Tabla de contenido
Los imanes permanentes de NdFeB (neodimio, hierro, boro) y SmCo (samario, cobalto) tienen numerosas aplicaciones en la electrónica (altavoces, auriculares), las energías renovables (turbinas eólicas), la industria médica y la automoción (motores, frenos, embragues). Estos imanes son valiosos para diferentes aplicaciones debido a sus propiedades excepcionales, pero algunos factores ambientales afectan su rendimiento. Para proteger estos imanes del efecto de los elementos ambientales como la corrosión, la temperatura y la humedad, las superficies de estos imanes deben recubrirse con capas protectoras. Cuando los imanes se exponen a condiciones ambientales de alta humedad y temperatura, la superficie de estos se daña y el rendimiento y la eficacia se ven afectados. El costo del proyecto o producto aumenta debido a la reparación y el reemplazo de los imanes. Los imanes pueden funcionar mejor y durante más tiempo y el producto es económico si se realiza un recubrimiento de superficie de alta calidad.
En este artículo se analizan y describen las diferentes técnicas y métodos de protección de superficies para imanes permanentes, con sus ventajas y desventajas. También se describen los criterios para la selección de los materiales de protección adecuados para los imanes permanentes, con el fin de orientar e informar a las industrias manufactureras y a los clientes.
La necesidad de protección superficial de los imanes permanentes
Las características materiales de los imanes permanentes los hacen muy vulnerables a la corrosión y otros efectos ambientales. Los imanes permanentes más vulnerables son los imanes de neodimio-hierro-boro (NdFeB), que tienen una naturaleza oxidante y son muy propensos a la corrosión o problemas superficiales al exponerse a un entorno de humedad y corrosión. La naturaleza corrosiva de estos imanes es riesgosa y no es adecuada para aplicaciones duraderas y de alto rendimiento.
En este artículo se analizan y describen las diferentes técnicas y métodos de protección de superficies para imanes permanentes, con sus ventajas y desventajas. También se describen los criterios para la selección de los materiales de protección adecuados para los imanes permanentes, con el fin de orientar e informar a las industrias manufactureras y a los clientes.
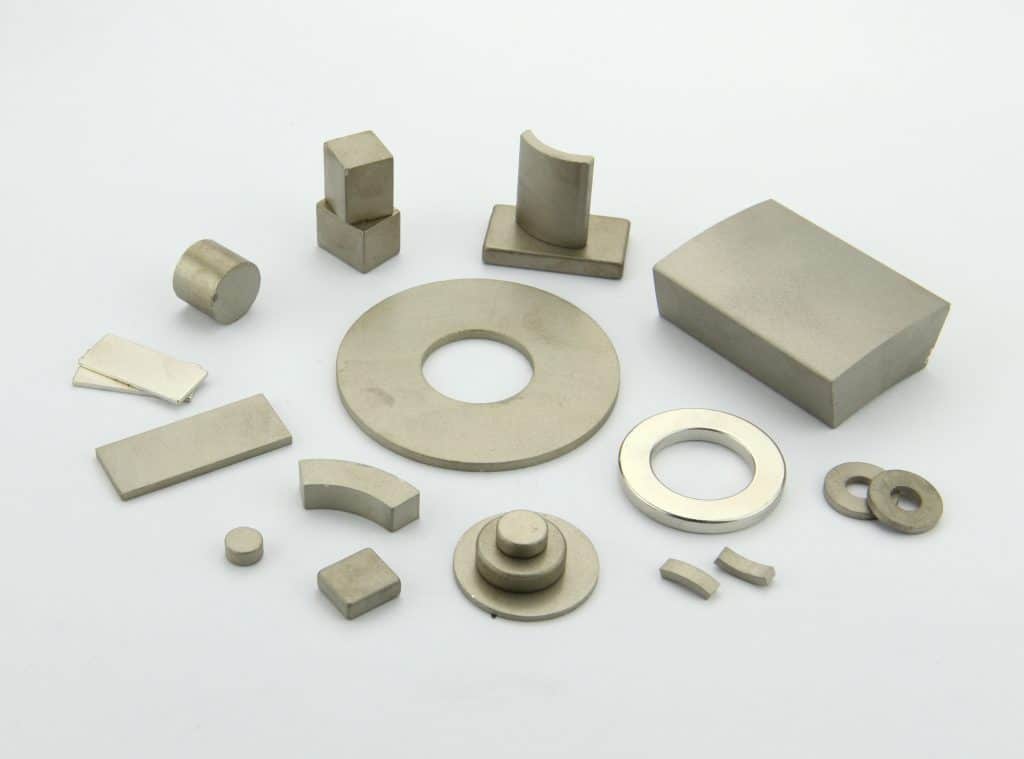
Sensibilidad y susceptibilidad de los imanes al ambiente corrosivo:
Las propiedades magnéticas de los imanes permanentes, como el rendimiento y la resistencia, disminuyen gradualmente con la corrosión. El proceso de degradación de la superficie y la corrosión de los imanes se acelera con la exposición continua a sustancias químicas y a variaciones de temperatura y humedad. El rendimiento y la eficacia de los circuitos magnéticos se ven afectados y comprometidos, y también todo el sistema puede fallar incluso con una pequeña cantidad de efecto de corrosión.
