Sommario
I magneti permanenti NdFeB (Neodimio Ferro Boro) e SmCo (Samario Cobalto) hanno numerose applicazioni nell'elettronica (altoparlanti, cuffie), nelle energie rinnovabili (turbine eoliche), nell'industria medica e automobilistica (motori, freni, frizioni). Questi magneti sono preziosi per diverse applicazioni grazie alle proprietà eccezionali, ma alcuni fattori ambientali influenzano le loro prestazioni. Per proteggere questi magneti dall'effetto di elementi ambientali come corrosione, temperatura e umidità, le superfici di questi magneti devono essere rivestite con strati protettivi. Quando i magneti sono esposti a condizioni ambientali di elevata umidità e temperatura, la loro superficie viene danneggiata e le prestazioni e l'efficacia vengono influenzate. Il costo del progetto o del prodotto aumenta a causa della riparazione e della sostituzione dei magneti. I magneti possono funzionare meglio e per un periodo di tempo più lungo e il prodotto è economico se viene eseguito un rivestimento superficiale di alta qualità.
In questo articolo vengono esplorate e descritte le diverse tecniche e metodi di protezione superficiale per magneti permanenti con vantaggi e svantaggi. I criteri per la selezione dei materiali di protezione adatti per i magneti permanenti vengono inoltre descritti per la guida e l'informazione delle industrie manifatturiere e dei clienti.
La necessità della protezione superficiale dei magneti permanenti
Le caratteristiche dei materiali dei magneti permanenti li rendono molto vulnerabili alla corrosione e ad altri effetti ambientali. I magneti permanenti più vulnerabili sono i magneti al neodimio ferro boro (NdFeB) di natura ossidante e sono molto inclini alla corrosione o a problemi di superficie esposti all'umidità e all'ambiente corrosivo. La natura corrosiva di questi magneti è rischiosa e non adatta per applicazioni ad alte prestazioni e durevoli.
In questo articolo vengono esplorate e descritte le diverse tecniche e metodi di protezione superficiale per magneti permanenti con vantaggi e svantaggi. I criteri per la selezione dei materiali di protezione adatti per i magneti permanenti vengono inoltre descritti per la guida e l'informazione delle industrie manifatturiere e dei clienti.
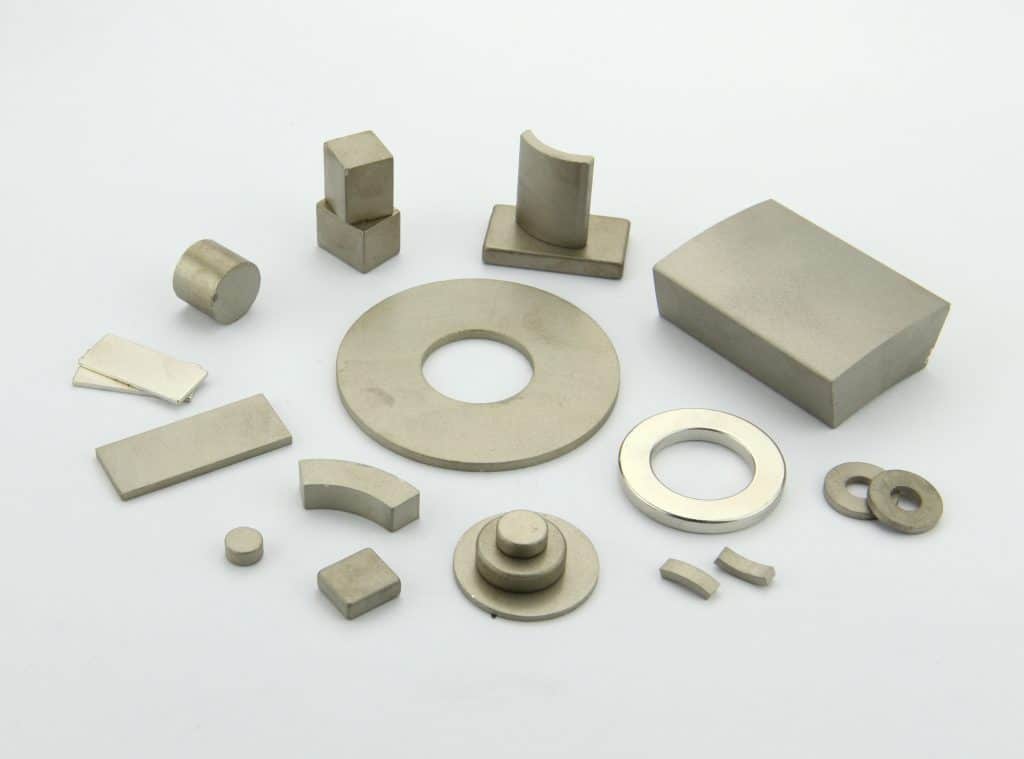
Sensibilità e suscettibilità dei magneti all'ambiente corrosivo:
Le proprietà magnetiche dei magneti permanenti come prestazioni e resistenza diminuiscono gradualmente con la corrosione. Il processo di degradazione superficiale e corrosione dei magneti viene accelerato con l'esposizione continua a sostanze chimiche e variazioni di temperatura e umidità. Le prestazioni e l'efficacia dei circuiti magnetici vengono influenzate e compromesse e anche l'intero sistema può guastarsi anche con una piccola quantità di effetto corrosivo.
