Table des matières
Les aimants permanents NdFeB (néodyme fer bore) et SmCo (samarium cobalt) ont de nombreuses applications dans les secteurs de l'électronique (haut-parleurs, écouteurs), des énergies renouvelables (éoliennes), de la médecine et de l'automobile (moteurs, freins, embrayages). Ces aimants sont précieux pour différentes applications en raison de leurs propriétés exceptionnelles, mais certains facteurs environnementaux affectent leurs performances. Pour protéger ces aimants des effets des éléments environnementaux tels que la corrosion, la température et l'humidité, les surfaces de ces aimants doivent être recouvertes de couches protectrices. Lorsque les aimants sont exposés à des conditions d'humidité et de température élevées, leur surface est endommagée et leurs performances et leur efficacité sont affectées. Le coût du projet ou du produit augmente en raison de la réparation et du remplacement des aimants. Les aimants peuvent fonctionner mieux et plus longtemps et le produit est économique si un revêtement de surface de haute qualité est effectué.
Les différentes techniques et méthodes de protection de surface des aimants permanents, avec leurs avantages et leurs inconvénients, sont explorées et décrites dans cet article. Les critères de sélection des matériaux de protection appropriés pour les aimants permanents sont également décrits à titre indicatif et informatif pour les industries manufacturières et les clients.
La nécessité de la protection de surface des aimants permanents
Les caractéristiques matérielles des aimants permanents les rendent très vulnérables à la corrosion et aux autres effets de l'environnement. Les aimants permanents les plus vulnérables sont les aimants en néodyme fer bore (NdFeB) ayant une nature oxydante et ceux-ci sont très susceptibles de se corroder ou de présenter des problèmes de surface en étant exposés à l'humidité et à la corrosion. La nature corrosive de ces aimants est risquée et ne convient pas aux applications hautes performances et durables.
Les différentes techniques et méthodes de protection de surface des aimants permanents, avec leurs avantages et leurs inconvénients, sont explorées et décrites dans cet article. Les critères de sélection des matériaux de protection appropriés pour les aimants permanents sont également décrits à titre indicatif et informatif pour les industries manufacturières et les clients.
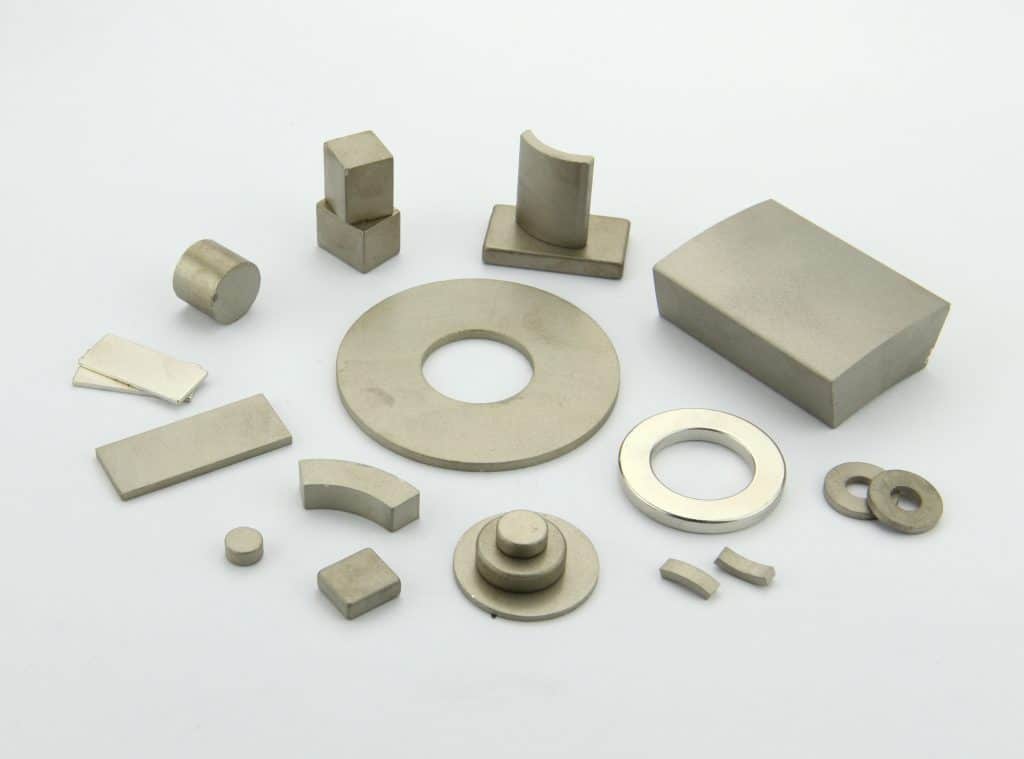
Sensibilité et susceptibilité des aimants à l'environnement corrosif :
Les propriétés magnétiques des aimants permanents, comme leurs performances et leur résistance, diminuent progressivement avec la corrosion. Le processus de dégradation de la surface et de corrosion des aimants s'accélère avec l'exposition continue aux produits chimiques et les variations de température et d'humidité. Les performances et l'efficacité des circuits magnétiques sont affectées et compromises et l'ensemble du système peut également tomber en panne même avec un faible effet de corrosion.