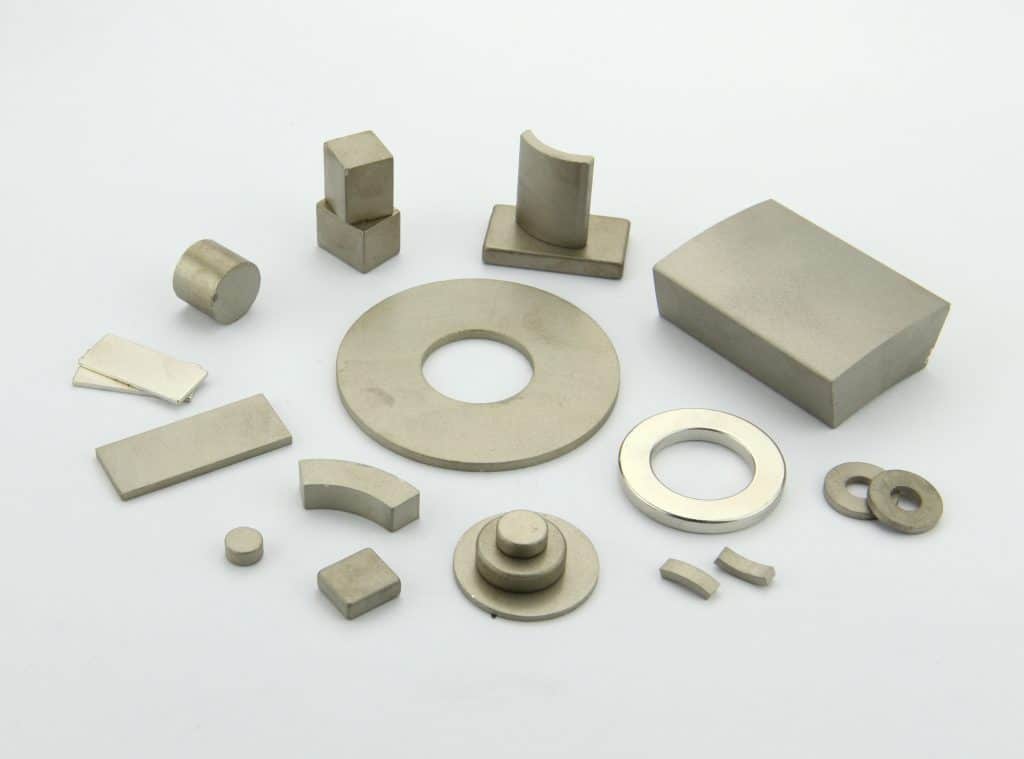
Mejorar la durabilidad y la vida útil de los imanes:
La durabilidad y la vida útil de los imanes se pueden mejorar mediante el diseño e implementación de estrategias o técnicas de protección de superficies efectivas. La capa protectora se produce en la superficie de los imanes con técnicas de recubrimiento y protege contra la humedad, la corrosión y los efectos de la oxidación, y también se aumenta la vida útil de los imanes. El rendimiento operativo general de los imanes se puede aumentar y se requieren menos costos de mantenimiento si se realiza una inversión en técnicas de protección de superficies. Las posibilidades de falla del equipo también se pueden mitigar con el uso de técnicas de protección de superficies efectivas y de alta calidad.
