Table des matières
Les aimants en néodyme fer bore (NdFeB), aujourd'hui considérés comme les aimants permanents les plus puissants, sont largement utilisés dans des secteurs tels que l'électronique, l'automobile, les énergies renouvelables et les soins de santé.
Malgré leur puissance, leur seul point faible est leur grande sensibilité à la corrosion et à l'oxydation, notamment dans des environnements humides et chimiquement agressifs. C'est pourquoi le revêtement magnétique en NdFeB est si important.
Le revêtement assure la préservation des propriétés magnétiques, une durabilité accrue, de meilleures performances et une sécurité accrue dans diverses applications. L'inadaptation du revêtement entraîne une détérioration rapide de ces aimants et, par conséquent, une réduction de leur fonctionnalité, voire la défaillance de composants critiques.
Cette revue vise à explorer les différents types de revêtements disponibles pour les aimants NdFeB, à comparer leurs performances et à choisir le plus adapté à une application. Les procédés de revêtement, les avantages de leur application et les tendances futures affectant cet aspect crucial de la technologie des aimants seront également abordés.
Partie 1 : Matériaux de revêtement courants pour les aimants NdFeB
Les aimants NdFeB sont très réactifs aux facteurs environnementaux tels que l'humidité et l'oxygène, ce qui peut rapidement corroder leurs surfaces et leur intégrité magnétique. Ces revêtements sont appliqués pour éviter ce type de détérioration.
Les revêtements les plus connus pour les aimants NdFeB sont les suivants :
Revêtement en nickel (Ni-Cu-Ni)
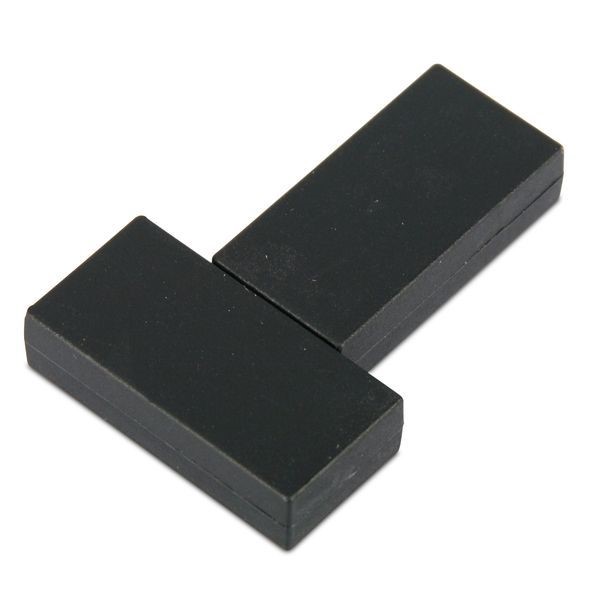
Le nickel est le matériau de revêtement le plus utilisé. En effet, il offre les meilleures caractéristiques de résistance à la corrosion, de solidité et d'esthétique. Ce revêtement est généralement réalisé en trois couches (nickel-cuivre-nickel) pour une finition métallique brillante et longue durée.
Les deux premières couches de nickel protègent contre la corrosion et l'usure, tandis que la couche intermédiaire en cuivre assure adhérence et flexibilité. Ce produit est destiné aux applications industrielles générales, à l'électronique et aux particuliers.
Revêtement époxy
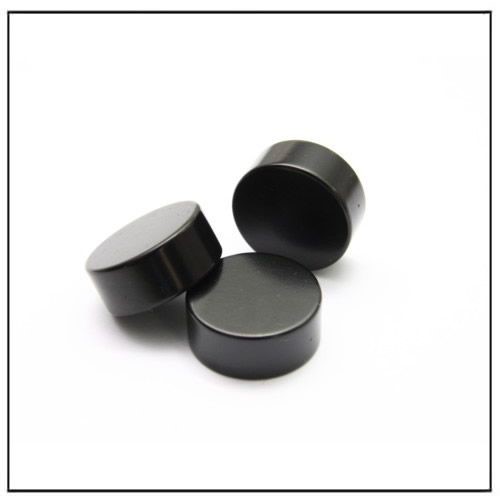
L'époxy est la protection ultime dans les environnements humides, mouillés ou chimiquement agressifs. Ce revêtement non métallique forme une couche protectrice épaisse qui résiste à l'humidité, aux embruns salins et à la corrosion chimique.