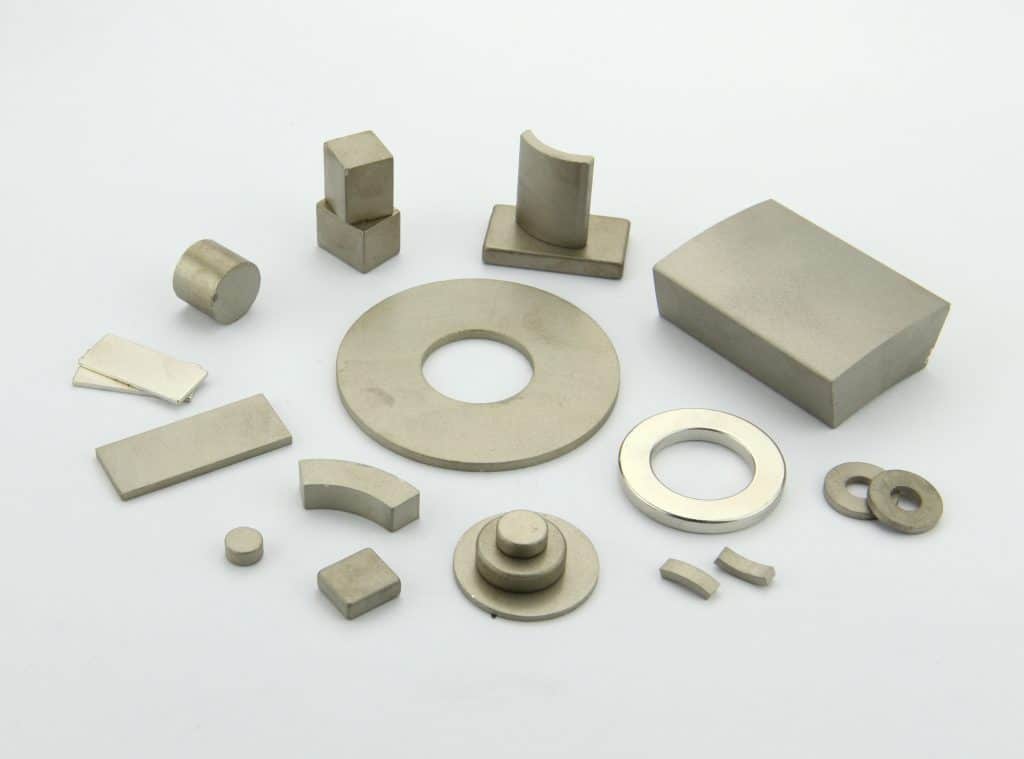
Améliorer la durabilité et la durée de vie des aimants :
La durabilité et la durée de vie des aimants peuvent être améliorées en élaborant et en mettant en œuvre des stratégies ou des techniques efficaces de protection de surface. La couche protectrice est produite sur la surface des aimants à l'aide de techniques de revêtement et protège contre les effets de l'humidité, de la corrosion et de l'oxydation, et la durée de vie des aimants est également augmentée. Les performances opérationnelles globales des aimants peuvent être augmentées et les coûts de maintenance réduits si des investissements sont réalisés dans des techniques de protection de surface. Les risques de défaillance de l'équipement peuvent également être atténués grâce à l'utilisation de techniques de protection de surface efficaces et de haute qualité.
