Comment sont fabriqués les aimants SmCo ?
Table des matières
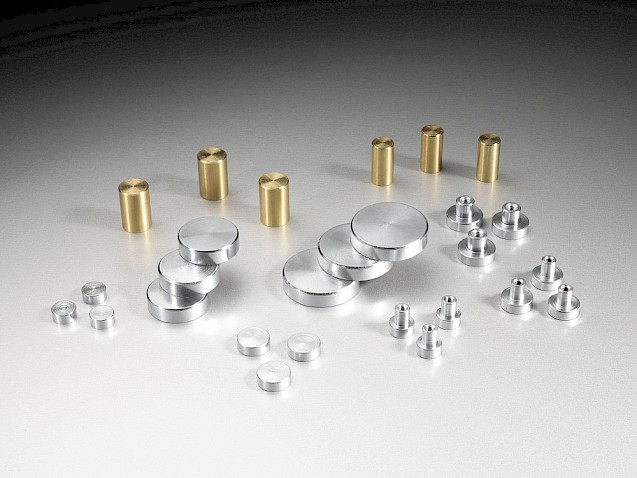
Fabriqué à partir d'un mélange de samarium et de cobalt, Aimants SmCo Les aimants SmCo sont un pilier de nombreux secteurs de haute technologie. Particulièrement à haute température, ils sont réputés pour leur stabilité et leur résistance. Comment sont fabriqués les aimants SmCo ? Cette page vous guidera dans la fabrication complexe d'aimants extrêmement puissants. De la préparation du matériau aux finitions, chaque étape est essentielle pour garantir le bon fonctionnement des aimants. Ce guide vous apportera toutes les connaissances nécessaires, que vous soyez intéressé par les aimants SmCo pour un projet ou passionné par le processus de production.
Que sont les aimants SmCo ?
Composés essentiellement de samarium et de cobalt, les aimants SmCo, également appelés aimants samarium-cobalt, sont des aimants à base de terres rares. Leurs excellentes propriétés magnétiques, notamment leur énergie magnétique élevée et leur résistance à la corrosion, sont reconnues. Dans des applications spécialisées comme l'aérospatiale, le militaire et les moteurs haute performance, leur capacité à résister à des températures élevées, jusqu'à 350 °C, les rend particulièrement importants. Les aimants SmCo sont utiles dans de nombreux domaines, car ils conservent leur magnétisme dans des conditions très exigeantes, contrairement aux autres aimants.
Types courants d'aimants SmCo
Le SmCo 1:5 et le SmCo 2:17 sont deux variétés principales d'aimants SmCo. Leur composition et leurs propriétés magnétiques les distinguent fondamentalement. Composé d'une part de samarium et de cinq parts de cobalt, l'aimant SmCo 1:5 offre une bonne stabilité et une énergie élevée. À l'inverse, les aimants SmCo 2:17 présentent un produit énergétique magnétique encore plus élevé et une concentration en samarium plus importante. La diversité des utilisations exige des formes et des tailles variées pour les deux types.
Aimants SmCo 1:5
Les aimants SmCo 1:5 sont composés d'une part de samarium et de cinq parts de cobalt. Ces aimants offrent un excellent compromis entre rentabilité, stabilité thermique et force magnétique. Ils sont particulièrement utiles pour les applications nécessitant une résistance aux températures élevées et une force magnétique modérée. Les moteurs, capteurs et actionneurs utilisant des aimants SmCo 1:5 sont courants dans les secteurs industriel et automobile. Généralement moins chers que leurs homologues SmCo 2:17, ils sont parfaits pour les applications nécessitant des performances moindres.
Aimants SmCo 2:17
Les aimants SmCo 2:17, contenant environ deux parts de samarium pour dix-sept parts de cobalt, présentent une concentration plus élevée en samarium. Leur produit énergétique magnétique est donc supérieur à celui des aimants SmCo 1:5. Ils offrent une force magnétique, une résistance thermique et une longévité supérieures. Ils sont fréquemment utilisés dans les moteurs hautes performances, les capteurs magnétiques et les applications aérospatiales exigeant une énergie magnétique élevée et une stabilité à haute température. Bien qu'ils soient privilégiés dans les applications exigeantes, les aimants SmCo 2:17 sont généralement plus coûteux que les aimants SmCo 1:5 en raison de leurs meilleures performances.