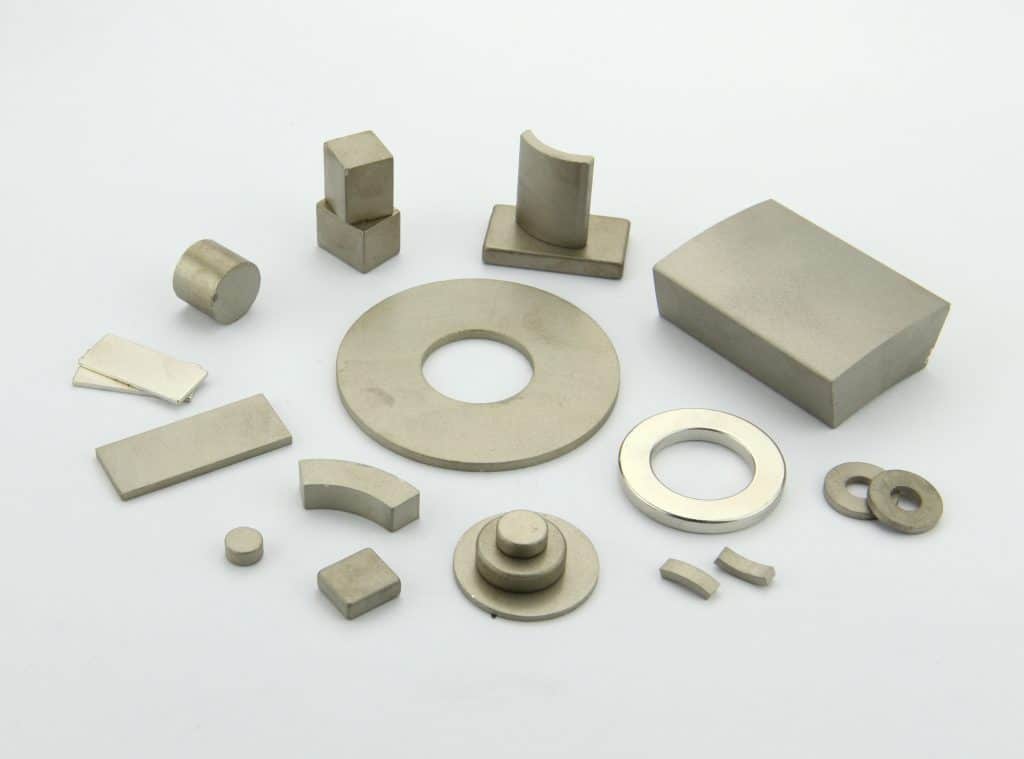
Miglioramento della durata e della vita utile dei magneti:
La durata e la vita utile dei magneti possono essere migliorate ideando e implementando strategie o tecniche efficaci di protezione della superficie. Lo strato protettivo viene prodotto sulla superficie dei magneti con tecniche di rivestimento e protegge da umidità, corrosione ed effetti di ossidazione, e la vita utile dei magneti aumenta. Le prestazioni operative complessive dei magneti possono essere aumentate e sono richiesti minori costi di manutenzione se si investe in tecniche di protezione della superficie. Le possibilità di guasto dell'attrezzatura possono anche essere mitigate con l'uso di tecniche di protezione della superficie efficaci e di alta qualità.
