How Are SmCo Magnets Made?
Table of Contents
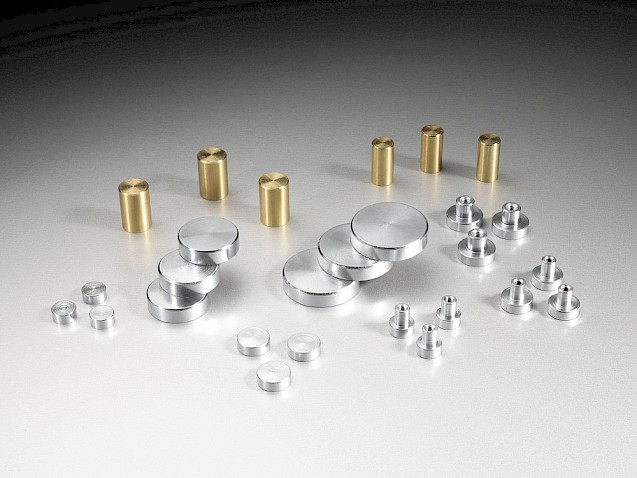
Made from a mix of samarium and cobalt, SmCo magnets are a mainstay of many high-tech sectors. Particularly at high temperatures, these magnets are renowned for their stability and strength. How then are SmCo magnets produced? The complex method behind the production of extremely strong magnets will guide you on this page. From material preparation to finishing touches, every stage is vital for guaranteeing the magnets run as they should. This guide will provide all the knowledge you need whether your interests in SmCo magnets for a project or you’re fascinated in the production process.
What are SmCo Magnets?
Made essentially from samarium and cobalt, SmCo magnets—also known as samarium-cobalt magnets—are rare-earth magnets. Excellent magnetic qualities of these magnets—including high magnetic energy and corrosion resistance—are well-known. In specialized uses including aerospace, military, and high-performance motors, their capacity to survive high temperatures—up to 350°C—makes them especially important. SmCo magnets are useful in many different fields since they retain their magnetism under very demanding conditions unlike those of other magnets.
Common Types of SmCo Magnets
SmCo 1:5 and SmCo 2:17 are two primarily two varieties of SmCo magnets. Their composition and magnetic qualities define the two primarily differently. Comprising one part samarium and five parts cobalt, the SmCo 1:5 magnet provides good stability and high energy. Conversely, SmCo 2:17 magnets have an even greater magnetic energy product and a larger concentration of samarium. diverse uses call for diverse forms and sizes of both kinds.
SmCo 1:5 Magnets
One part samarium combined with five parts cobalt makes SmCo 1:5 magnets. These magnets have a nice mix between cost-effectiveness, temperature stability, and magnetic strength. They are especially helpful in uses where resistance to high temperatures is required and where modest magnetic strength is enough. Both industrial and automotive sectors find motors, sensors, and actuators using SmCo 1:5 magnets quite common. Generally less expensive than their SmCo 2:17 counterparts, they are perfect for uses with less performance requirements.
SmCo 2:17 Magnets
About two parts samarium for every seventeen parts cobalt, SmCo 2:17 magnets have a higher concentration of samarium. Their magnetic energy product is thus more than that of the SmCo 1:5 magnets. Superior magnetic strength, temperature resistance, and longevity abound from SmCo 2:17 magnets. High-performance motors, magnetic sensors, and aerospace applications where both high magnetic energy and stability at increased temperatures are required find frequent use for them. Though they are preferred in demanding applications, SmCo 2:17 magnets are usually more costly than SmCo 1:5 magnets because of their better performance.
Process Flow of SmCo Magnet
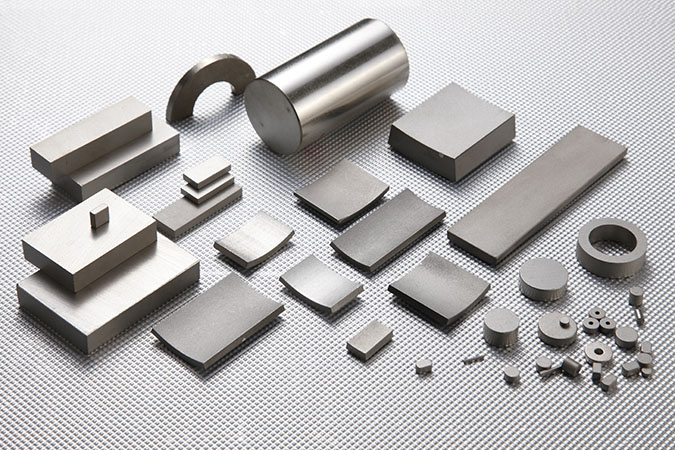
Making SmCo magnets is a very exact procedure with several processes that each help to define the final qualities of the magnet. As even the tiniest process variation can influence the performance of SmCo magnets, the manufacturing path calls for accuracy and knowledge. We shall explore each stage in more detail in this part, with particular attention to how these magnets are painstakingly created to satisfy industry standards and particular application criteria.