Lista de aplicaciones con requisito de alta resistencia a la corrosión:
Algunas de las aplicaciones donde se requiere una alta resistencia a la corrosión de los imanes permanentes se enumeran a continuación:
Instrumentos médicos:
Los instrumentos médicos, como los equipos de resonancia magnética (MRI) y los dispositivos de diagnóstico, funcionan con el campo magnético de los imanes permanentes. Los imanes permanentes proporcionan un entorno de campo magnético continuo en estos dispositivos para un funcionamiento duradero y confiable.
Automóviles:
Los imanes permanentes son los componentes principales de los sensores y motores de los automóviles y están más expuestos a los efectos ambientales, por lo que la superficie de los imanes permanentes utilizados en los automóviles debe estar recubierta con una capa protectora.
Motores (eléctricos):
Los motores eléctricos de barcos y unidades industriales expuestos a ambientes duros y húmedos son más vulnerables a la corrosión y otros procesos de degradación de la superficie.
Las industrias pueden garantizar la protección de la superficie de los imanes para un mejor rendimiento en entornos húmedos y corrosivos considerando la importancia del recubrimiento de la superficie de los imanes permanentes, discutida anteriormente.
Métodos habituales de protección de superficies para imanes permanentes
Existen en el mercado distintos métodos de protección de superficies para los imanes permanentes contra la corrosión y otros efectos de degradación de la superficie. A continuación se describen algunos de los métodos de protección de superficies:
Recubrimiento orgánico:
La superficie de los imanes permanentes se protege de los efectos de los productos químicos y la humedad mediante un recubrimiento de poliuretano y resina epoxi. Este recubrimiento se denomina recubrimiento orgánico. La resistencia al impacto y la propiedad de adhesión de los imanes aumentan con la formación de una capa protectora en la superficie de los imanes. Los imanes están coloreados y tienen un acabado suave con este tipo de recubrimiento, por lo que son muy factibles o adecuados para aplicaciones estéticas.
Tratamiento de oxidación:
Para los imanes de neodimio, hierro y boro (NdFeB) y SmCo (samario y cobalto), el método de tratamiento de oxidación es muy adecuado. En esta técnica, se forma una capa controlada de óxido en la superficie de los imanes. Con esta técnica, se aumenta la durabilidad y la resistencia a la corrosión de los imanes permanentes para las condiciones de ambientes húmedos y hostiles.
Método de enchapado:
Para la protección de la superficie de los imanes permanentes se utilizan técnicas de recubrimiento como el zinc y el níquel-cobre-níquel.
Recubrimiento tipo zinc:
El método de galvanización es muy adecuado y económico para proteger la superficie de los imanes permanentes durante un corto período de tiempo. La capa de sacrificio de zinc se forma en la superficie de los imanes, que se corroen como resultado del entorno corrosivo y protegen el imán. El método de galvanización no se utiliza generalmente debido a la protección a corto plazo contra el entorno corrosivo.
Recubrimiento tipo níquel cobre níquel:
Para la protección de la superficie de los imanes permanentes, el método más utilizado es el de níquel-cobre-níquel. Este método de recubrimiento de triple capa ofrece una alta capacidad de resistencia contra la corrosión al mejorar la adhesión y la dureza de los imanes permanentes. El recubrimiento externo de níquel proporciona una protección adicional y hace que esta técnica sea muy viable para diferentes aplicaciones de la industria.
Recubrimiento al vacío:
El recubrimiento al vacío se conoce como método de deposición física de vapor y es muy adecuado para condiciones ambientales adversas debido a su alta resistencia a la corrosión y sus fuertes propiedades de unión.
Recubrimiento químico:
Recubrimiento de aleación de níquel-fósforo:
En esta técnica, se aplica un revestimiento de aleación de níquel y fósforo a la superficie de los imanes permanentes para mejorar la resistencia a la corrosión en condiciones de humedad y corrosión. Este tipo de revestimiento se realiza en diferentes espesores para aumentar la resistencia al desgaste según los requisitos del entorno.