Elenco delle applicazioni con richiesta di elevata resistenza alla corrosione:
Di seguito sono elencate alcune delle applicazioni in cui è richiesta un'elevata resistenza alla corrosione dei magneti permanenti:
Strumenti medici:
Strumenti medici come la risonanza magnetica per immagini (MRI) e dispositivi diagnostici funzionano con il campo magnetico dei magneti permanenti. I magneti permanenti forniscono l'ambiente di campo magnetico continuo in questi dispositivi per un funzionamento durevole e affidabile.
Automobili:
I magneti permanenti sono i componenti principali dei sensori e dei motori delle automobili e sono maggiormente esposti agli effetti ambientali. Quindi, la superficie dei magneti permanenti utilizzati nelle automobili deve essere rivestita con uno strato protettivo.
Motori (elettrici):
I motori elettrici delle navi e delle unità industriali esposti ad ambienti difficili e umidi sono più vulnerabili alla corrosione e ad altri processi di degrado superficiale.
Le industrie possono garantire la protezione della superficie dei magneti per ottenere prestazioni migliori in ambienti umidi e corrosivi tenendo conto dell'importanza, sopra discussa, del rivestimento della superficie dei magneti permanenti.
Metodi comuni di protezione superficiale per magneti permanenti
Esistono diversi metodi di superficie sul mercato per la protezione dei magneti permanenti dalla corrosione e da altri effetti di degradazione della superficie. Alcuni dei metodi di protezione della superficie sono descritti di seguito:
Rivestimento organico:
La forte protezione superficiale dei magneti permanenti dagli effetti delle sostanze chimiche e dell'umidità, viene eseguita con il rivestimento del poliuretano e della resina epossidica sulla superficie dei magneti. Questo rivestimento è chiamato rivestimento organico. La resistenza all'impatto e la proprietà di adesione dei magneti vengono aumentate con la formazione di uno strato protettivo sulla superficie dei magneti. I magneti sono colorati e rifiniti in modo uniforme con questo tipo di rivestimento, quindi i magneti rivestiti sono molto fattibili o adatti per applicazioni estetiche.
Trattamento di ossidazione:
Per i magneti in neodimio ferro boro (NdFeB) e SmCo (Samario Cobalto), il metodo di trattamento di ossidazione è molto adatto. In questa tecnica, uno strato controllato di ossido viene formato sulla superficie dei magneti. Con questa tecnica, la durata e la resistenza alla corrosione dei magneti permanenti vengono aumentate per le condizioni di ambiente umido e duro.
Metodo di placcatura:
Per la protezione superficiale dei magneti permanenti vengono utilizzate tecniche di placcatura come la zincatura e la nichel-rame-nichel.
Rivestimento di tipo zincato:
Protezione della superficie dei magneti permanenti per un breve periodo di tempo, il metodo di zincatura è un metodo molto adatto ed economico. Lo strato sacrificale dello zinco è prodotto sulla superficie dei magneti che si corrode a causa dell'ambiente corrosivo e protegge il magnete. Il metodo di zincatura non è usato generalmente a causa della protezione a breve termine dall'ambiente corrosivo.
Placcatura tipo nichel rame nichel:
Per la protezione superficiale dei magneti permanenti, il metodo più comunemente utilizzato è Nickel Copper Nickel. Questo metodo di placcatura a triplo strato offre un'elevata capacità di resistenza alla corrosione migliorando l'aderenza e la tenacità dei magneti permanenti. Il rivestimento esterno in nichel fornisce una protezione extra e rende questa tecnica molto fattibile per diverse applicazioni del settore.
Rivestimento sotto vuoto:
Il rivestimento sotto vuoto è noto come metodo di deposizione fisica da vapore ed è particolarmente adatto alle condizioni ambientali difficili grazie all'elevata resistenza alla corrosione e alle forti proprietà di adesione.
Placcatura chimica:
Rivestimento in lega di nichel-fosforo:
In questa tecnica, la placcatura in lega di nichel fosforo viene eseguita sulla superficie dei magneti permanenti per migliorare la resistenza alla corrosione in condizioni umide e corrosive. Questo tipo di placcatura viene eseguito in diversi spessori per aumentare la resistenza all'usura in base ai requisiti dell'ambiente.