Liste des applications nécessitant une résistance élevée à la corrosion :
Certaines des applications où une résistance élevée à la corrosion des aimants permanents est requise sont répertoriées ci-dessous :
Instruments médicaux :
Les instruments médicaux tels que l'imagerie par résonance magnétique (IRM) et les appareils de diagnostic fonctionnent avec le champ magnétique des aimants permanents. Les aimants permanents fournissent un environnement de champ magnétique continu dans ces appareils pour un fonctionnement durable et fiable.
Automobiles:
Les aimants permanents sont les principaux composants des capteurs et des moteurs des automobiles et sont plus exposés aux effets environnementaux. Par conséquent, la surface des aimants permanents utilisés dans les automobiles doit être recouverte d'une couche protectrice.
Moteurs (électriques) :
Les moteurs électriques des navires et des unités industrielles exposés à des environnements difficiles et humides sont plus vulnérables à la corrosion et à d’autres processus de dégradation de surface.
Les industries peuvent assurer la protection de la surface des aimants pour de meilleures performances dans les environnements humides et corrosifs en considérant l'importance discutée ci-dessus du revêtement de la surface des aimants permanents.
Méthodes courantes de protection de surface pour les aimants permanents
Il existe sur le marché différentes méthodes de protection de surface pour protéger les aimants permanents contre la corrosion et d'autres effets de dégradation de surface. Certaines des méthodes de protection de surface sont décrites ci-dessous :
Revêtement organique :
La protection de surface des aimants permanents contre les effets des produits chimiques et de l'humidité est assurée par le revêtement de la surface des aimants en polyuréthane et en résine époxy. Ce revêtement est appelé revêtement organique. La résistance aux chocs et la propriété d'adhérence des aimants sont augmentées grâce à la formation d'une couche protectrice sur la surface des aimants. Les aimants sont colorés et finis en douceur avec ce type de revêtement, de sorte que les aimants revêtus sont très réalisables ou adaptés à des applications esthétiques.
Traitement d'oxydation :
Pour les aimants en néodyme fer bore (NdFeB) et SmCo (samarium cobalt), la méthode de traitement par oxydation est très appropriée. Dans cette technique, une couche contrôlée d'oxyde est formée sur la surface des aimants. Avec cette technique, la durabilité et la résistance à la corrosion des aimants permanents sont augmentées pour les conditions d'environnement humide et difficile.
Méthode de placage :
Des techniques de placage telles que le zinc et le nickel-cuivre-nickel sont utilisées pour la protection de surface des aimants permanents.
Type de placage au zinc :
La protection de la surface des aimants permanents pendant une courte période de temps, la méthode de placage au zinc est une méthode très appropriée et économique. La couche sacrificielle de zinc est produite sur la surface des aimants qui se corrode en raison de l'environnement corrosif et protège l'aimant. La méthode de placage au zinc n'est généralement pas utilisée en raison de la protection à court terme contre l'environnement corrosif.
Nickel Cuivre Type de placage au nickel :
Pour la protection de surface des aimants permanents, le nickel-cuivre-nickel est la méthode la plus couramment utilisée. Cette méthode de placage à trois couches offre une capacité de résistance élevée contre la corrosion en améliorant l'adhérence et la ténacité des aimants permanents. Le revêtement externe en nickel offre une protection supplémentaire et rend cette technique très pratique pour différentes applications de l'industrie.
Revêtement sous vide :
Le revêtement sous vide est connu sous le nom de méthode de dépôt physique en phase vapeur et convient parfaitement aux conditions environnementales difficiles en raison de sa résistance élevée à la corrosion et de ses fortes propriétés de liaison.