Flux de processus de l'aimant SmCo
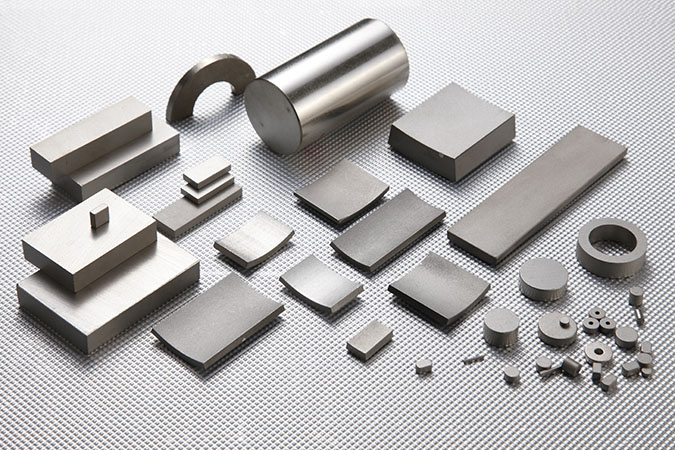
La fabrication des aimants SmCo est un procédé très précis, qui comprend plusieurs étapes qui contribuent chacune à définir les qualités finales de l'aimant. La moindre variation de procédé pouvant influencer les performances des aimants SmCo, le processus de fabrication exige précision et savoir-faire. Nous explorerons chaque étape plus en détail dans cette partie, en nous concentrant plus particulièrement sur la manière dont ces aimants sont minutieusement fabriqués pour répondre aux normes industrielles et aux critères d'application spécifiques.
Étape 1 : Préparation du matériel
La sélection et le traitement rigoureux des matières premières sont essentiels à la fabrication des aimants SmCo. Le samarium (Sm) et le cobalt (Co) constituent les principaux composants des aimants SmCo. Leurs excellentes propriétés magnétiques ont motivé leur choix. Le samarium, une terre rare, est responsable du champ magnétique élevé ; le cobalt améliore la stabilité et la résistance à la corrosion de l'aimant.
Habituellement, les composants bruts contiennent également d'infimes concentrations de fer (Fe), de cuivre (Cu) et d'autres traces de métaux, comme le zirconium (Zr) et l'hafnium (Hf). Ces composants supplémentaires améliorent les performances magnétiques générales, la stabilité thermique et la longévité des aimants. L'obtention des propriétés magnétiques optimales repose sur une combinaison précise de ces composants. Pour garantir les bons ratios, les ingrédients bruts sont pesés et des calculs minutieux sont effectués afin d'éviter tout déséquilibre de composition.
Une fois les mesures précises, les éléments sont mélangés pour obtenir un mélange homogène. Cette combinaison est essentielle pour garantir des caractéristiques magnétiques constantes sur l'ensemble des composants de l'aimant. L'une des premières étapes pour garantir l'efficacité de l'aimant SmCo dans diverses applications est l'homogénéité de ce mélange de matériaux.
Étape 2 : Fusion et alliage
La fusion et l'alliage interviennent après la préparation des matériaux. Un four à induction traite le samarium et le cobalt mesurés, ainsi que d'autres matériaux. Pour stopper l'oxydation pendant le chauffage, ce four utilise de l'argon ou un autre gaz inerte. Il est donc essentiel de maintenir l'atmosphère du four exempte d'oxygène, car l'oxydation réduirait la pureté des composants et affecterait la qualité de l'aimant final.
Les composants sont chauffés à des températures très élevées, où le cobalt et le samarium fondent et se combinent pour former un alliage homogène. Après un coulage minutieux dans des moules, cet alliage en fusion forme des lingots solides. Avant traitement ultérieur, ces lingots constituent la forme brute de l'aimant. Un coulage parfait du matériau en fusion garantit la taille et la composition appropriées des lingots.
Le maintien de la stabilité de l'alliage dépend d'une régulation précise de la température du four et de la vitesse de coulée. Toute variation de température ou un refroidissement inadéquat peut entraîner des variations des qualités magnétiques de l'aimant. Cette étape est donc un équilibre délicat entre chaleur, temps et gestion rigoureuse des matériaux.
Étape 3 : Fraisage de l'alliage
Les lingots refroidis et durcis se brisent en morceaux plus petits qui sont ensuite broyés en fines poudres. Le broyage est une étape cruciale du processus de fabrication des aimants, car il prépare le matériau pour les phases suivantes. Des rectifieuses alimentent les lingots d'alliage, qui se décomposent en une fine poudre de granulométrie homogène.