Ils sont disponibles en différentes couleurs, comme le noir, le gris, et même dans des formulations personnalisées pour s'adapter aux applications nécessitant protection et respect de l'environnement. En termes de résistance mécanique, l'époxy est moins performant que les revêtements métalliques, mais cela le rend adapté aux applications marines, automobiles et extérieures.
Revêtement de zinc (Zn)
Les revêtements de zinc sont avant tout économiques. Ils offrent une résistance modérée à la corrosion et sont très faciles à appliquer, par galvanoplastie ou mécaniquement. Le zinc agit principalement comme un revêtement sacrificiel : il se corrode avant l'aimant lui-même.
Bien qu'ils ne soient pas très bien adaptés aux environnements très difficiles, les revêtements en Zn pourraient être sélectionnés assez souvent pour des applications intérieures à faible risque où l'exposition à l'humidité serait assez limitée.
Revêtement au phosphate
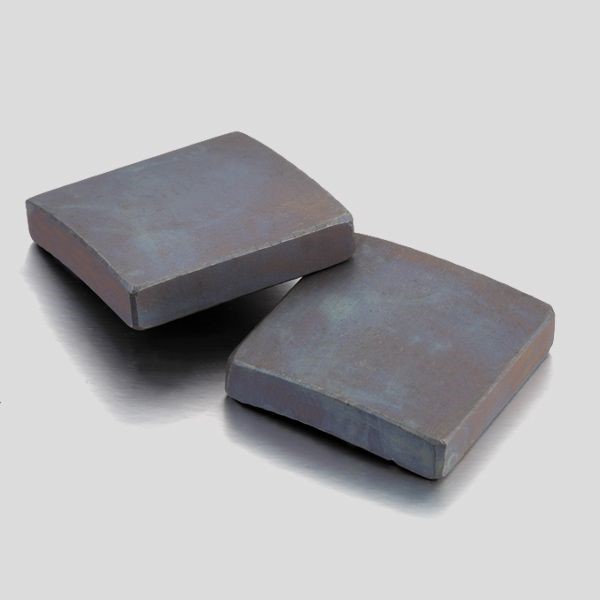
La phosphatation est généralement utilisée comme première couche pour favoriser l'adhérence lors de l'application de peinture ou d'autres revêtements. Les traitements au phosphate sont peu résistants à la corrosion, bien qu'ils puissent légèrement contribuer à augmenter la rugosité de surface.
Revêtement en or (Au)
Les applications des revêtements d'or sont très spécifiques. La plupart sont utilisées en médecine et dans l'aérospatiale. L'or est inerte, biocompatible et extrêmement résistant à la corrosion, ce qui en fait l'élément idéal pour les implants ou les dispositifs exposés à des fluides corporels ou à des produits chimiques agressifs.
L’or lui-même est extrêmement coûteux et n’est donc utilisé que dans les situations où ses propriétés uniques sont les plus cruciales.
Revêtement en parylène
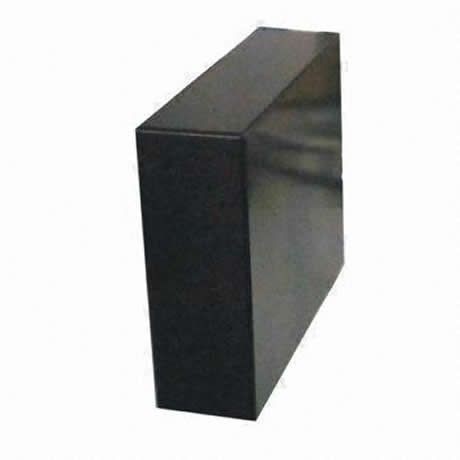
Le parylène est un revêtement polymère produit par dépôt chimique en phase vapeur. Il permet de former une barrière extrêmement fine et sans piqûres, sans interaction avec les substrats.
Cette barrière offre une résistance remarquable à l'humidité, aux produits chimiques et à la température. Les revêtements en parylène sont généralement utilisés pour les composants électroniques, médicaux et aérospatiaux exigeant précision et fiabilité.
Partie 2. Introduction aux performances des matériaux de revêtement couramment utilisés
Voici un bref aperçu des performances de ces matériaux dans des domaines clés :
Matériau de revêtement | Résistance à la corrosion | Résistance mécanique | Stabilité thermique | Coût | Cas d'utilisation courants |
Ni-Cu-Ni | Haut | Haut | Modéré | Modéré | Électronique à usage général |
Époxy | Très élevé | Modéré | Faible à modéré | Faible | Marine, usage extérieur |
Zinc | Modéré | Modéré | Faible | Faible | Environnements à faible risque |
Phosphate | Faible | Faible | Faible | Très faible | Couche de prétraitement |
Or | Très élevé | Modéré | Haut | Haut | Médical, aérospatial |
Parylène | Excellent | Modéré | Haut | Très élevé | Électronique de précision |
Partie 3. Comment choisir le matériau de revêtement des aimants NdFeB ?