Placage chimique :
Placage d'alliage nickel-phosphore :
Dans cette technique, le placage en alliage nickel-phosphore est effectué sur la surface des aimants permanents pour améliorer la résistance à la corrosion dans des conditions humides et corrosives. Ce type de placage est réalisé en différentes épaisseurs pour augmenter la résistance à l'usure en fonction des exigences de l'environnement.
Méthode de revêtement en parylène :
Pour obtenir une excellente résistance à la corrosion et une finesse supplémentaire des aimants permanents, la méthode de revêtement au parylène est largement utilisée en raison de ses propriétés hautement spécialisées. Les aimants de formes complexes sont recouverts avec cette technique facilement et parfaitement sans affecter les performances magnétiques. Cette technique a des applications dans l'électronique et les équipements médicaux.
Encapsulation étanche à l'eau :
L'encapsulation étanche est une méthode de protection complète dans laquelle un revêtement en plastique ou en époxy est appliqué sur la surface des aimants permanents pour protéger les aimants des conditions d'humidité élevée. La durabilité et les performances à long terme des aimants sont assurées par cette technique de revêtement et offrent une solution viable aux conditions environnementales du serveur. Cela rend également la surface des aimants résistante à la contamination et à l'humidité.
Comparaison des avantages et des inconvénients des différentes méthodes de protection de surface
Les exigences nécessaires doivent être prises en compte lors du choix de la méthode de protection appropriée. Les facteurs de ces méthodes de revêtement sont présentés dans le tableau suivant.
| Résistance à la corrosion |
| Complexité de la production | Caractéristiques de performance | Scénario applicable | ||
Revêtement de zinc | Moyen | Faible | Faible | Résistance moyenne à la corrosion, moins coûteuse, pour conditions non corrosives | Protection pour une période plus courte | ||
Revêtement organique | Haut | Moyen | Moyen | réalisable pour les formes complexes, offre une protection contre la corrosion due aux produits chimiques | Pour conditions chimiques et d'humidité élevée | ||
Placage nickel-cuivre-nickel | Haut | Moyen | Moyen | Offre une excellente résistance à la corrosion, largement utilisé | Adapté aux conditions humides | ||
Placage chimique (alliage nickel-phosphore) | Très haut | Moyen | haut | Adapté aux conditions difficiles grâce à sa haute résistance à la corrosion | Pour applications marines (hautement corrosif) | ||
Projection sous vide / placage | Très haut | haut | haut | Coût très élevé Résistance aux hautes températures et protection de surface | Pour instruments de précision | ||
Technique d'oxydation | Faible | Faible | Faible | La stabilité de la surface est améliorée, mais les performances de protection sont plus faibles | Convient aux aimants SmCo | ||
Encapsulation de l'eau | Très haut | Moyen à élevé | Moyen à élevé | Idéal pour les environnements sous-marins et extérieurs | Stable pour une exposition à long terme à l'humidité | ||
Technique de revêtement au parylène | Très haut | Haut | haut | Idéal pour les applications sensibles et une résistance élevée à la corrosion | Pour l'électronique et le médical |
Comment choisir la bonne solution de protection de surface
Le choix de la méthode de protection de surface appropriée pour les aimants permanents est très important car les performances et la longévité sont garanties. Les éléments importants à prendre en compte sont énumérés ci-dessous :
Haute résistance à l’humidité : Il convient d'utiliser une technique de revêtement présentant une résistance élevée à la corrosion et à l'humidité.
Stabilité à haute température : le revêtement qui reste stable dans des conditions de température élevée.
Convient aux applications salées ou marines : La méthode de protection de surface est adaptée et peut supporter les conditions de l'eau salée.
Durabilité vs coût :
La durabilité doit être préférée au coût de la technique de revêtement, car certaines méthodes de revêtement sont coûteuses mais ont une durabilité et une durée de vie plus élevées grâce à l'utilisation de matériaux de haute qualité et à une technique d'application.
Guide de sélection :
- Identification de l'environnement de travail comme industriel, intérieur et extérieur.
- Type d'éléments corrosifs comme le sel, les produits chimiques, l'eau.
- Exigence de performance
- Sélection de la technique en fonction des besoins et du budget.
Que pouvons-nous faire pour la protection de surface des aimants permanents ?
