Why does neodymium magnet need coating?
Neodymium Magnets are produced by powder metallurgy process, which is a kind of chemically active powder material with tiny internal pores and cavities, which is easy to be corroded and oxidized in the air. After the material is corroded or component damage, it will cause the attenuation or even loss of magnetic properties over time, thus affecting the performance and life of the whole machine, so strict anti-corrosion treatment must be carried out before use.
At present, Neodymium Magnet anti-corrosion treatment commonly used plating, chemical plating, electrophoresis, phosphating treatment, etc., of which plating as a mature means of metal surface treatment is most widely used.
Coating types and characteristics of NdFeB magnets.
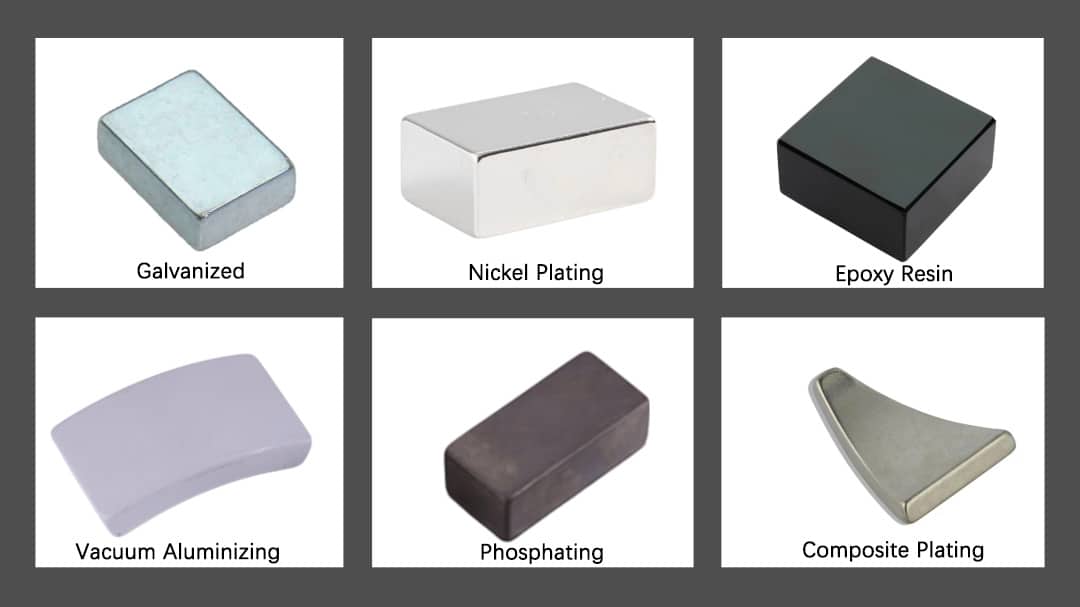
Neodymium Magnet plating adopts different plating process according to the different environment of product use, and the surface plating is also different, such as zinc plating, nickel plating, copper plating, tin plating, precious metal plating, etc. Generally, zinc plating, nickel plating+copper+nickel, nickel plating+copper+chemical nickel plating are the mainstream three processes. Only zinc and nickel are suitable for direct plating on the surface of NdFeB magnets, so multi-layer plating technology is generally implemented after nickel plating. Now has broken through the NdFeB magnet direct copper plating technology difficulties, direct copper plating and then nickel plating is the development trend, so that the plating design is more conducive to the NdFeB magnet components of the thermal demagnetization indicators to reach the customer needs.
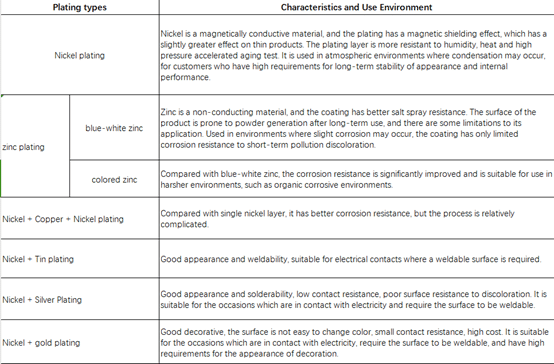
Corrosion resistance of common plating:
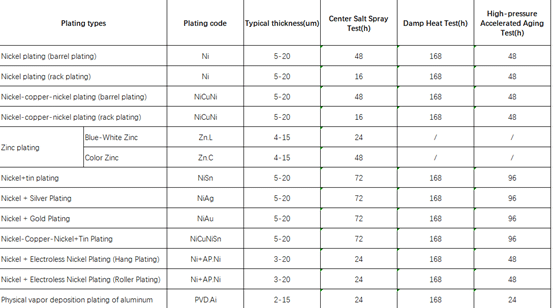
What is the difference between galvanized and nickel plated?
NdFeB magnets are most commonly used in galvanized and nickel plated, they have obvious differences in appearance, corrosion resistance, service life, price and so on:
Polishing difference: nickel plating is superior to zinc plating in polishing, the appearance is brighter. High requirements for the appearance of the product will generally choose nickel-plated, while some of the magnets are not exposed, the appearance of the product requires a relatively low general galvanized.
Corrosion resistance difference: zinc is active metal, can react with acid, so the corrosion resistance is poor; nickel-plated surface treatment, its corrosion resistance is higher.
Difference in service life: Due to different corrosion resistance, the service life of zinc plating is lower than that of nickel plating, which is mainly manifested in the fact that the plating layer on the surface is easy to fall off after a long time of use, leading to the oxidation of the magnet, thus affecting the magnetic properties.
Hardness difference: nickel plating is higher than zinc plating, in the process of use, you can greatly avoid the collision and other situations, making NdFeB powerful magnets appear to fall off the corner of the phenomenon, cracked, and so on.