¿Cómo se fabrican los imanes de SmCo?
Tabla de contenido
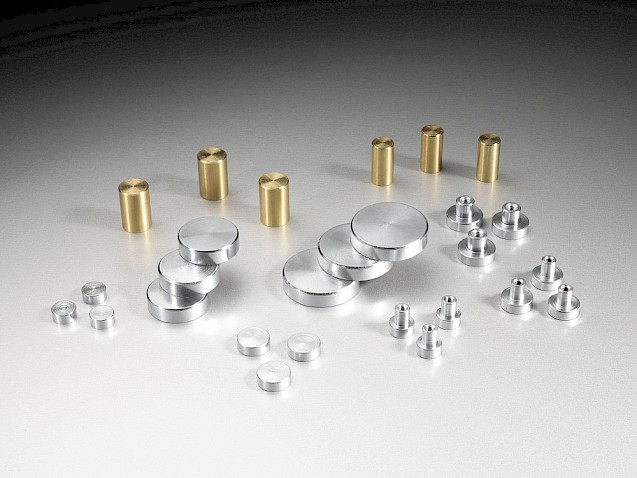
Hecho de una mezcla de samario y cobalto, Imanes de SmCo Son un pilar de muchos sectores de alta tecnología. Especialmente a altas temperaturas, estos imanes son reconocidos por su estabilidad y resistencia. ¿Cómo se producen los imanes de SmCo? El complejo método de producción de imanes extremadamente potentes le guiará en esta página. Desde la preparación del material hasta los retoques finales, cada etapa es vital para garantizar el correcto funcionamiento de los imanes. Esta guía le proporcionará toda la información necesaria, tanto si le interesan los imanes de SmCo para un proyecto como si le fascina el proceso de producción.
¿Qué son los imanes SmCo?
Fabricados esencialmente con samario y cobalto, los imanes de SmCo, también conocidos como imanes de samario-cobalto, son imanes de tierras raras. Sus excelentes propiedades magnéticas, como su alta energía magnética y resistencia a la corrosión, son bien conocidas. En aplicaciones especializadas, como la industria aeroespacial, militar y en motores de alto rendimiento, su capacidad para soportar altas temperaturas (hasta 350 °C) los hace especialmente importantes. Los imanes de SmCo son útiles en diversos campos, ya que conservan su magnetismo en condiciones muy exigentes, a diferencia de otros imanes.
Tipos comunes de imanes de SmCo
El SmCo 1:5 y el SmCo 2:17 son dos variedades principales de imanes de SmCo. Su composición y propiedades magnéticas los definen de forma muy diferente. Compuesto por una parte de samario y cinco partes de cobalto, el imán de SmCo 1:5 proporciona buena estabilidad y alta energía. Por el contrario, los imanes de SmCo 2:17 tienen un producto de energía magnética aún mayor y una mayor concentración de samario. Sus diversos usos requieren diversas formas y tamaños de ambos tipos.
Imanes SmCo 1:5
Una parte de samario combinada con cinco partes de cobalto produce imanes de SmCo 1:5. Estos imanes ofrecen una excelente combinación de rentabilidad, estabilidad térmica y fuerza magnética. Son especialmente útiles en aplicaciones donde se requiere resistencia a altas temperaturas y una fuerza magnética moderada es suficiente. Tanto en el sector industrial como en el automotriz, los motores, sensores y actuadores que utilizan imanes de SmCo 1:5 son bastante comunes. Generalmente más económicos que sus equivalentes de SmCo 2:17, son perfectos para aplicaciones con menores requisitos de rendimiento.
Imanes SmCo 2:17
Con aproximadamente dos partes de samario por cada diecisiete partes de cobalto, los imanes de SmCo 2:17 presentan una mayor concentración de samario. Por lo tanto, su producto de energía magnética es mayor que el de los imanes de SmCo 1:5. Los imanes de SmCo 2:17 ofrecen una fuerza magnética, resistencia a la temperatura y longevidad superiores. Se utilizan con frecuencia en motores de alto rendimiento, sensores magnéticos y aplicaciones aeroespaciales donde se requiere alta energía magnética y estabilidad a altas temperaturas. Si bien son preferidos en aplicaciones exigentes, los imanes de SmCo 2:17 suelen ser más costosos que los de SmCo 1:5 debido a su mejor rendimiento.