Step 1: Material Preparation
Careful choice and processing of raw materials comes first in making SmCo magnets. Samarium (Sm) and cobalt (Co) make up SmCo magnets mostly. Excellent magnetic qualities of these two materials led to their choice. The rare earth element samarium is in charge of the high magnetic field; cobalt improves the stability and corrosion resistance of the magnet.
Usually, the raw components also comprise minute concentrations of iron (Fe), copper (Cu), and other trace metals including zirconium (Zr) and hafnium (Hf). These extra components help the magnets to have better general magnetic performance, temperature stability, and longevity. Achieving the correct magnetic qualities depends on exactly combining these components. To guarantee the right ratios, the raw ingredients are weighed; meticulous calculations are done to prevent any composition imbalance.
The items are blended to create a homogeneous mixture once their measurements are precisely accurate. This combination is crucial to guarantee that the resultant product has constant magnetic characteristics over the whole magnet’s parts. One of the first stages toward making sure the SmCo magnet functions effectively over a variety of uses is the homogeneity of this material mix.
Step 2: Melting and Alloying
The melting and alloying procedure comes following the phase of material preparation. An induction furnace runs the measured samarium and cobalt as well as any other materials. To stop oxidation during the heating process, this furnace runs argon or another inert gas. Keeping the furnace atmosphere oxygen-free is therefore very important since oxidation would reduce the purity of the components, influencing the quality of the final magnet.
The components are heated to such high temperatures, where the cobalt and samarium melt and combine to create a homogeneous alloy. Following careful pouring into molds, this molten alloy forms solid ingots. Before more treatment, these ingots are the raw form of the magnet. Perfect pouring of the molten material guarantees the appropriate size and composition of the ingots.
Maintaining the stability of the alloy depends on closely regulating the furnace temperature as well as the pouring pace. Any temperature variations or inadequate cooling could produce variations in the magnetic qualities of the magnet. This stage then is a delicate balancing act between heat, time, and careful material management.
Step 3: Milling the Alloy
The cooled and hardened ingots break into smaller pieces that are subsequently ground into fine powders. Since it gets the material ready for the next phases of magnet manufacture, milling is a crucial stage in the magnet making process. Grinding machines feed the alloy ingots, which break down into a consistent particle size fine powder.
The following stage in magnet production depends on this powder since it lets the particles be shaped and aligned so that the magnetic field of the resultant product is maximized. To guarantee that the magnetic particles are tiny enough to be crushed or sintered into a solid structure later, the powder consistency must satisfy quite exact criteria.
The material is under continual observation in this grinding step to guarantee uniform particle size. Variations in particle size can cause variations in the ultimate magnetic strength and the general SmCo magnet performance.
Step 4: Pressing or Sintering
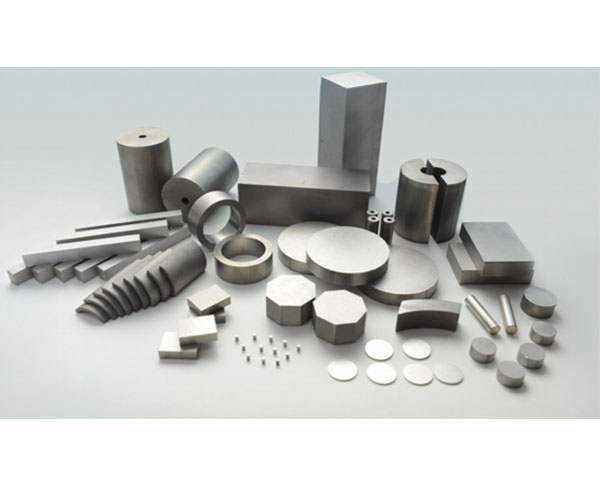
The powdered alloy should next be either pressed or sinterced into the required form. Pressing is forming a solid object by compaction of the powdered material under great pressure in a mold. For SmCo magnets, however, sintering—the more often used technique—involves a further heat treatment.
The powder is inserted into a die and heated very highly—up to 1250°C—just below the melting point during sintering. The fusion of the particles brought about by this heat produces a solid mass. The material is then chilled under a magnetic field to guarantee that the particles align in a manner maximizing the magnetic strength of the magnet. Ensuring the final magnet has maximum energy product and full coercivity—resistance to demagnetization—dependent on this stage is absolutely vital.
A heat-driven process, sintering calls for very exact temperature control. Too low a temperature will cause poor particle fusion; too high a temperature may cause the alloy to melt and lose its magnetic qualities. Moreover, the correct cooling under a magnetic field guarantees that the magnet keeps its intended strength and alignment.
Step 5: Machining and Finishing
Sintering leaves somewhat delicate resultant magnets that require more processing. Machining and polishing steps enable the magnet to be molded into its perfect shape. Usually polished to match strict dimensional limits, the sintered magnets have been ground down. This stage is absolutely important since the ultimate size and form of the magnet directly affect its application.