Metodo di rivestimento parilene:
Per ottenere un'eccellente resistenza alla corrosione e una sottigliezza extra dei magneti permanenti, il metodo di rivestimento in parilene è ampiamente utilizzato per le sue proprietà altamente specializzate. I magneti di forme complesse vengono rivestiti con questa tecnica facilmente e perfettamente senza compromettere le prestazioni magnetiche. Questa tecnica ha applicazioni nell'elettronica e nelle apparecchiature mediche.
Incapsulamento impermeabile:
L'incapsulamento impermeabile è un metodo di protezione completo in cui un rivestimento in materiale plastico o epossidico viene applicato sulla superficie dei magneti permanenti per proteggere i magneti dalle condizioni di elevata umidità. La durata a lungo termine e le prestazioni dei magneti sono garantite con questa tecnica di rivestimento e forniscono una soluzione fattibile per le condizioni ambientali del server. Rende inoltre la superficie dei magneti a prova di contaminazione e umidità.
Confronto dei vantaggi e degli svantaggi dei vari metodi di protezione delle superfici
I requisiti necessari devono essere considerati durante la selezione del metodo di protezione adatto. I fattori di questi metodi di rivestimento sono discussi nella seguente tabella.
| Resistenza alla corrosione |
| Complessità della produzione | Caratteristiche delle prestazioni | Scenario applicabile | ||
Rivestimento di zinco | Medio | Basso | Basso | Mediamente resistente alla corrosione, meno costoso, per condizioni non corrosive | Protezione per un periodo di tempo più breve | ||
Rivestimento organico | Alto | Medio | Medio | fattibile per forme complesse, fornisce protezione dalla corrosione dovuta a sostanze chimiche | Per condizioni chimiche e di elevata umidità | ||
Placcatura in nichel rame-nichel | Alto | Medio | Medio | Offre un'eccellente resistenza alla corrosione, ampiamente utilizzato | Adatto a condizioni umide | ||
Rivestimento chimico (lega nichel-fosforo) | Molto alto | Medio | alto | Adatto a condizioni difficili grazie all'elevata resistenza alla corrosione | Per applicazioni marine (altamente corrosive) | ||
Spruzzatura/placcatura sotto vuoto | Molto alto | alto | alto | Costo molto elevato Resistenza alle alte temperature e protezione delle superfici | Per strumenti di precisione | ||
Tecnica di ossidazione | Basso | Basso | Basso | Stabilità della superficie migliorata, prestazioni di protezione più deboli | Adatto per magneti SmCo | ||
Incapsulamento dell'acqua | Molto alto | Da medio ad alto | Da medio ad alto | Più adatto per ambienti subacquei ed esterni | Stabile per esposizione a lungo termine all'umidità | ||
Tecnica di rivestimento parilene | Molto alto | Alto | alto | Più adatto per applicazioni sensibili e elevata resistenza alla corrosione | Per elettronica e medicina |
Come scegliere la giusta soluzione per la protezione delle superfici
La selezione del metodo di protezione superficiale adatto per i magneti permanenti è molto critica perché ne sono garantite le prestazioni e la longevità. Gli elementi importanti che devono essere considerati sono elencati di seguito:
Elevata resistenza all'umidità: Dovrebbe essere utilizzata una tecnica di rivestimento che presenti un'elevata resistenza alla corrosione e all'umidità.
Stabilità alle alte temperature: il rivestimento che rimane stabile in condizioni di alte temperature.
Adatto per applicazioni in ambienti salati o marini: il metodo di protezione della superficie è adatto e può sopportare le condizioni dell'acqua salata.
Durata vs costo:
La durabilità dovrebbe essere preferita al costo della tecnica di rivestimento, perché alcuni metodi di rivestimento sono costosi ma hanno una maggiore durata e durata grazie all'uso di materiali di alta qualità e tecniche di applicazione.
Guida alla selezione:
- Identificazione dell'ambiente di lavoro: industriale, interno ed esterno.
- Tipi di elementi corrosivi come acqua salata, sostanze chimiche.
- Requisito di prestazione
- Selezione della tecnica in base alle esigenze e al budget.
Cosa possiamo fare per la protezione superficiale dei magneti permanenti?