Flujo de proceso del imán de SmCo
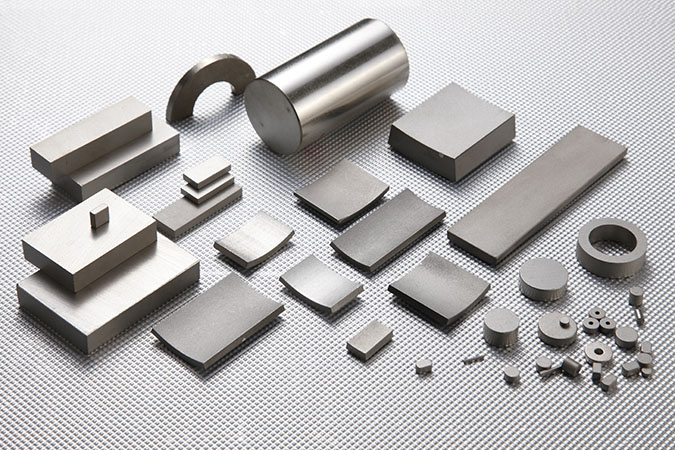
La fabricación de imanes de SmCo es un procedimiento muy preciso con varios procesos que contribuyen a definir las características finales del imán. Dado que incluso la más mínima variación en el proceso puede influir en el rendimiento de los imanes de SmCo, el proceso de fabricación requiere precisión y conocimiento. En esta sección, analizaremos cada etapa con más detalle, prestando especial atención a la meticulosa creación de estos imanes para cumplir con los estándares de la industria y los criterios de aplicación específicos.
Paso 1: Preparación del material
La selección y el procesamiento cuidadosos de las materias primas son primordiales en la fabricación de imanes de SmCo. El samario (Sm) y el cobalto (Co) componen principalmente los imanes de SmCo. Las excelentes propiedades magnéticas de estos dos materiales justificaron su elección. El samario, un elemento de tierras raras, es responsable del alto campo magnético; el cobalto mejora la estabilidad y la resistencia a la corrosión del imán.
Generalmente, las materias primas también contienen pequeñas concentraciones de hierro (Fe), cobre (Cu) y otros metales traza, como circonio (Zr) y hafnio (Hf). Estos componentes adicionales contribuyen a un mejor rendimiento magnético general, estabilidad térmica y longevidad de los imanes. Para lograr las cualidades magnéticas correctas, es fundamental combinar con precisión estos componentes. Para garantizar las proporciones correctas, se pesan las materias primas y se realizan cálculos meticulosos para evitar cualquier desequilibrio en la composición.
Los elementos se mezclan para crear una mezcla homogénea una vez que sus mediciones son precisas. Esta combinación es crucial para garantizar que el producto resultante tenga características magnéticas constantes en todas las partes del imán. Uno de los primeros pasos para asegurar el funcionamiento eficaz del imán de SmCo en diversos usos es la homogeneidad de esta mezcla de materiales.
Paso 2: Fusión y aleación
El proceso de fusión y aleación se lleva a cabo tras la fase de preparación del material. Un horno de inducción procesa el samario y el cobalto medidos, así como cualquier otro material. Para evitar la oxidación durante el proceso de calentamiento, este horno utiliza argón u otro gas inerte. Por lo tanto, es fundamental mantener la atmósfera del horno libre de oxígeno, ya que la oxidación reduciría la pureza de los componentes y afectaría la calidad del imán final.
Los componentes se calientan a temperaturas tan altas que el cobalto y el samario se funden y combinan para crear una aleación homogénea. Tras un cuidadoso vertido en moldes, esta aleación fundida forma lingotes sólidos. Antes de un tratamiento posterior, estos lingotes constituyen la materia prima del imán. El vertido perfecto del material fundido garantiza el tamaño y la composición adecuados de los lingotes.
Mantener la estabilidad de la aleación depende de una estricta regulación de la temperatura del horno, así como del ritmo de vertido. Cualquier variación de temperatura o un enfriamiento inadecuado podría producir variaciones en las propiedades magnéticas del imán. Esta etapa, por lo tanto, requiere un delicado equilibrio entre el calor, el tiempo y una gestión cuidadosa del material.
Paso 3: Fresado de la aleación
Los lingotes enfriados y endurecidos se fragmentan en fragmentos más pequeños que posteriormente se muelen hasta obtener un polvo fino. Dado que prepara el material para las siguientes fases de la fabricación de imanes, el fresado es una etapa crucial en el proceso de fabricación de imanes. Las rectificadoras alimentan los lingotes de aleación, que se descomponen en un polvo fino de tamaño de partícula uniforme.