Método de recubrimiento de parileno:
Para lograr una excelente resistencia a la corrosión y un espesor extrafino de los imanes permanentes, el método de recubrimiento con parileno se utiliza ampliamente debido a sus propiedades altamente especializadas. Los imanes de formas complejas se recubren con esta técnica de manera fácil y perfecta sin afectar el rendimiento magnético. Esta técnica tiene aplicaciones en la electrónica y en equipos médicos.
Encapsulación a prueba de agua:
El encapsulado a prueba de agua es un método de protección completo en el que se aplica un revestimiento de material plástico o epoxi sobre la superficie de los imanes permanentes para protegerlos de las condiciones de alta humedad. La durabilidad y el rendimiento a largo plazo de los imanes están garantizados con esta técnica de revestimiento y brindan una solución viable para las condiciones ambientales del servidor. También hace que la superficie de los imanes sea a prueba de contaminación y humedad.
Comparación de las ventajas y desventajas de varios métodos de protección de superficies.
Al seleccionar el método de protección adecuado, se deben tener en cuenta los requisitos necesarios. Los factores de estos métodos de recubrimiento se analizan en la siguiente tabla.
| Resistencia a la corrosión |
| Complejidad de producción | Características de rendimiento | Escenario aplicable | ||
Recubrimiento de zinc | Medio | Bajo | Bajo | Resistente a la corrosión media, menos costoso, para condiciones no corrosivas. | Protección por un período de tiempo más corto | ||
Recubrimiento orgánico | Alto | Medio | Medio | Aplicable a formas complejas, proporciona protección contra la corrosión debido a productos químicos. | Para condiciones químicas y de alta humedad. | ||
Recubrimiento de níquel cobre-níquel | Alto | Medio | Medio | Ofrece una excelente resistencia a la corrosión, ampliamente utilizado. | Adecuado para condiciones húmedas. | ||
Recubrimiento químico (aleación de níquel-fósforo) | Muy alto | Medio | alto | Adecuado para condiciones severas debido a su alta resistencia a la corrosión. | Para aplicaciones marinas (altamente corrosivas) | ||
Pulverización al vacío/enchapado | Muy alto | alto | alto | Costo muy alto Resistencia a altas temperaturas y protección de superficies. | Para instrumentos de precisión | ||
Técnica de oxidación | Bajo | Bajo | Bajo | La estabilidad de la superficie es mayor, el rendimiento de la protección es más débil. | Adecuado para imanes SmCo | ||
Encapsulación de agua | Muy alto | De media a alta | De media a alta | Más adecuado para entornos submarinos y exteriores. | Estable durante un período prolongado de exposición a la humedad. | ||
Técnica de recubrimiento de parileno | Muy alto | Alto | alto | Más adecuado para aplicaciones sensibles y alta resistencia a la corrosión. | Para electrónica y medicina |
Cómo elegir la solución de protección de superficies adecuada
La selección del método de protección de superficie adecuado para los imanes permanentes es muy importante, ya que se garantiza el rendimiento y la longevidad. A continuación, se enumeran los elementos importantes que se deben tener en cuenta:
Alta resistencia a la humedad: Se debe utilizar una técnica de recubrimiento que tenga alta resistencia a la corrosión y a la humedad.
Estabilidad a alta temperatura: el recubrimiento que permanece estable en condiciones de alta temperatura.
Adecuado para aplicaciones saladas o marinas: El método de protección de la superficie es adecuado para soportar las condiciones del agua salada.
Durabilidad vs Costo:
Se debe preferir la durabilidad al costo de la técnica de recubrimiento porque algunos de los métodos de recubrimiento son costosos pero tienen mayor durabilidad y vida útil debido al uso de materiales y técnicas de aplicación de alta calidad.
Guía para la selección:
- Identificación del entorno de trabajo como industrial, interior y exterior.
- Tipo de elementos corrosivos como sal, químicos, agua.
- Requisito de desempeño
- Selección de técnica según requerimiento y presupuesto.
¿Qué podemos hacer para proteger la superficie de los imanes permanentes?
Contamos con amplia experiencia en brindar protección de superficies de alta calidad para imanes permanentes.