L'étape suivante de la production d'aimants dépend de cette poudre, car elle permet de façonner et d'aligner les particules afin de maximiser le champ magnétique du produit obtenu. Pour garantir que les particules magnétiques soient suffisamment fines pour être broyées ou frittées ultérieurement en une structure solide, la consistance de la poudre doit répondre à des critères très précis.
Le matériau est soumis à une surveillance continue lors de cette étape de broyage afin de garantir une granulométrie uniforme. Les variations de granulométrie peuvent entraîner des variations de la force magnétique ultime et des performances générales de l'aimant SmCo.
Étape 4 : Pressage ou frittage
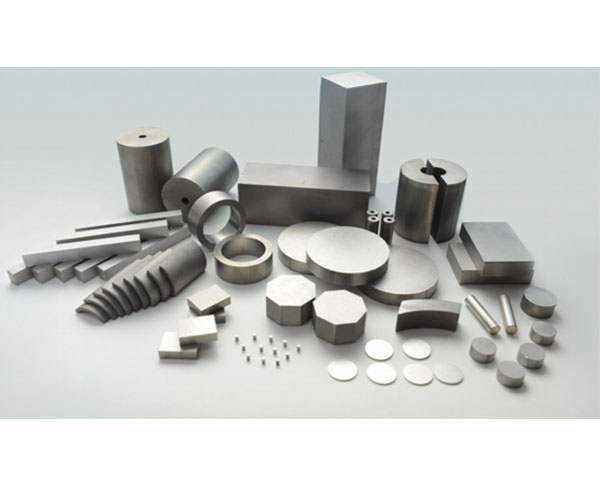
L'alliage en poudre doit ensuite être pressé ou fritté pour obtenir la forme souhaitée. Le pressage consiste à former un objet solide par compaction de la poudre sous forte pression dans un moule. Pour les aimants SmCo, le frittage, technique la plus courante, implique un traitement thermique supplémentaire.
La poudre est insérée dans une matrice et chauffée à très haute température – jusqu'à 1 250 °C – juste en dessous du point de fusion pendant le frittage. La fusion des particules provoquée par cette chaleur produit une masse solide. Le matériau est ensuite refroidi sous champ magnétique afin de garantir l'alignement des particules et de maximiser la force magnétique de l'aimant. Il est absolument crucial que l'aimant final présente un produit énergétique maximal et une coercivité totale (résistance à la démagnétisation) qui dépend de cette étape.
Procédé thermique, le frittage exige un contrôle très précis de la température. Une température trop basse entraînera une mauvaise fusion des particules ; une température trop élevée peut entraîner la fusion de l'alliage et la perte de ses propriétés magnétiques. De plus, un refroidissement correct sous champ magnétique garantit que l'aimant conserve sa résistance et son alignement.
Étape 5 : Usinage et finition
Le frittage produit des aimants fragiles qui nécessitent un traitement plus poussé. Les étapes d'usinage et de polissage permettent de mouler l'aimant pour lui donner sa forme parfaite. Généralement polis pour respecter des limites dimensionnelles strictes, les aimants frittés sont ensuite meulés. Cette étape est essentielle, car la taille et la forme finales de l'aimant influencent directement son application.
Ce processus comprend également le polissage et le lissage de la surface afin d'éliminer tout défaut susceptible d'affecter les performances ou l'adéquation de l'aimant à son usage prévu. La précision est cruciale lors de cette étape, car la moindre erreur peut entraîner des problèmes de performances importants à terme.
Étape 6 : Revêtement et magnétisation
Les dernières étapes de revêtement et de magnétisation suivent une fois les aimants usinés à la forme et à la taille souhaitées. Pour prolonger leur durée de vie et prévenir la corrosion, les aimants sont recouverts d'un revêtement protecteur. Selon l'application prévue, les revêtements les plus courants sont le nickel (Ni), le zinc (Zn) ou d'autres composés protecteurs.
Les aimants subissent une dernière étape de magnétisation après le revêtement. Un champ magnétique externe est utilisé pendant la magnétisation pour aligner les domaines magnétiques du matériau, activant ainsi ses propriétés magnétiques. Cette étape garantit que l'aimant peut fonctionner comme prévu et atteindre son plein potentiel magnétique.
La magnétisation est une étape importante, car elle finalise les performances de l'aimant et active son champ magnétique. La force, la stabilité et la résistance à la démagnétisation de l'aimant dépendent du type et de l'intensité du champ magnétique appliqué tout au long de cette opération.
Comment choisir le traitement de surface de l'aimant SmCo ?