La siguiente etapa en la producción de imanes depende de este polvo, ya que permite moldear y alinear las partículas para maximizar el campo magnético del producto resultante. Para garantizar que las partículas magnéticas sean lo suficientemente diminutas como para triturarlas o sinterizarlas posteriormente en una estructura sólida, la consistencia del polvo debe cumplir criterios muy precisos.
El material se somete a una supervisión continua durante esta etapa de molienda para garantizar la uniformidad del tamaño de las partículas. Las variaciones en el tamaño de las partículas pueden provocar variaciones en la fuerza magnética final y en el rendimiento general del imán de SmCo.
Paso 4: Prensado o sinterización
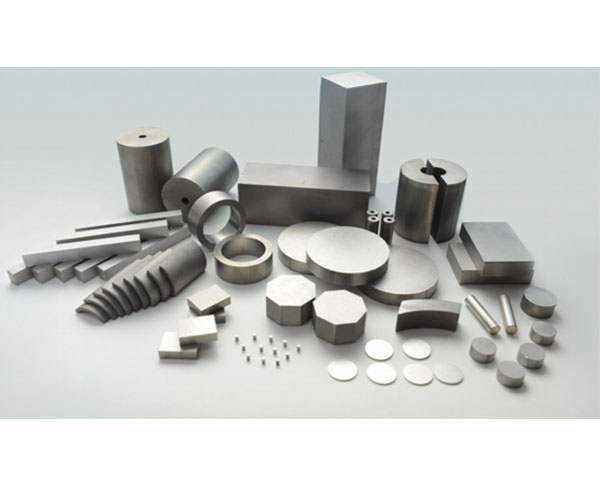
A continuación, la aleación en polvo debe prensarse o sinterizarse para obtener la forma deseada. El prensado consiste en formar un objeto sólido mediante la compactación del material en polvo a alta presión en un molde. Sin embargo, para los imanes de SmCo, la sinterización (la técnica más utilizada) implica un tratamiento térmico adicional.
El polvo se inserta en una matriz y se calienta a una temperatura muy alta (hasta 1250 °C), justo por debajo del punto de fusión durante la sinterización. La fusión de las partículas, provocada por este calor, produce una masa sólida. A continuación, el material se enfría bajo un campo magnético para garantizar que las partículas se alineen de forma que se maximice la fuerza magnética del imán. Es fundamental garantizar que el imán final tenga el máximo producto de energía y una coercitividad completa (resistencia a la desmagnetización) en función de esta etapa.
La sinterización, un proceso impulsado por calor, requiere un control de temperatura muy preciso. Una temperatura demasiado baja provocará una fusión deficiente de las partículas; una temperatura demasiado alta puede provocar que la aleación se funda y pierda sus propiedades magnéticas. Además, el enfriamiento correcto bajo un campo magnético garantiza que el imán mantenga su fuerza y alineación previstas.
Paso 5: Mecanizado y acabado
La sinterización produce imanes algo delicados que requieren mayor procesamiento. El mecanizado y el pulido permiten moldear el imán a su forma perfecta. Generalmente pulidos para cumplir con estrictos límites dimensionales, los imanes sinterizados han sido rectificados. Esta etapa es fundamental, ya que el tamaño y la forma finales del imán afectan directamente su aplicación.
Este proceso también incluye el pulido y alisado de la superficie para eliminar cualquier defecto que pueda afectar el rendimiento o la adaptación del imán a su uso previsto. La precisión es crucial en este paso, ya que cualquier pequeño error podría provocar problemas de rendimiento importantes en el futuro.
Paso 6: Recubrimiento y magnetización
Los últimos procesos de recubrimiento y magnetización se llevan a cabo una vez mecanizados los imanes en la forma y el tamaño requeridos. Para prolongar su vida útil y evitar la corrosión, se les aplica una cubierta protectora. Dependiendo del uso previsto del imán, los recubrimientos más comunes son níquel (Ni), zinc (Zn) u otros compuestos protectores.
Los imanes pasan por un último proceso de magnetización tras el recubrimiento. Durante la magnetización, se utiliza un campo magnético externo para alinear los dominios magnéticos del material, activando así sus propiedades magnéticas. Esta etapa garantiza que el imán pueda funcionar según lo previsto y alcance su máximo potencial magnético.
Una etapa importante es la magnetización, ya que perfecciona las características de rendimiento del imán y activa su campo magnético. La fuerza, estabilidad y resistencia a la desmagnetización del imán dependen del tipo y la intensidad del campo magnético aplicado durante esta operación.
¿Cómo elegir el tratamiento de superficie del imán SmCo?