Nous possédons une grande expertise dans la fourniture d’une protection de surface de haute qualité pour les aimants permanents.
Notre équipe possède une grande expérience dans la fourniture de services de protection de surface pour aimants permanents avec des connaissances et des compétences approfondies pour la sélection de la technique appropriée en fonction des conditions de conception.
Revêtement | Nom de la procédure technique | Couleur | Épaisseur (μm) | Durée(h) | Température (℃) | Environnement | ||
SST | Humide Test de chaleur | PCT | ||||||
Zinc blanc | Revêtement électrique | Bleu | 4-10 | 24 | 48 | — | <160 | Température normale |
Zn coloré | Revêtement électrique | Coloré | 4-10 | 48 | 48 | — | <160 | Température normale |
Ni chimique | Revêtement chimique | Argent | 8-15 | 96 | 300 | 48 | <200 | Environnement corrosif |
Ni-Ni | Revêtement électrique | Argent + Blanc | 10-20 | 72 | 300 | 48 | <200 |
Environnement corrosif |
Ni-Cu-Ni | Revêtement électrique | Argent + Blanc | 12-25 | 72 | 500 | 48 | <200 | |
Ni-Cu-Ni+Sn | Revêtement électrique | Argent + Blanc | 12-25 | 72 | 500 | 96 | <200 | Environnement corrosif |
Époxy pulvérisé | Électrophorèse | Noir ou Gris | 15-30 | 96 | 120 | — | <180 |
Environnement fortement corrosif |
Ni-Cu+ Époxy | Revêtement électrique +Électrophorèse | Noir ou Gris | 25-45 | 500 | 1000 | — | <200 | |
Everlube | Revêtement électrique | Jaune | 10-20 | 72 | 500 | 72 | -70~180 | |
Phosphate/Passivé | Dépôt chimique | Gris foncé | 1-2 | — | — | — | <500 | Protection temporaire |
Aluminium sous vide | Revêtement sous vide | Argent + Blanc | 2-10 | 100 | 500 | 72 | <500 | Température fluctuante Environnement |
Téflon | Revêtement électrique | Noir | 8-15 | 24 | 120 | 48 | <260 | Résistance à haute température |
Tendances futures en matière de protection de surface des matériaux magnétiques permanents
Nous attendons avec impatience le développement et le progrès des techniques de protection de surface avec l’avancement de la technologie.
Technologies anticorrosion :
La durée de vie et la durabilité des aimants permanents seront augmentées dans des conditions environnementales difficiles grâce à l'invention de nouvelles technologies.
Matériaux innovants :
Anticipant les matériaux nouveaux et innovants pour le revêtement des aimants permanents qui peuvent offrir des performances et une durabilité élevées.
Respectueux de l'environnement :
Des travaux de recherche et développement sont menés pour atténuer l’impact nocif de ces revêtements sur l’environnement.
Conclusion
Les aimants en néodyme fer bore (NdFeB) sont plus vulnérables à la corrosion et aux conditions environnementales difficiles. Il est donc essentiel de revêtir ces aimants permanents de revêtements de surface protecteurs pour maintenir leurs performances et augmenter leur durabilité. La technique de revêtement de surface appropriée et efficace peut rendre ces aimants très utiles dans les environnements humides et corrosifs, mais également améliorer leurs performances et leur durabilité.
Pour conserver les propriétés magnétiques plus longtemps, il est essentiel de choisir la technique de revêtement de surface la plus adaptée aux aimants permanents. Les risques et dangers pour l'environnement peuvent être réduits grâce à des techniques de protection de surface sur mesure.
Pour des recommandations et des solutions professionnelles, nous encourageons les clients à nous contacter à tout moment. Nous sommes très expérimentés et disposons d'une expertise diversifiée dans les méthodes de protection de surface qui vous fourniront un service de qualité.
N'hésitez pas à nous contacter pour obtenir des conseils et des solutions concernant les techniques de protection de surface et pour savoir comment sélectionner la technique adaptée à vos aimants. Grâce à votre coopération, nous pouvons augmenter les performances et la durabilité de vos aimants permanents.