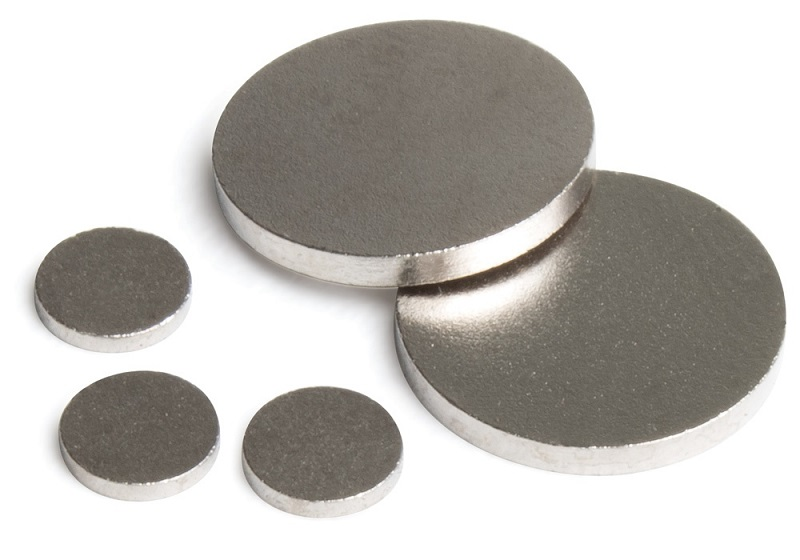
La durée de vie des aimants SmCo est considérablement améliorée par le traitement de surface. Différents revêtements sont utilisés pour protéger les aimants de l'oxydation, de l'usure et de la corrosion, selon l'application. Les deux traitements de surface les plus fréquemment utilisés pour les aimants SmCo sont les revêtements de nickel (Ni) et de zinc (Zn). Ces revêtements prolongent la durée de vie et les performances de l'aimant, en particulier dans les environnements exigeants comme les environnements maritimes ou les températures élevées. Le traitement de surface doit être choisi en fonction de l'environnement d'utilisation de l'aimant et du degré de protection requis.
Avantages et inconvénients des aimants SmCo

Voici les avantages et les inconvénients des aimants SmCo
Avantages
Les caractéristiques exceptionnelles des aimants SmCo – densité énergétique élevée, excellente stabilité thermique et résistance à la corrosion – sont reconnues. Pour les applications à haute température, comme dans les secteurs aérospatial et automobile, ils sont parfaits car ils peuvent fonctionner jusqu'à 350 °C. Les aimants SmCo présentent également une coercivité élevée, ce qui signifie qu'ils résistent à la démagnétisation.
Inconvénients
Bien que les aimants SmCo présentent de nombreux avantages, ils sont plus fragiles que d'autres types d'aimants, comme le NdFeB. Leur fragilité augmente leur sensibilité aux chocs ou aux ruptures dues aux contraintes. De plus, le coût de production des matières premières influence leur prix élevé. Bien qu'ils excellent dans des conditions exigeantes, leur prix élevé peut être prohibitif pour certaines applications.
Domaines d'application des aimants SmCo
Les aimants SmCo sont utilisés dans de nombreux secteurs et applications. Leurs excellentes propriétés magnétiques et leur stabilité à haute température sont des composants clés dans des secteurs tels que l'aérospatiale, le militaire et l'électronique. Ils sont utilisés dans les systèmes de propulsion et les capteurs nécessitant une longue durée de vie à haute température dans les avions. Ils sont également essentiels dans les moteurs électriques des voitures électriques et les équipements médicaux comme les appareils d'IRM. Les systèmes de lévitation magnétique, les éoliennes et les capteurs automobiles utilisant des aimants SmCo démontrent également leur adaptabilité à de nombreux secteurs.
Conclusion
Leurs fortes qualités magnétiques, leur stabilité thermique et leur résistance à la corrosion confèrent aux aimants SmCo une valeur inestimable. Ces aimants sont fabriqués selon des méthodes rigoureuses, incluant la préparation du matériau, le frittage, l'usinage et le revêtement. Malgré certains inconvénients (fragilité et coût, entre autres), leurs atouts spécifiques les rendent indispensables pour des applications importantes. Que vous travailliez dans l'aérospatiale, l'électronique ou un autre secteur, comprendre le processus de fabrication des aimants SmCo vous permet d'apprécier leur rôle dans les technologies contemporaines. Les aimants SmCo sont indispensables aux systèmes de haute technologie, car leur adaptabilité, associée à des techniques de fabrication sophistiquées, garantit qu'ils inspireront toujours la créativité dans de nombreux secteurs.