Siamo altamente specializzati nel fornire una protezione superficiale di alta qualità per i magneti permanenti.
Il nostro team vanta una vasta esperienza nella fornitura di servizi di protezione superficiale per magneti permanenti, con conoscenze approfondite e competenze per la selezione della tecnica adatta in base alle condizioni di progettazione.
Rivestimento | Nome della procedura tecnica | Colore | Spessore (μm) | Durata (h) | Temperatura (℃) | Ambiente | ||
Acqua dolce | Umido Prova di calore | PCT | ||||||
Zn bianco | Rivestimento elettrico | Blu | 4-10 | 24 | 48 | — | <160 | Temperatura normale |
Zn colorato | Rivestimento elettrico | Colorato | 4-10 | 48 | 48 | — | <160 | Temperatura normale |
Ni chimico | Rivestimento chimico | Argento | 8-15 | 96 | 300 | 48 | <200 | Ambiente corrosivo |
Ni-Ni | Rivestimento elettrico | Argento+ Bianco | 10-20 | 72 | 300 | 48 | <200 |
Ambiente corrosivo |
Ni-Cu-Ni | Rivestimento elettrico | Argento+ Bianco | 12-25 | 72 | 500 | 48 | <200 | |
Ni-Cu-Ni+Sn | Rivestimento elettrico | Argento+ Bianco | 12-25 | 72 | 500 | 96 | <200 | Ambiente corrosivo |
Epossidica spruzzata | Elettroforesi | Nero o grigio | 15-30 | 96 | 120 | — | <180 |
Ambiente fortemente corrosivo |
Epossidico Ni-Cu+ | Rivestimento elettrico +Elettroforesi | Nero o grigio | 25-45 | 500 | 1000 | — | <200 | |
Lubrificante per sempre | Rivestimento elettrico | Giallo | 10-20 | 72 | 500 | 72 | -70~180 | |
Fosfato/Passivato | Deposizione chimica | Grigio scuro | 1-2 | — | — | — | <500 | Protezione temporanea |
Alluminio sottovuoto | Rivestimento sotto vuoto | Argento+ Bianco | 2-10 | 100 | 500 | 72 | <500 | Temperatura fluttuante Ambiente |
Teflon | Rivestimento elettrico | Nero | 8-15 | 24 | 120 | 48 | <260 | Resistenza alle alte temperature |
Tendenze future nella protezione permanente delle superfici dei materiali magnetici
Guardiamo con interesse allo sviluppo e al progresso delle tecniche di protezione delle superfici parallelamente all'avanzamento della tecnologia.
Tecnologie per l'anticorrosione:
Grazie all'invenzione di nuove tecnologie, la durata e la resistenza dei magneti permanenti alle condizioni ambientali più difficili saranno aumentate.
Materiali innovativi:
Anticipando l'impiego di materiali nuovi e innovativi per il rivestimento dei magneti permanenti, che possano offrire elevate prestazioni e durata.
Rispettoso dell'ambiente:
Sono in corso lavori di ricerca e sviluppo per mitigare l'impatto nocivo di questi rivestimenti sull'ambiente.
Conclusione
I magneti al neodimio ferro boro (NdFeB) sono più vulnerabili alla corrosione e alle condizioni ambientali severe, quindi i rivestimenti superficiali protettivi sono essenziali per questi magneti permanenti per sostenere le prestazioni e aumentare la durata. La tecnica di rivestimento superficiale adatta ed efficace può rendere questi magneti molto utili per l'ambiente umido e corrosivo, ma anche migliorare le prestazioni e la durata.
Per mantenere le proprietà magnetiche per un periodo di tempo più lungo, è essenziale scegliere la tecnica di rivestimento superficiale più adatta per i magneti permanenti. I rischi e i pericoli per l'ambiente possono essere ridotti con tecniche di protezione superficiale su misura.
Per consigli e soluzioni professionali, invitiamo i clienti a contattarci in qualsiasi momento. Siamo altamente esperti e abbiamo competenze diversificate nei metodi di protezione delle superfici e vi forniremo un servizio di qualità.
Contattateci per una guida e una soluzione per le tecniche di protezione della superficie e per sapere come selezionare la tecnica giusta per i vostri magneti. Possiamo aumentare le prestazioni e la durata dei vostri magneti permanenti con la vostra collaborazione.