Il est bien connu que les aimants NdFeB doivent être dotés d'un revêtement spécifique pour maintenir leur intégrité et leurs performances dans différentes applications. La protection contre la corrosion et l'usure, grâce à un choix judicieux du revêtement des aimants NdFeB, doit également garantir leur compatibilité avec les exigences mécaniques, thermiques et environnementales.
Voici quelques facteurs à prendre en compte lors du choix d’un matériau de revêtement :
Exposition environnementale
Parmi d’autres facteurs, l’environnement opérationnel peut être considéré comme le facteur le plus important pour décider du revêtement à utiliser pour les aimants NdFeB.
Dans des conditions intérieures sèches, avec une faible humidité ou une faible exposition aux produits chimiques, un revêtement standard en nickel-cuivre-nickel (Ni-Cu-Ni) peut être utilisé. Il offre une bonne résistance à la corrosion et un éclat métallique exceptionnel, idéal pour l'électronique grand public et les applications industrielles simples.
Si les aimants doivent être exposés aux conditions extérieures, ou dans des environnements très humides ou salins, un revêtement plus robuste sera nécessaire. La plupart des époxydes résistants à l'humidité sont fiables ; sinon, le parylène offre une surface parfaitement étanche et sans piqûres.
Usure mécanique et manutention
Les aimants NdFeB dynamiques ou utilisés dans des environnements à frottement élevé nécessitent des revêtements de protection spécifiques contre les dommages physiques. Les revêtements en nickel sont particulièrement adaptés aux applications nécessitant une manipulation, des chocs mécaniques ou un enchevêtrement dans un système mécanique, car ils présentent une grande dureté et une grande résistance à l'usure.
En revanche, lorsque l'aimant n'est pas soumis à des forces mécaniques importantes, mais nécessite une protection contre les intempéries lors de l'installation, l'époxy peut être une option judicieuse. Bien qu'il ne présente pas la même robustesse mécanique que les métaux, il offre une protection supérieure à la moyenne et s'adapte facilement aux formes complexes.
Tolérance à la température
La température de fonctionnement est un autre facteur important à prendre en compte pour le revêtement des aimants NdFeB. La chaleur est très néfaste pour ces aimants, et une exposition de quelques instants à la chaleur entraînerait leur démagnétisation permanente.
Les revêtements n'empêcheraient pas la démagnétisation de l'aimant, mais protégeraient sa surface de l'oxydation thermique. Les revêtements de nickel et d'or présentent une stabilité à des températures modérément élevées et préservent une bonne intégrité structurelle.
En revanche, les revêtements époxy ont une tolérance très limitée à la chaleur, se dégradant ou se ramollissant à des températures élevées, ce qui les rend inutilisables pour les applications à haute température. Le parylène, déposé par dépôt en phase vapeur, présente une excellente stabilité thermique et doit être traité avec une extrême prudence dans les environnements à haute température.
Exigences électriques et fonctionnelles
Les revêtements utilisés dans les applications électroniques ou médicales doivent respecter des caractéristiques électriques et biologiques. Les revêtements comme l'époxy et le parylène sont de bons isolants. Cette propriété les rend adaptés aux applications magnétiques en électronique, où les courts-circuits électriques doivent être évités.
Le parylène est particulièrement adapté aux applications en électronique de précision et en aérospatiale grâce à sa capacité à former des revêtements très fins et uniformes. Dans le domaine biomédical, l'or et le parylène sont biocompatibles et non toxiques et peuvent être utilisés en toute sécurité dans les dispositifs médicaux internes ou les instruments en contact avec les tissus biologiques.
Coûts et contraintes budgétaires
Le budget pour le revêtement des aimants NdFeB est raisonnable, mais absolument nécessaire. Lorsque la modélisation des coûts est importante, les revêtements de zinc ou de phosphate offrent une protection de base au moindre coût, adaptée aux applications intérieures non critiques.
Les nickels sont les plus fréquemment utilisés en raison de leur excellent rapport qualité-prix, de leur résistance à la corrosion et de leur durabilité. Dans les applications haut de gamme ou spécialisées, on utilise des revêtements en or, en parylène et en PTFE. Cependant, en raison de leur coût, ils sont généralement réservés aux applications critiques où les performances requises justifient amplement leur coût.
