corrosivo |
Ni-Ni | Revestimento Elétrico | Prata+ Branco | 10-20 | 72 | 300 | 48 | <200 |
Ambiente Corrosivo |
Ni-Cu-Ni | Revestimento Elétrico | Prata+ Branco | 12-25 | 72 | 500 | 48 | <200 | |
Ni-Cu-Ni+Sn | Revestimento Elétrico | Prata+ Branco | 12-25 | 72 | 500 | 96 | <200 | Ambiente Corrosivo |
Epóxi pulverizado | Eletroforese | Preto ou cinza | 15-30 | 96 | 120 | — | <180 |
Ambiente fortemente corrosivo |
Ni-Cu+ Epóxi | Revestimento Elétrico +Eletroforese | Preto ou cinza | 25-45 | 500 | 1000 | — | <200 | |
Everlube | Revestimento Elétrico | Amarelo | 10-20 | 72 | 500 | 72 | -70~180 | |
Fosfato/Passivado | Deposição química | Cinza escuro | 1-2 | — | — | — | <500 | Proteção Temporária |
Alumínio a vácuo | Revestimento a vácuo | Prata+ Branco | 2-10 | 100 | 500 | 72 | <500 | Temperatura flutuante Ambiente |
Teflon | Revestimento Elétrico | Preto | 8-15 | 24 | 120 | 48 | <260 | Resistência a altas temperaturas |
Tendências futuras na proteção de superfícies de materiais magnéticos permanentes
Estamos ansiosos pelo desenvolvimento e progresso das técnicas de proteção de superfície com o avanço da tecnologia.
Tecnologias anticorrosivas:
A vida útil e a durabilidade dos ímãs permanentes serão aumentadas para condições ambientais severas com a invenção de novas tecnologias.
Materiais inovadores:
Antecipando novos e inovadores materiais para o revestimento de ímãs permanentes que podem oferecer alto desempenho e durabilidade.
Amigável ao meio ambiente:
Trabalhos de pesquisa e desenvolvimento estão sendo feitos para mitigar o impacto nocivo desses revestimentos no meio ambiente.
Conclusão
Os ímãs de Neodímio Ferro Boro (NdFeB) são mais vulneráveis à corrosão e às condições ambientais severas, portanto, revestimentos de superfície de proteção são muito essenciais para esses ímãs permanentes para sustentar o desempenho e aumentar a durabilidade. A técnica de revestimento de superfície adequada e eficaz pode tornar esses ímãs muito úteis para o ambiente úmido e corrosivo, mas também melhorar o desempenho e a durabilidade.
Para sustentar as propriedades magnéticas por mais tempo, é muito essencial escolher a técnica de revestimento de superfície mais adequada para os ímãs permanentes. Os riscos e perigos ambientais podem ser reduzidos com as técnicas de proteção de superfície personalizadas.
Para recomendações e soluções profissionais, encorajamos os clientes a entrar em contato conosco a qualquer momento. Temos muita experiência e conhecimento diversificado em métodos de proteção de superfície que fornecerão a você um serviço de qualidade.
Entre em contato para obter orientação e solução para as técnicas de proteção de superfície e como selecionar a técnica correta para seus ímãs. Podemos aumentar o desempenho e a durabilidade de seus ímãs permanentes com sua cooperação.