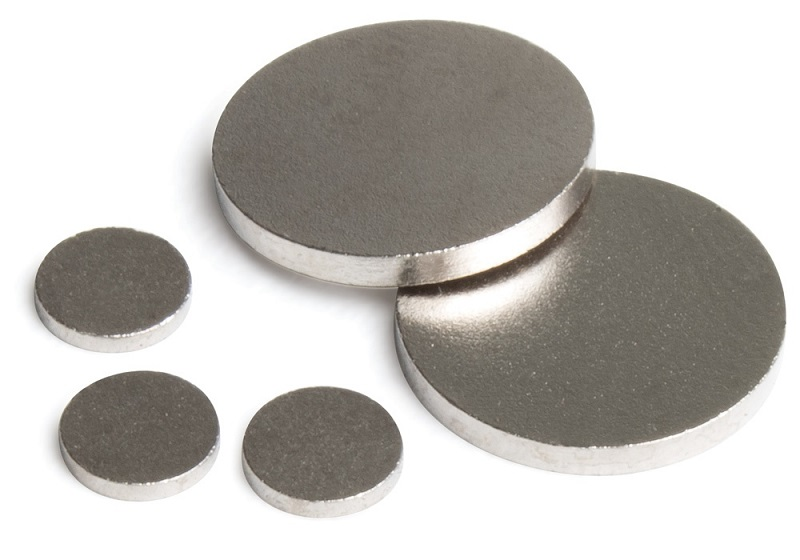
La vida útil de los imanes de SmCo se mejora considerablemente mediante el tratamiento superficial. Se utilizan diferentes recubrimientos para protegerlos de la oxidación, el desgaste y la corrosión según la aplicación. Los dos tratamientos superficiales más utilizados para los imanes de SmCo son los de níquel (Ni) y zinc (Zn). Especialmente en entornos exigentes como el marítimo o las altas temperaturas, estos recubrimientos prolongan la vida útil y el rendimiento del imán. El tratamiento superficial debe seleccionarse teniendo en cuenta el entorno en el que se utilizará el imán y el grado de protección requerido.
Ventajas y desventajas de los imanes de SmCo

Aquí están los beneficios y desventajas de los imanes SmCo
Ventajas
Las características superiores de los imanes de SmCo (alta densidad energética, gran estabilidad térmica y resistencia a la corrosión) son ampliamente reconocidas. Para usos en entornos de alta temperatura, como en los sectores aeroespacial y automotriz, son ideales, ya que pueden operar a temperaturas de hasta 350 °C. Los imanes de SmCo también presentan una alta coercitividad, lo que significa que son resistentes a la desmagnetización.
Desventajas
Si bien los imanes de SmCo ofrecen varias ventajas, son más frágiles que otros tipos de imanes, como los de NdFeB. Esta fragilidad aumenta su susceptibilidad a impactos o roturas por tensión. Además, el coste de producción de las materias primas influye en su tendencia a ser más caros. Si bien destacan en condiciones exigentes, su elevado precio puede resultar prohibitivo para algunos usos.
Campos de aplicación de los imanes de SmCo
Los imanes de SmCo se aplican en una amplia gama de sectores y usos. Componentes clave en sectores como el aeroespacial, el militar y la electrónica son sus excelentes propiedades magnéticas y su estabilidad a altas temperaturas. Los imanes de SmCo se utilizan en sistemas de propulsión y sensores que requieren una larga vida útil a altas temperaturas en aeronaves. Además, son vitales en motores eléctricos para coches eléctricos y equipos médicos como las máquinas de resonancia magnética. Además, demuestran su adaptabilidad en numerosos sectores los sistemas de levitación magnética, las turbinas eólicas y los sensores automotrices que utilizan imanes de SmCo.
Conclusión
Sus fuertes propiedades magnéticas, estabilidad térmica y resistencia a la corrosión hacen de los imanes de SmCo un material muy valioso. Estos imanes se fabrican mediante métodos precisos que incluyen la preparación del material, la sinterización, el mecanizado y el recubrimiento. Si bien presentan ciertas desventajas, como la fragilidad y el coste, sus ventajas especiales los hacen absolutamente esenciales en aplicaciones importantes. Ya sea que trabaje en el sector aeroespacial, la electrónica u otro, conocer cómo se producen los imanes de SmCo le permitirá valorar su papel en la tecnología contemporánea. Los imanes de SmCo son un componente esencial en los sistemas de alta tecnología, ya que su adaptabilidad, sumada a las sofisticadas técnicas de fabricación, garantiza que siempre inspirarán la creatividad en diversos sectores.