Considération esthétique et besoins de personnalisation
Partout où l'aspect esthétique de l'aimant est important dans l'électronique grand public, les produits promotionnels ou les applications décoratives, l'esthétique des revêtements entre en jeu.
Les revêtements en nickel offrent une surface métallique brillante, à la fois esthétique et fonctionnelle. Les revêtements époxy, quant à eux, sont personnalisables en termes de couleurs et de textures, offrant ainsi une alternative aux entreprises souhaitant que leurs composants s'inscrivent dans un thème visuel précis.
Partie 4. Comment les aimants NdFeB sont-ils revêtus ?
L'application d'un revêtement sur les aimants NdFeB est un procédé essentiel pour leur longévité et leurs performances dans divers environnements. Voici quelques procédés de revêtement reconnus pour les aimants NdFeB.
Galvanoplastie
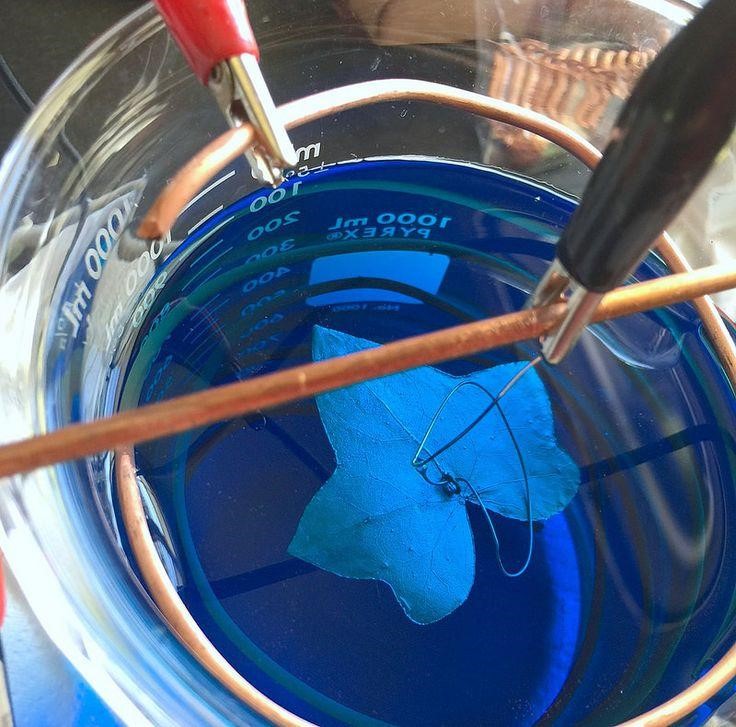
Le nickel, le cuivre ou l'or sont les métaux couramment utilisés pour le dépôt électrolytique des aimants NdFeB. L'aimant est plongé dans une solution électrolytique composée de sels métalliques pour le processus d'électrodéposition.
On peut obtenir un revêtement métallique très fin et uniforme, doté d'excellentes propriétés de résistance à la corrosion et à l'usure. Il s'agit généralement d'un revêtement électrolytique Ni-Cu-Ni, offrant un bon compromis entre performance et coût.
Revêtement en poudre
Le revêtement en poudre permet l'application de différents types de revêtements non métalliques, y compris certains liquides comme l'époxy. La poudre sèche est chargée électrostatiquement puis pulvérisée sur la surface de l'aimant.
Les particules chargées électrostatiquement se fixent mécaniquement à la surface de l'aimant, puis se lient à celle-ci après durcissement au four. Il en résulte la formation d'une couche épaisse et résistante à l'usure, offrant une protection contre l'humidité, les produits chimiques et l'abrasion.
Revêtement par immersion
Le revêtement par immersion est un moyen très simple et très économique d'obtenir un revêtement époxy et phosphaté de type marin. Il suffit de plonger l'aimant dans une solution de revêtement, et un revêtement homogène est appliqué sur toutes les surfaces.
Si la solution est laissée sécher après immersion, l'opération peut être répétée pour obtenir l'épaisseur souhaitée. Le revêtement par immersion est généralement utilisé lorsqu'une précision élevée n'est pas requise, mais nécessite une protection contre la corrosion ou les agressions environnementales.