This process also comprises surface polishing and smoothing to remove any defects that might impact the performance or fit of the magnet into its intended usage. Precision is crucial during this step since any little error could lead to significant performance issues down the road.
Step 6: Coating and Magnetizing
The last processes of coating and magnetizing follow once the magnets have been machined into the required form and size. To increase their lifetime and stop corrosion, the magnets have a protective covering applied on them. Depending on the planned application of the magnet, common coatings are nickel (Ni), zinc (Zn), or other protective compounds.
The magnets go through a last process of magnetizing following coating. An external magnetic field is used during magnetization to align the magnetic domains within the material, therefore activating its magnetic qualities. This stage guarantees that the magnet can run in its expected use and reaches its full magnetic potential.
An important stage is magnetization since it finalizes the performance qualities of the magnet and activates its magnetic field. The whole strength, stability, and resistance to demagnetizing of the magnet depend on the type and strength of the magnetic field applied throughout this operation.
How to Choose the Surface Treatment of SmCo Magnet?
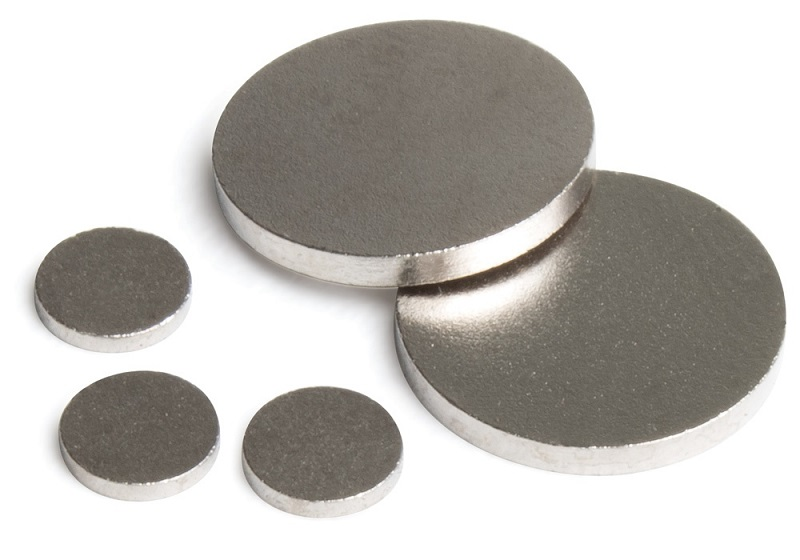
The lifetime of SmCo magnets is substantially enhanced by surface treatment. Different coatings are used to shield the magnets from oxidation, wear, and corrosion based on the application. Two most often used surface treatments for SmCo magnets are nickel (Ni) and zinc (Zn) coatings. Particularly in demanding surroundings like maritime or high-temperature conditions, these coatings extend the lifetime and performance of the magnet. The surface treatment should be selected with consideration for the surroundings the magnet will be utilized in and the required degree of protection.
The Advantages and Disadvantages of SmCo Magnets

Here are the benefits and drawbacks of SmCo magnets
Advantages
Superior features of SmCo magnets—high energy density, great temperature stability, and resistance to corrosion—are well recognized. For uses in high-temperature situations, such as in the aerospace and automotive sectors, they are perfect since they can run in temperatures up to 350°C. SmCo magnets also have a high coercivity, meaning they are resistant to demagnetization.
Disadvantages
Though SmCo magnets have several benefits, they are more brittle than other kinds of magnets, such NdFeB. its brittleness increases its susceptibility to impact or stress-related breakdown. Furthermore, their production’s cost of the raw materials influences their tendency to be more costly. Although they excel in demanding conditions, some uses may find their higher price point prohibitive.
Application Fields of SmCo Magnets
A wide range of sectors and uses find SmCo magnets applied. Key components in sectors including aerospace, military, and electronics are their great magnetic qualities and high temperature stability. SmCo magnets find use in propulsion systems and sensors needing longevity at high temperatures in aircraft. Additionally vital in electric motors for electric cars and medical equipment like MRI machines are they are. Furthermore demonstrating their adaptability across many sectors are magnetic levitation systems, wind turbines, and automotive sensors using SmCo magnets.
Conclusion
Strong magnetic qualities, temperature stability, and corrosion resistance define SmCo magnets as quite valuable. Made these magnets using exact methods including material preparation, sintering, machining, and coating. Although they have certain drawbacks—brittleness and cost, among other things—their special benefits make them absolutely vital in important uses. Whether your sector of employment is aerospace, electronics, or another, knowing how SmCo magnets are produced enables you to value their part in contemporary technology. SmCo magnets are a necessary part in high-tech systems since their adaptability paired with sophisticated manufacturing techniques guarantees that they will always inspire creativity in many sectors.