Nuestro equipo tiene amplia experiencia en la prestación de servicios de protección de superficies para imanes permanentes con profundos conocimientos y habilidades para la selección de la técnica adecuada con respecto a las condiciones de diseño.
Revestimiento | Nombre del procedimiento técnico | Color | Espesor (μm) | Duración (h) | Temperatura (℃) | Ambiente | ||
temperatura media del mar | Húmedo Prueba de calor | PCT | ||||||
Zinc blanco | Recubrimiento eléctrico | Azul | 4-10 | 24 | 48 | — | <160 | Temperatura normal |
Zinc coloreado | Recubrimiento eléctrico | De colores | 4-10 | 48 | 48 | — | <160 | Temperatura normal |
Ni químico | Recubrimiento químico | Plata | 8-15 | 96 | 300 | 48 | <200 | Entorno corrosivo |
Ni-Ni | Recubrimiento eléctrico | Plata + Blanco | 10-20 | 72 | 300 | 48 | <200 |
Entorno corrosivo |
Ni-Cu-Ni | Recubrimiento eléctrico | Plata + Blanco | 12-25 | 72 | 500 | 48 | <200 | |
Ni-Cu-Ni+Sn | Recubrimiento eléctrico | Plata + Blanco | 12-25 | 72 | 500 | 96 | <200 | Entorno corrosivo |
Epoxi pulverizado | Electroforesis | Negro o gris | 15-30 | 96 | 120 | — | <180 |
Entorno fuertemente corrosivo |
Epoxi Ni-Cu+ | Recubrimiento eléctrico +Electroforesis | Negro o gris | 25-45 | 500 | 1000 | — | <200 | |
Lubricante permanente | Recubrimiento eléctrico | Amarillo | 10-20 | 72 | 500 | 72 | -70~180 | |
Fosfato/Pasivado | Deposición química | Gris oscuro | 1-2 | — | — | — | <500 | Protección temporal |
Aluminio al vacío | Recubrimiento al vacío | Plata + Blanco | 2-10 | 100 | 500 | 72 | <500 | Temperatura fluctuante Ambiente |
Teflón | Recubrimiento eléctrico | Negro | 8-15 | 24 | 120 | 48 | <260 | Resistencia a altas temperaturas |
Tendencias futuras en la protección de superficies con materiales magnéticos permanentes
Esperamos el desarrollo y progreso de las técnicas de protección de superficies con el avance de la tecnología.
Tecnologías para la anticorrosión:
La vida útil y la durabilidad de los imanes permanentes aumentarán en condiciones ambientales severas con la invención de nuevas tecnologías.
Materiales innovadores:
Anticipándose a los nuevos e innovadores materiales para el recubrimiento de los imanes permanentes que puedan ofrecer alto rendimiento y durabilidad.
Respetuoso del medio ambiente:
Se están realizando trabajos de investigación y desarrollo para mitigar el impacto nocivo de estos recubrimientos sobre el medio ambiente.
Conclusión
Los imanes de neodimio, hierro y boro (NdFeB) son más vulnerables a la corrosión y a las duras condiciones ambientales, por lo que los revestimientos de superficie protectores son muy esenciales para estos imanes permanentes a fin de mantener el rendimiento y aumentar la durabilidad. La técnica de revestimiento de superficie adecuada y eficaz puede hacer que estos imanes sean muy útiles para entornos húmedos y corrosivos, pero también mejora el rendimiento y la durabilidad.
Para mantener las propiedades magnéticas durante más tiempo, es muy importante elegir la técnica de recubrimiento de superficie más adecuada para los imanes permanentes. Los riesgos y peligros ambientales se pueden reducir con técnicas de protección de superficies personalizadas.
Para obtener recomendaciones y soluciones profesionales, animamos a los clientes a que se pongan en contacto con nosotros en cualquier momento. Tenemos una gran experiencia y conocimientos diversos en métodos de protección de superficies que le brindarán un servicio de calidad.
Póngase en contacto con nosotros para obtener orientación y soluciones sobre técnicas de protección de superficies y cómo seleccionar la técnica adecuada para sus imanes. Podemos aumentar el rendimiento y la durabilidad de sus imanes permanentes con su cooperación.