Revêtement par pulvérisation
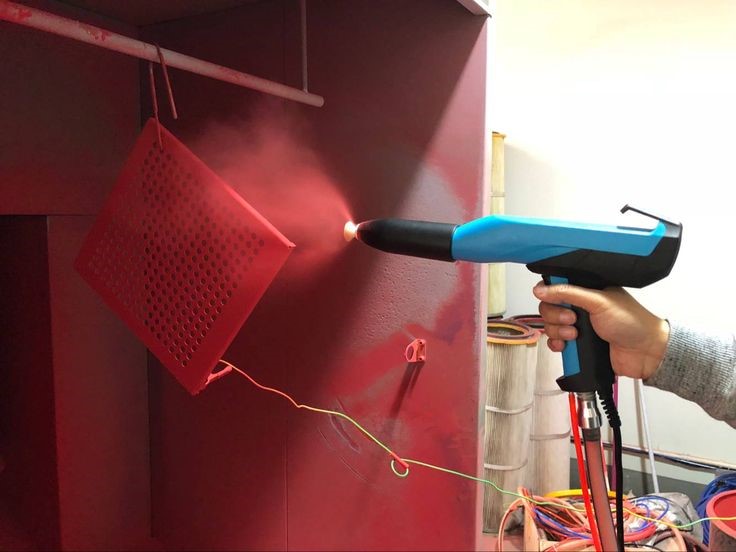
Le revêtement par pulvérisation consiste à appliquer un matériau de revêtement à l'aide d'un aérographe ou d'un pulvérisateur, principalement pour les époxydes ou les peintures. Le matériau de revêtement est atomisé en fines gouttelettes et pulvérisé directement sur la surface de l'aimant. Cette technique est souvent utilisée.
Partie 5 : Quels avantages le revêtement apporte-t-il aux aimants NdFeB ?
Voici quelques-uns des avantages que l’on obtient en revêtant des aimants NdFed :
- Protection contre la corrosion – Protège de l’humidité et de l’oxygène les aimants rouillés.
- Durabilité améliorée – Augmente la résistance aux dommages physiques lors de la manipulation.
- Stabilité thermique – Protège des températures élevées, une démagnétisation se produit.
- Résistance chimique – concernant la corrosion en milieu chimique ou marin.
- Plus de valeur esthétique – Présente un aspect très soigné et professionnel aux biens de consommation.
- Biocompatibilité- Sans danger pour les implants médicaux et les outils chirurgicaux.
- Isolation électrique – Empêche les courts-circuits même dans les assemblages électroniques à contact étroit.
Partie 6. Orientation future du développement du revêtement des aimants NdFeB
La demande d’aimants NdFeB augmente et augmentera dans les années à venir pour les technologies modernes, notamment les applications dans les véhicules électriques, les systèmes d’énergie renouvelable et l’électronique miniaturisée.
Par conséquent, des solutions de revêtement améliorées seront nécessaires. Les développements futurs dans ce domaine viseront à améliorer les performances, la durabilité et la polyvalence des revêtements d'aimants NdFeB.
L'un des axes majeurs de cette démarche serait la formulation de nanorevêtements et de systèmes multicouches offrant une excellente protection pour un poids minimal. Ces revêtements devraient permettre d'obtenir des films multicouches ultra-minces, conçus pour résister à la corrosion, être stables thermiquement et résister à l'usure dans des environnements soumis à de fortes contraintes, le tout dans un format compact.
Un autre aspect concerne les progrès vers des revêtements respectueux de l'environnement et non toxiques. De plus, face au durcissement de la réglementation, les chercheurs étudient le remplacement de ces matériaux dangereux par des alternatives écologiques pour la galvanoplastie.
Les nouveaux revêtements intelligents pourraient également être considérés comme très prometteurs. Cette innovation prolongerait considérablement la durée de vie des aimants NdFeB dans des environnements extrêmes ou dynamiques.
On observe également une demande croissante de solutions de revêtement personnalisées pour différents secteurs, par exemple des revêtements biocompatibles pour les dispositifs médicaux, des revêtements résistants à la chaleur pour les applications aérospatiales, etc. La technologie progresse constamment, et il existe donc un besoin de revêtements sur mesure et flexibles.
Conclusion
Les aimants NdFeB sont sans doute parmi les aimants permanents les plus puissants jamais connus ; cependant, leur véritable potentiel n'est réalisé que lorsqu'ils sont associés au revêtement approprié pour les protéger.
À mesure que la technologie progresse, les exigences en matière de matériaux magnétiques évoluent, ouvrant de nouvelles perspectives d'innovation en matière de méthodes et de matériaux de revêtement. Si vous travaillez sur l'électronique de nouvelle génération, les systèmes d'énergie renouvelable ou les outils médicaux de précision, il est essentiel de comprendre et de choisir le revêtement idéal pour vos aimants NdFeB.